Driverless tractors are here.
Robotics and guidance have met out back of the barn, and across the globe tractors without operators are being birthed. No longer part of imagination, they are a reality that many producers could get behind, or even in front of, with confidence.
The North American Great Plains, Western Australia and the European and Asian steppes are obvious candidates because of their vast fields, but the technology being used in the machines of today is not limited by mile-long passes in a field.
Read Also
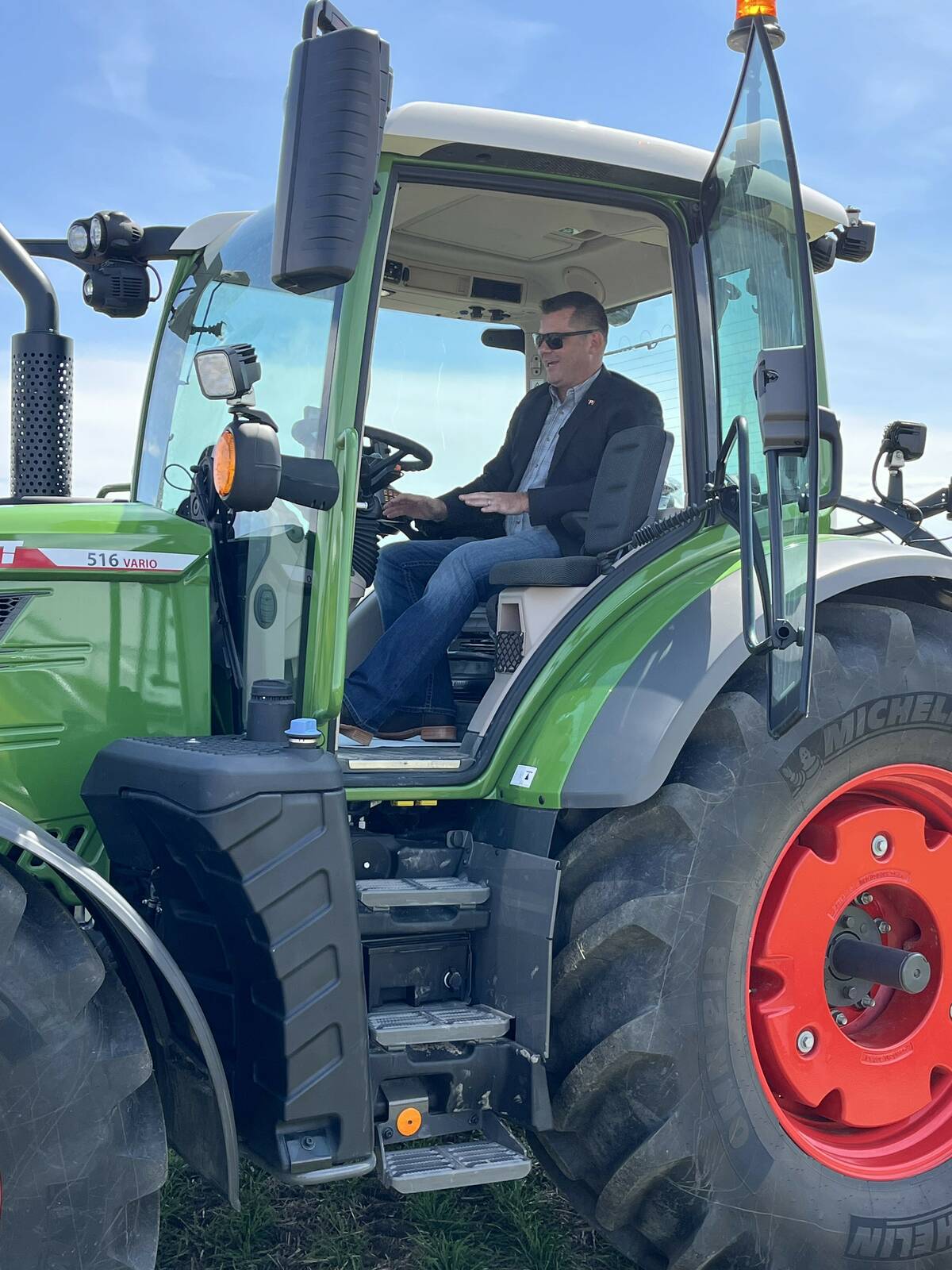
Farming Smarter receives financial boost from Alberta government for potato research
Farming Smarter near Lethbridge got a boost to its research equipment, thanks to the Alberta government’s increase in funding for research associations.
