Revolutionary system Measuring grain in a hopper trailer depends on green lights instead of digital weigh scales
CORRECTION: This story originally contained the wrong phone number for Load Judge. The
correct phone number is 605-380-7585. We apologize for any inconvenience this may have caused.
BRANDON — Loading a trailer to the exact legal limit on the first try is an art. Drivers often go to the scale two, three or four times to hit the mark.
Correctly distributing the weight of the grain over the axles is the hardest part of the dance.
This trial and error process can add up to one lost trip per day when it lasts too long.
Read Also
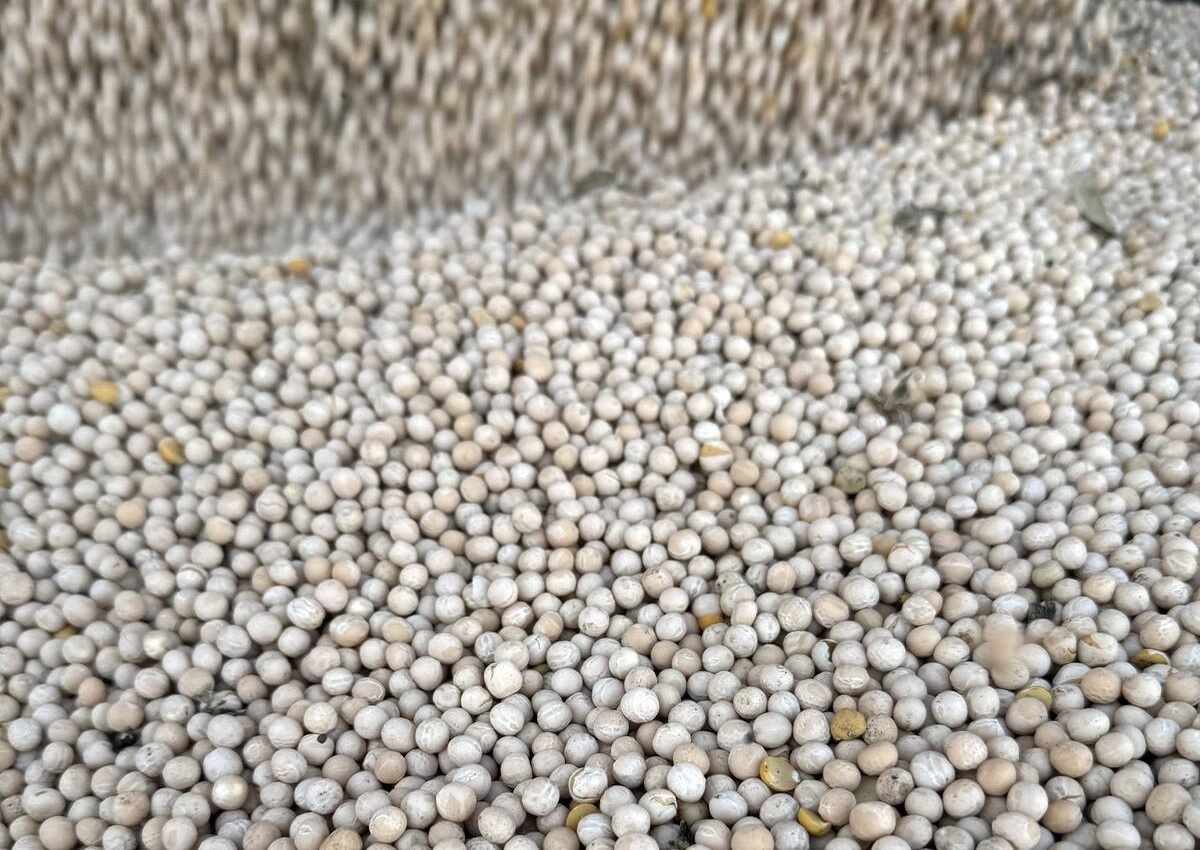
Yellow pea prices collapse on lack of demand
China’s tariffs and India’s accumulated stocks from previous imports have curbed those countries’ demand for Canada’s yellow peas just as harvest adds price pressure at the farm gate.
