Western Producer reporter Ed White is following construction of several grain terminals from the ground up. This is the sixth in the series.
WILKIE, Sask. – Ellwood Sawby is an effective salesman.
He has not only convinced farmers across the Prairies to buy his grain pump systems for on-farm storage, but also convinced one of the world’s grain trading giants to pour tens of millions of dollars into a prairie-wide grain elevator system using a design that nobody has ever tried on a large scale.
Read Also
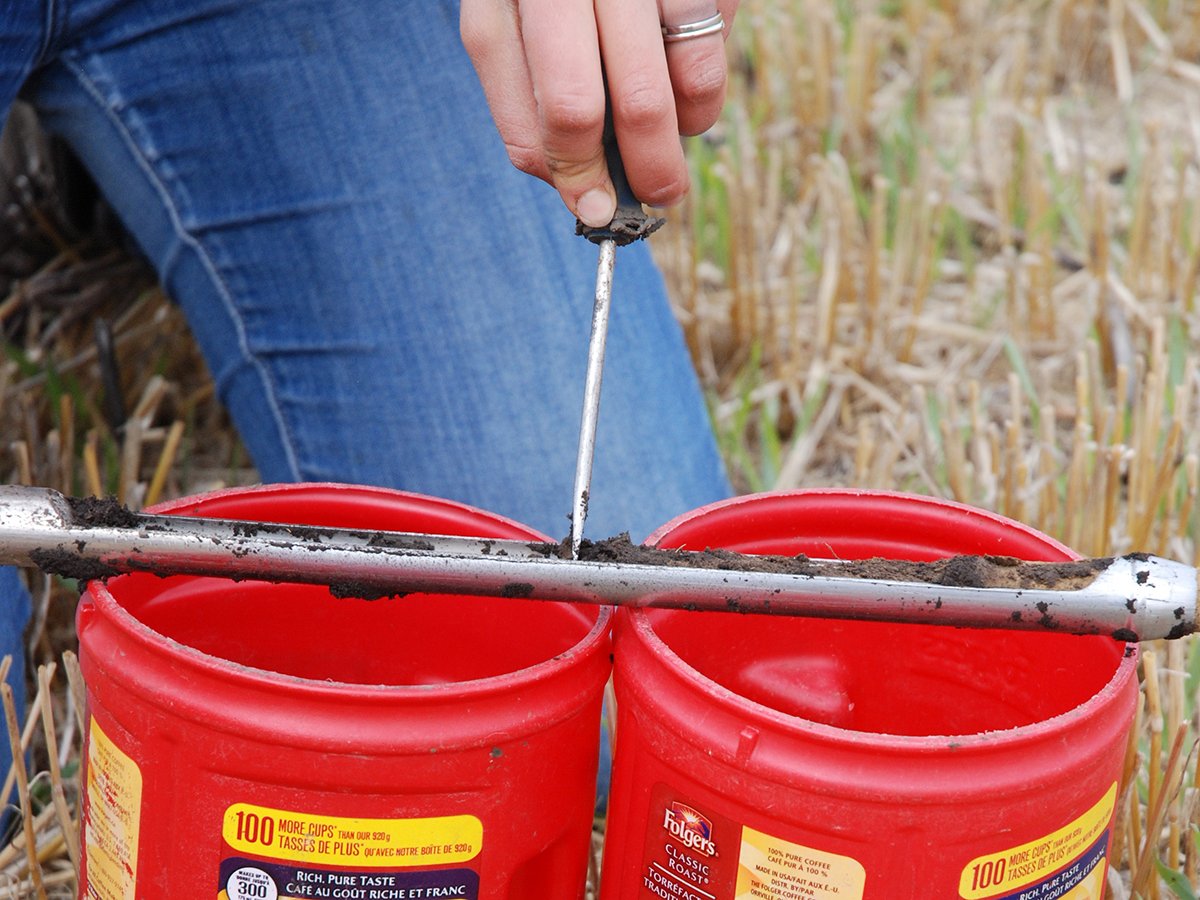
Federal government supports soil health strategy
Sophie Beecher, director general at Agriculture Canada, said at a soil conference in Winnipeg that the feds support the idea of a national soil health strategy.
“This is the first one they ever ran in the history of the world,” said a thrilled Sawby, moments after workers at the Louis Dreyfus grain collection facility conducted a short run of the 16-inch-pipe grain pump system.
The Louis Dreyfus facility at Wilkie is very different from concrete elevators. Rather than one or two main structures, it is composed of more than a dozen huge steel bins and many smaller bins strung together by the loops of the grain pump system.
The steel facility here is a cobweb of utilitarian considerations, a simple laying out of horizontal lines of conveyance.