The technology is capable of short turns in tight spaces. The first applications have been working for several years in orchards and vineyards, where accuracy is crucial.
Acres are measured in weeks in the field in broad acre agriculture, and the further north one travels in this hemisphere, the shorter the time farmers have for their tasks, so efficiency is critical.
Terry Anderson, who has been designing and building farm machinery for the Great Plains and Prairies for more than 40 years with seven companies under his belt, has turned his attention to autonomous tractors.
Autonomous Tractor Corp. is now marketing a driverless system so that tractors can perform all normal fieldwork with the added benefit of energy-efficient diesel-electric power.
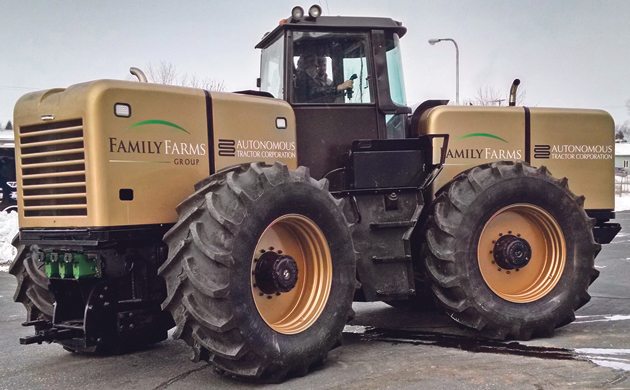
Anderson said it is a logical progression of agriculture and one he has forecast for the industry for decades.
Today, for about US$10,000, the North Dakota company will add its fully autonomous control system to an existing tractor that’s already been converted from conventional diesel-mechanical drive to its eDrive diesel-electric system.
The system, called AutoDrive, can be installed only on an eDrive tractor.
It shouldn’t be confused with auto-steer, which requires an operator in the cab at all times.
AutoDrive allows a tractor to operate when the cab is vacant. The operator can be on a second or third machine, mapping the next field or managing the tender vehicles.
Electric motors aid in the ATC system because of their precision of operation for guidance, relying on individual wheel motors rather than more complex transmission and mechanical drives.
However, these too have become much more precise tools over the past few years, meaning the remote guidance technology works nearly as well with existing platforms.
John Deere began summoning unmanned grain carts to its combines four years ago, but that project remains largely on the drawing boards in Iowa.
Also in Iowa, farm equipment manufacturer Kinze has been developing its own version of a tractor-towed grain cart system, which would automatically manage the grain haul from combine to trucks and trailers.
So inspiring were these mostly unavailable tools that a young Manitoba farmer took the cheap guidance tools available for unmanned aerial vehicles and adapted them to a tractor on his family farm.
The result was a grain cart that came when it was called.
Matt Reimer of Killarney became an instant farm celebrity when he transferred the auto-guidance from drones to an eight-year-old John Deere seven series tractor via an Outback steering control and some wheel camber sensors.
That farming hack and Reimer’s insistence that his work remain open-sourced is helping to usher in what the young farmer hopes will be a new age of farmers modifying more than just a hitch or an opener on their modern equipment.
“I want others to be able to build on this, with what they know,” he said.
“As farmers, we all can see what we would do to change our equipment. This opens that up quite a bit.”
Reimer said drone tractors during seeding or sprayers later in the season are natural steps for the technology, making farmers more efficient and less dependent on short-season staff.
