Allan Rumpf and his family pay attention to the numbers when it comes to major decisions such as buying seed drills. He farms 9,400 acres at Battleford, Sask., with his brother Perry and father Henry.
When they ran the numbers on the pair of ConservaPak ILS drills they bought in 2005, they received a pleasant surprise. Without factoring in the better grade they received on their wheat this fall, the direct benefit of the purchase was $50,000.
“We all work together on the financial breakdown,” Rumpf said.
“Before we made the decision to buy new drills, we figured there was going to be a significant financial gain. We just didn’t know how much.”
Read Also
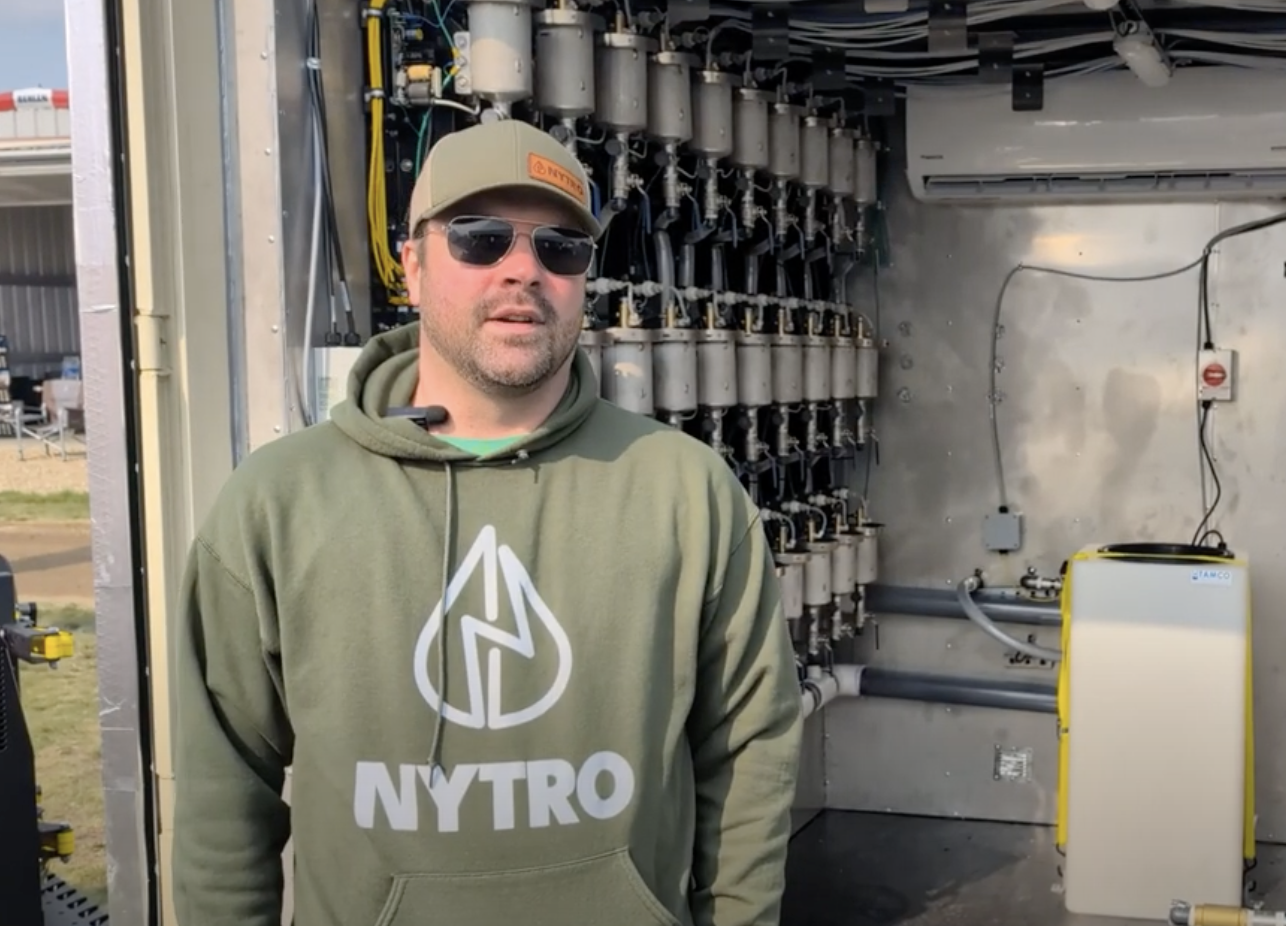
VIDEO: Green Lightning and Nytro Ag win sustainability innovation award
Nytro Ag Corp and Green Lightning recieved an innovation award at Ag in Motion 2025 for the Green Lightning Nitrogen Machine, which converts atmospheric nitrogen into a plant-usable form.
The Rumpfs had been zero till seeding since 1997 with a pair of 40-foot disc seeders. In 2005, they got rid of the discs and bought two ConservaPak 56-foot Platinum ILS drills. They kept both Flexi-Coil 2320 air carts and both New Holland 9884 tractors.