South Dakota grain farmer Shawn Gengerke thinks he has found a solution with his Load Judge hopper trailer sensor system, which he debuted at Manitoba Ag Days in January.
The system ensures that a driver can consistently load all axles to the maximum and not be affected by dust, dirt, mud, snow, ice, extreme heat, extreme cold, wind, bad night time visibility and driver fatigue.
Gengerke said the system also eliminates the need for drivers to climb up on the trailer, which is a significant safety factor.
“Commercial grain hauling is all about return on investment,” he said.
“You get paid per bushel, and there are only so many loads you can possibly deliver in any given day.”
Gengerke said truck drivers have more than enough to do juggling the vagaries of weather elements against the clock and the scale.
Climbing ladders does nothing but add to the stress and danger of trucking grain. The driver should focus his attention on proper load placement.
“Load placement in the trailer is critical,” he said.
“You lose money every mile you don’t have the correct allowable weight on each axle. Load Judge gives you accurate real-time proximities. You set your safe load limit on the first load. You come back and load grain in exactly the same place in the trailer on every subsequent trip time after time.”
Gengerke said his system removes the guesswork for drivers and elevator operators. It gets trucks back on the road sooner, which makes elevators more efficient.
“It’s a difficult job,” he said.
“You pull into an elevator, they open this great big chute and start dumping grain into your trailer. And you’re all just guessing, aren’t you? It typically takes two or three rounds to the scale to get the load even close to what you want, but that’s time you’re not being paid for. And burning diesel you’re not being paid for. It’s all very inefficient. And we know cameras don’t work because of the dust build-up.”
Gengerke said his system solves all those problems with three vertical light bars in each two-hopper trailer. One vertical light bar aligns with each hopper, with the third bar installed half-way between in the middle.
The light bars are mounted on the trailer wall on the driver’s side. There are no light receiving sensors on the opposite wall of the trailer.
The green lights in the vertical bars serve as their own transmitters and receivers, creating an image from the moment the first kernels start piling up in the hoppers.
As grain continues falling into the trailer, the algorithm Gengerke developed starts to take over and feed data, which is converted into a real-time image of the grain pile depicted on the driver’s screen.
“It reads the angles, pile heap and fall. That data travels through the power module box on the trailer. We use a wireless Wi-Fi to send the information to the driver sitting in the cab. He watches grain falling into the hopper trailers in real-time on his iPad, iPhone or Android platform two. And there’s a magnification button to blow it up on the screen for a closer look.
“The lights take one reading every time they flash on. They take another reading every time they flash off. They self-calibrate in one flash and send data to the driver with the next flash. The driver gets a real-time picture of the grain pile once every second.
“That’s the information he needs to decide whether to drive forward or backward to put the correct load on each axle. It really does become a very simple procedure for the driver.”
The system also includes one moisture sensor for each trailer unit. Gengerke said it is an important reading at harvest time because it tells the truck driver whether a load can go directly to the elevator if it’s dry enough or if it should go to the yard for drying.
“If we have moist grain, the truck driver knows it goes to a different bin,” he said.
“We might know about that on the combine, but the fact is that moisture sensors on combines are not very accurate. Our moisture sensors are accurate.
“Once you know which bins hold your wet grains, you use the moisture sensor in the Load Judge to blend off those wet bins for a load that’s under 15 percent. If you don’t have that information from the trailer, you might haul a load 100 or 150 miles and then find you lose $300 because your moisture content is too high. Load Judge makes sure that doesn’t happen.”
Gengerke said the information provided to the driver must be specific if the system is to create maximum benefits. The data is adjusted for different trailer brands and models and different commodities.
He said lower manpower cost is another factor in some trucking operations. Drivers accustomed to paying another person to help with loading can now do the job on their own.
A pile peak adjustment feature lets the driver account for differences in loading dry or moist commodities.
A bushel estimator feature uses existing bushel weight information to give the driver real-time bushel estimates while loading.
The basic Load Judge kit includes six sensors, one moisture sensor, a Wi-Fi box, quick attach plug, cables and necessary hardware. It is designed for a two-hopper trailer and sells for $6,500.
For more information, contact Gengerke at 605-380-7585 or visit www.loadjudge.com.