“Machines are often better at repetitive things than people,” he said. “It frees up people to be best at what they do.”
At the Agritechnica farm show in Germany five years ago, Agco chief executive officer Martin Richenhagen debuted a fully autonomous drone tractor from Fendt, working as a mirror to a leader unit in a German field.
“We have the technology today,” he said in an interview a year after that launch. “We can make it safe and profitable for farmers, potentially better for the environment through efficiencies.”
Richenhagen said at the time of the release that regulatory hurdles would be a likely limiting factor for farm adoption in the United States, but he could imagine the machines operating autonomously in other, less “litigious parts of the world.”
A month ago, guidance and technology company Trimble debuted its first autonomous tractor at an event in Nevada. The Case IH tractor made its way around an obstacle course in the desert, showing off an ability to stop when unplanned events interfered with its LIDAR readings.
Designers said the machine was mostly a stock tractor that had its steering and some other functions “hijacked” using off-the-shelf Trimble and other third party hardware and software that is already in the marketplace.
The company said most of the required guidance and other electronic components are already in the machines.
Fiat’s Case IH and New Holland farm equipment companies took the work of Reimer and prototypes by Deere and others one step further this fall.
Case IH released a version of a cabless tractor based on the popular Magnum platform. Testing in Kentucky showed the machine is capable of most field operations, offering the possibility of both drone applications and independent fieldwork, supported by an operator either at the field or back at the farmyard.
The operator manages rather than drives the units, providing direction and control from a tablet in the field or a desktop computer in the office. Sensors provide feedback and mapping can give autonomous navigation and work plans.
A cabbed version of the machine from New Holland also debuted in Iowa. The equipment drew large crowds of producers looking for efficiency solutions that would help meet skilled farm labour shortages.
Leo Thompson, who farms 3,500 acres in Minnesota , was at the Farm Progress Show in Boone, Iowa, when Case IH removed the cover from its cabless Magnum.
“This does make it real for me. I can see one on our place.”
“We have to till a fair bit where we are, and a couple of these would cut our costs for labour, which is getting harder to get anyway,” he said.
“I’d still want a cab if they offered it, just so we could drive it the old-fashioned way too.”
Transport between fields might still be an issue, he added, even in a world where driverless cars are becoming a reality.
Dan Halliday of New Holland said radar, LIDAR and camera technologies developed for collision avoidance have improved the systems and significantly reduced costs.
“We need to know what farmers want these machines to do and which equipment they will want it on,” he said.
“We have some pretty good ideas, but before we launch these types of technology into the market, we want their input.”
The Case IH machine is based on the 370 horsepower Magnum chassis with the CVT drive system. The 8.7 litre FTP Cursor 9 puts the machine in the row crop and large forage production sectors.
New Holland’s concept machine, a T8 with 435 h.p., was already 90 percent automated before the company added the autonomous features. Both machines tread on the air seeder workloads in the U.S. Great Plains and Canadian Prairies.
Meanwhile, ATC feels it has what it needs to proceed with its robotic units. The system’s four stages are installed one at a time as farmers gradually become acquainted with the new technology. The tractor can operate independently of a human by the time Level 4 has been reached.
A cab wasn’t part of the company’s prototypes, but is now so that a human can jump into the cab and take over, said Anderson, vice-president of ATC and chief designer of the technology.
He said AutoDrive relies on the company’s Laser-Radio Navigation System for sub-inch positioning data and FieldSmart artificial intelligence software, which allows the tractor to be “trained” without programming.
“Sonar systems provide full perimeter safety, and pan-tilt cameras communicate via cellular to allow you to monitor progress and remotely resolve issues at any time.”
Anderson said he decided years ago that he could convert any tractor to diesel-electric and then add an autonomous control system. However, that’s a big chunk to bite off all at once, so he split the system into four stages:
Level 1: The basic system requires the operator to manually drive the diesel-electric modified tractor.
