Moving grain is a dangerous business, whether on the farm or in a commercial setting. P&H took the initiative over a decade ago to address safety in its facilities.Â
“We’ve been upgrading our safety equipment over the past 15 years. We’ve installed sensors and hazard monitoring equipment throughout our facilities. The systems automatically shut the equipment off before anything dangerous starts to happen,” says P&H construction engineer Zach Harrison.
“For example, if a belt starts to rub on the side, that could create enough friction heat to ignite grain dust. Well, the way we’re set up now, a sensor will detect that heat and shut down the appropriate motors. If there’s a bearing or shaft anywhere creating a problem, the system knows.”
Harrison says trigger points for the various sensors are carefully calculated to create a high degree of safety. Thresholds for safe operating temperatures on different machines are established by researchers whose recommendations are incorporated into all new handling facilities. If one safety system goes down, all equipment comes to a halt until the issue is resolved.Â
Grain dust has always been the major enemy of grain elevators in terms of human respiratory problems and catastrophic explosions. Harrison says P&H has done three things to deal with grain dust.
- Grain now moves within enclosures rather than out in the open. Dust remains in a controlled environment whenever it’s moving in the plant.
- Suction fans are located at strategic points where dust is most easily removed from the grain. This dust is drawn through ductwork and deposited in a sealed chamber. If there are duct problems, everything stops.
- In the past year P&H has enlisted an independent third-party engineer to inspect all plants and make further recommendations to improve dust handling. That inspection includes the Dugald plant, even though it’s brand new.
What to do with captured dust is always a perplexing question. It has nutrient value for livestock, but handling pure dust is a nuisance. At Dugald, dust is blended into screenings to reduce the odds of it blowing away in a breeze. It’s then trucked to a local cattle producer, who feeds it to his cattle. He comes twice a week to pick up screenings, eliminating the storage issue for P&H.
Keeping staff safe while shuttling cars was a big design consideration. The engineers decided to erect fall protection cables that allow workers to climb to the top of cars while fastened to a cable safety harness.
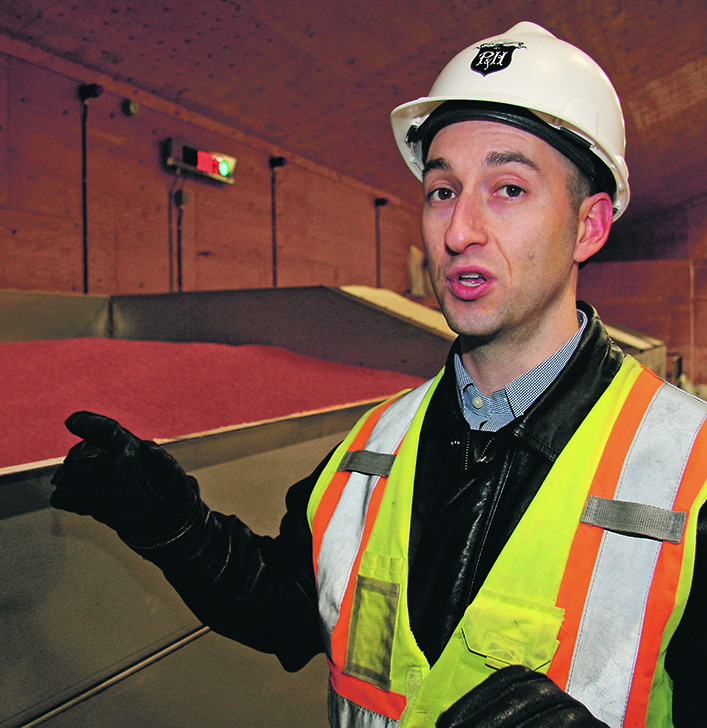
One tower is at the fertilizer shed, the other at the main grain handling plant. If a worker slips and falls, the harness is secured to something akin to a zip line.Â
“Typically, a rail facility like this receives fertilizer and ships out grain. Two distinct functions, so we have one tower for each end of the operation. The worker goes up the gangway and attaches a lanyard over the cable so he’s well secured when walking along the tops of the rail cars. If anything should happen, he’s secured to the cable so there’s no injury and nobody hitting the ground.
“When we’re loading 15 grain cars an hour, it gets pretty busy. 150 cars and 15 hours to load it. That train does not stop. It’s on automatic cruise control and it keeps slowly moving forward while we’re loading. The last thing we want is an injury. Anytime.
“One guy goes along opening the cars and looking down to check to see if there’s leftover grain that’s gone mouldy or an animal got in there and died. That car doesn’t get filled.
“We also make sure a fertilizer car never gets filled with grain. Can’t happen. The second guy comes along behind and closes the lids once the car is filled.”
Another big improvement in the eyes of staff is the new basement. In older elevators, the basement was a dark, damp and foreboding place. Workers had to go down there because that’s where the mechanization monster lived.
The new-era grain elevator basement is wide open, dry, well lighted and dust free. Staff have space to inspect and work on equipment.
Numbers tell the story
The new P&H Dugald facility features expanded operation, 13 hours a day, six days a week. By building east of Winnipeg, the company says it is making a long-term commitment to farmers north, east and south of the city.
Numbers tell the story:
» 25,000 tonne grain elevator
» 6,000 tonne dry fertilizer shed
» 7,800 sq. ft. Agrichemical Warehousing Standards Association heated chemical shed
» seed treatment facility
» 150 car CN loop track
» full agronomic services, from soil testing to field scouting