Their commitment to the new seeding system was strong so they sold their harrows.
In their 2004 seeding operation, each tractor logged 380 hours pulling a 40-foot drill. In 2005, each tractor logged only 250 hours pulling a 56-foot drill. That cut 260 tractor hours from their seeding operation.
If an operator averaged 12 hours per day, it took each tractor 32 days to seed 4,700 acres with the discs. With the same operator working the same 12 hour day, but pulling the 56-foot ILS, it took 21 days to seed the same 4,700 acres, effectively cutting 11 days off their seeding schedule.
“We were delayed by rain at one point,” Rumpf said. “So there were two days we started at 4:30 in the morning and went through until 10 p.m. We did 800 acres each day. That’s two operators, two tractors and the two new drills.”
He said a good truck driver is required to keep everything rolling. They still have the old 220-bushel tanks, but once they upgrade that part of the lineup, their field efficiency should increase again.
Cutting 11 days from the seeding period proved beneficial.
“The benefit stays with you the whole summer,” Rumpf said.
“Our wheat came up right away. Everything was even and the fields remained uniform all summer. Each field matured at the same time. All the wheat graded No. 2, right across the board. Nothing graded lower. We attribute that to the seed drill. Our wheat averaged 52 bushels across the whole farm.”
Hair pinning had always been a problem with the discs.
“Seed placement might have been good, but the straw was pinched down in the trench and it dried out the soil,” he said.
“We had one field of barley stubble last spring that was in terrible condition. It was all lumps and clumps. But we had already sold our harrows, so we direct seeded canola right into the mess. That canola came through beautifully. It was 30 bu. where we got frost and 45 bu. where there was no frost.”
The Rumpfs figured each tractor used about 36 litres of diesel per hour. If diesel is factored at 64 cents per litre, 380 hours would cost $8,755 for the year. If the annual time is reduced to 250 hours, the fuel cost is $5,760 for one tractor.
The annual fuel savings amounted to $2,995 per tractor, or $5,990 for two tractors.
Although they had no way of measuring opener resistance in the soil, the Rumpfs think the 56-foot ILS requires less power than the 40-foot disc machine. Some of this is attributable to the row spacing. The discs had been on 10.5-inch row spacing while the ILS is on a 12-inch row spacing.
“The new drills pull much easier than the discs,” Rumpf said. “We have hills here where we could not pull 40 feet of disc machine up the slope unless we pulled it up out of the ground. These new drills are much easier to pull. A lot of that is the big wheels. It pulls just like a cultivator.”
The Rumpfs estimated that each of their disc seeders required up to 350 hours of maintenance per year. Although they have only one year under their belts with their new ILS drills, the experience of other owners indicates that 15 hours per drill should be adequate, which could potentially save them 335 hours per year on each of the two drills.
Parts are another consideration. Their experience with the two disc machines documented an average parts cost of $10,800 over a three-year period for each disc seeder.
The estimated three-year parts cost on the ILS would be about $3,700 for fertilizer tips and hard surfacing, for a potential saving of $7,100 over a three-year period for each drill. The financial value of the additional saving on labour will vary from farm to farm.
They stayed with the disc setup as long as they did because of rocks on a section of their land. They were concerned that a shank-type opener would pull up too many stones.
However, the ILS is able to adjust hydraulic pressure on the fertilizer shank, reducing the number of stones rolled out of the ground. As well, the individual hydraulic trips allow each shank to lift over a stone rather than pulling it up.
“The hydraulic trip was 100 percent every day,” Rumpf said.
“Some of our stony land has been farmed with the discs since 1997, so you would expect to pull up a lot of stones if you put a shank through. But we were surprised at the small number of stones we got. Nothing big. A lot of them were the size of a football or a basketball, but the big ones stayed buried. The ILS doesn’t grab and hold on. It just trips and rides over.”
That is good for their maintenance budget.
“We did not have a single broken part on either machine through the entire 9,400 acres, and that includes the stony fields.”
In their financial breakdown, the Rumpfs figured they saved $13,720 on fuel and parts for the disc drill and harrows.
They factored their tractor expense at $70 per hour for both seeding and harrowing operations. They eliminated 360 hours of tractor time from their overall farming operation for an additional cost saving of $25,200.
They factored their labour at $15 per hour for both shop time and machine operator time. An estimated time saving of 1,030 hours resulted in an additional cost saving of $15,450.
Adding up the three cost categories creates a total estimated saving of $54,370.
But what about the cost of two new 56-foot ILS drills?
It’s a big investment, Rumpf conceded, but he said two 40-foot disc drills also represented a big investment.
“When we bought the ILS machines last year, a new disc machine was going to cost us $3,000 per foot. The ConservaPak was in the area of $2,400 per foot. So if you compare a 40-foot disc to a 56-foot ILS, it’s getting pretty close. Not quite a wash, but almost.”
He admitted their fields were smoother with the disc seeders.
“You feel it in the combine, especially if you’re going across the rows. The disc machine gave us a nicer field finish.”