Level 2: This advanced GPS guidance system puts two RTK transponders at the edge of a field on tripods. As well, two units on the tractor are a fixed distance apart, which allows the system to create four triangles.
“Four positioning triangles lets you be pretty damned accurate.”
Anderson said this doesn’t solve the problem of total GPS failure, which is usually caused by major solar disruptions rather than by problems in the ionosphere. Level 2 has major advantages over other GPS based systems, he added.
“What’s typically done … is they use a (filter), which takes all the data up to a point and process it to arrive at a uniform average. That’s garbage in, garbage out,” he said.
“With two fixed RTK stations in the field, we know whether or not the signal we’re receiving is legitimate. In the same way, two units on the tractor provide a check to see if we have valid signals.
“If we position the two tractor units precisely seven feet apart and the equipment suddenly says they’re nine feet apart, then we know there’s a problem. So rather than let the tractor take off on a 90 degree turn and hit something, we can determine ahead of time that we have faulty signals so we alert the system to stop the tractor.”
The field RTK tripods are typically located at opposite ends of the field to minimize the impact of the ionosphere. Anderson said ionosphere thickness changes, which is why GPS signals are refracted and become unstable.
Level 3: The next step is to install a gyro-mounted laser to steer the tractor, using GPS to check it for accuracy. Laser gyro uses two electronic beams moving opposite to each other over the same path. Interference between the two beams indicates patterns of rotation. This data can then control the guidance of anything from a tractor to a jet liner or a submarine.
ATC is working with Advanced Navigation, an Australian company that’s been developing laser gyro guidance. Anderson said they have done research showing how the laser gyro can enhance the accuracy of GPS.
Level 4: ATC takes it one step further when it installs a radio system on top of the RTK GPS and laser gyro systems. This final step provides a fully autonomous driverless tractor that the farmer can set up in a field and leave it to do its work.
“When we go fully autonomous, we need absolute knowledge of where that tractor is in the field. When we took that to Big Iron in Fargo, (North Dakota, two years ago), we found a lot of people weren’t ready for it yet,” Anderson said.
“We’ve found we need the first three steps so the farmer develops the confidence to let the tractor work on its own. We won’t install Level 4 until the farmer is comfortable with the first three.”
He said his quoted price of $10,000 includes the RTK GPS, laser gyro and radio signal system. Each system is applied over the previous system so that all systems are working together in Level 4.
“For example, the two units on the cab roof give you Level 2,” he said. “Then you simply add something inside them to get to Level 3. Then you add something else inside them and that puts you at Level 4.”
Jim Walker, who runs Case IH in North America, said his company wanted to get farmers’ input into autonomous farm equipment and felt the best way was to bring it to a farm show and ask them.
He said his company plans to offer the technology in cab-free and standard designs, “provided that is what farmers tell us they want.”
Halliday said producers might find they want to run one machine and have one or more drones in the same field.
“Combines could also be a natural for this technology,” he said.
Leo Bose of Case IH said the agricultural economy has become so demanding of farmers that this type of equipment fits into the “high-efficiency farming practices of the future.”
While driverless tractors, cab or not, would likely be largely ignored by most of the public when they are in the field, transporting on the road would likely draw some attention, said Walker.
Halliday said the prototypes are getting “a good work out in the field” at New Holland, but farmers might be able to order their own in as little as three years. He said they might even be able to retrofit recent models for autonomous operation.
Both brands are using technology from Utah-based Autonomous Solutions Inc., which offers kits for a variety of equipment.
While the Case IH prototype is missing its cab, the only other items easily differentiating the New Holland from a manned vehicle are the extra wi-fi antennas, four cameras on the corners of the cab and the radar and LIDAR units on the nose of the machines.
Walker said regulatory jurisdictions will have something to say about large autonomous vehicles but feels that acceptance isn’t far away.
Meanwhile, Thompson offered this assessment: “I really would buy one, if the price made sense. I can calculate the payback for the bank.”