Concrete elevators go up. This facility goes sideways.
As Sawby walked around the site he seemed delighted by the growth of the giant operation, the highest profile use of the Hutchinson Grain Pump that he promotes so intensely. He talked to worker after worker about how construction was progressing, seeming on the verge of hugging everyone he came across, like a proud father trying to spread the joy of a bouncing baby.
Sawby’s company, Skyway Grain Systems Inc., from Airdrie, Alta., built three major grain collection points for Louis Dreyfus last year and is building three more this year. But this facility is the only one using such a large gauge chain conveyor system. The others have used 10 inch pipes, this uses 16 inch. Concrete elevators and existing large steel facilities generally use a belt and bucket system to move grain. The chain loop system here is completely different.
While Sawby seems convinced the grain pump-steel bin design will work as well as any concrete elevator or traditional steel facility, he happily acknowledges it’s a high stakes roll of the dice.
“Louis Dreyfus is taking a real chance. It’s a gamble,” said Sawby, who drove from the Western Canada Farm Progress Show in Regina to inspect the building site.
“The top engineer at Pioneer said ‘Jesus, Ellwood. We never would have taken the chance that Louis Dreyfus has.'”
But the untried nature of this facility doesn’t faze Sawby. He thinks Louis Dreyfus became a multinational giant by taking intelligent risks, and he wants to do the same thing.
Most of the major grain facilities being built across the Prairies are large concrete elevators, such as the the Saskatchewan Wheat Pool elevator in North Battleford that this series has been following.
Two other major elevators are also being built in North Battleford – both of them concrete giants that stand like monoliths.
The only concrete in this structure is in the ground level flat pads that the 73,000 bushel bins sit on, and in the driveways grain trucks will use when they deliver.
And unlike the concretes, which aren’t designed to store grain but rather to push it through fast, this facility can store more than a million bushels.
Steel facilities are cheaper than concrete elevators. This one will cost about $6 million. Concrete elevators the size of the ones being built in North Battleford cost more than $10 million.
No one in the grain industry thinks steel is as good as concrete. Most say concrete elevators keep grain in better condition. With steel, heating, sweating and grain quality deterioration pose greater risks.
And concrete doesn’t wear out as fast as steel. Concrete elevators are designed to last at least 50 years. Most steel bins aren’t expected to last more than 30.
Charles Dietrich, Saskatchewan Wheat Pool’s manager of engineering, said he has seen much wear and tear in the large steel bins attached to the pool’s wooden elevators. One has even failed after only 10 years, though most last considerably longer.
Steel is also susceptible to strong wind gusts, a common phenomenon on the Prairies. Steel bins are especially vulnerable when they are empty, Dietrich said. They tend to be empty in July and August, before the new crop is harvested, which is exactly when there is the greatest danger of windstorms.
That’s why the pool decided its new network of elevators would be concrete. Besides, for a facility like the elevator in North Battleford, steel wouldn’t save the pool money. The company’s new elevators are based on having many small bins that hold tightly controlled qualities of grain. Huge steel bins are cheaper than huge concrete bins, “but the economics disappear” inside an elevator that has many medium-sized containers.
Still, the price of steel, at about half of concrete, means the grain industry construction business is always split between steel and concrete believers.
This winter, Sawby attended a grain elevator construction convention in Florida. He said he saw debate after debate break out among earnest attendees about steel versus concrete.
“One guy would sway you to his side, then the other guy would sway you back,” said Sawby. “It’s a never-ending fight.”
Dwight Benninga, an engineer from the Kansas manufacturing company that makes the grain pumps, said he thinks steel is becoming more popular as grain companies try to cut costs and back away from concrete.
“It’s tremendously expensive to build those on a cost per bushel basis,” said Benninga, who accompanied Sawby on his inspection tour.
“A lot of the new facilities in the U.S. that we see are steel.”
But Dietrich said he thinks the Louis Dreyfus and ConAgra decision to use steel facilities reflects a lower level of commitment to the prairie market than held by the companies using concrete.
“We think they’ve come in to test the market,” said Dietrich. Since steel facilities are a much lower investment, they are easier for companies to back away from if they decide to leave the market.
When a company builds in concrete, it signals it intends to be there for a long time, said Dietrich.
With most of these giant concrete and steel facilities now under construction, it will be years before there is a clear answer to which is the best investment – short-term steel or long-term concrete. But Sawby is delighted he has been able to play a role in one side of the debate.
“When I saw the Hutchinson Grain Pump loop system in the ’80s, I couldn’t believe how simple it was,” he said.
“I’ve had a dream that this would happen ever since,” said Sawby, gesturing at the Wilkie building site.