A new technology will soon be released into our market that will revolutionize how cattle in Canada are vaccinated.
Beef quality assurance, biosecurity, disease transmission and meat tenderness are all on the minds of consumers these days, and this new approach should dispel a number of consumer concerns.
It involves vaccinating with compressed air, carbon dioxide or nitrogen. The product is then delivered through a small orifice equivalent to one-seventh the size of an 18-gauge needle.
The system eliminates the problems one now encounters with broken, bent or burred needles, hide damage and the potential for infection from dirty needles.
Read Also
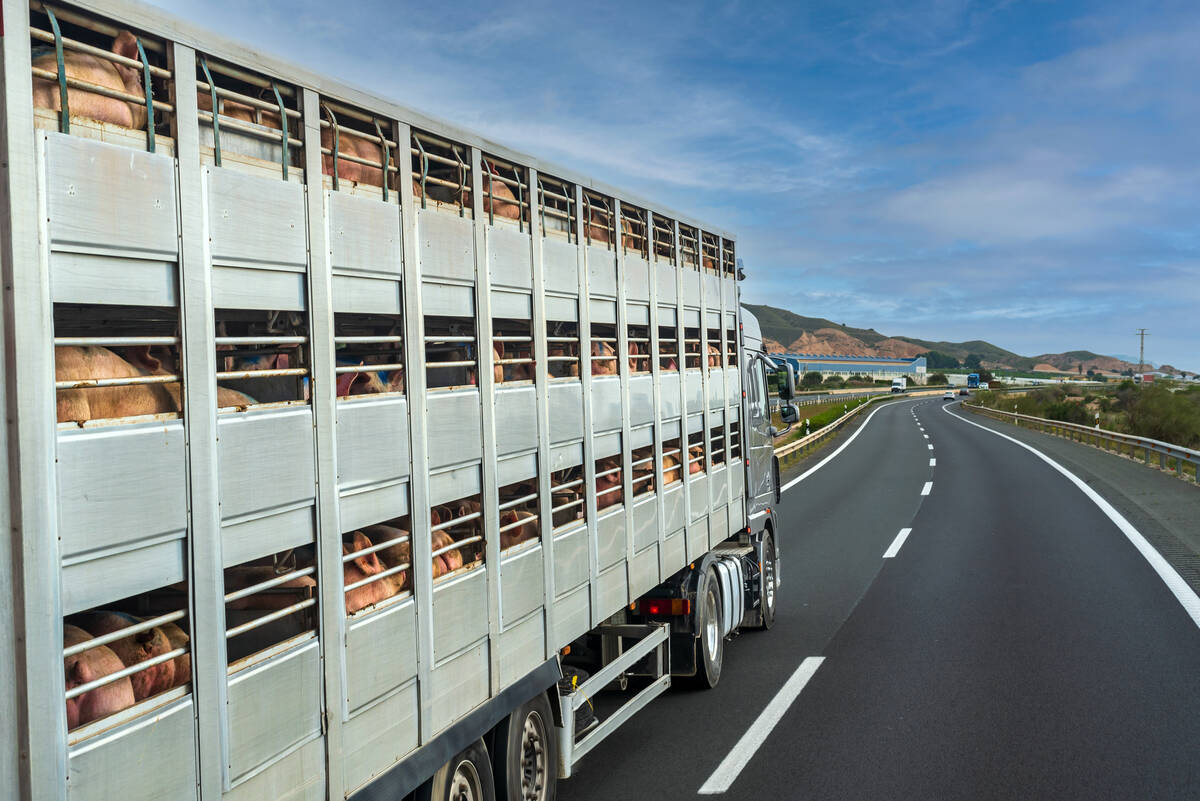
Hogs’ transport stress called costly
Poor trailer design and transportation stress are killing pigs and costing the pork industry millions of dollars in penalties, meat quality downgrades and failed welfare audits, according to research by a federal scientist.
In nature, animals are protected from natural exposure to disease such as direct contact or erogenous transmission. It is no wonder then that the next step in a more natural vaccination process would be needleless.
We are already seeing mass numbers of poultry vaccinated in chambers using an aerosolized vaccination process. Perhaps vaccination by that method or by way of oral vaccines in the feed are in the foreseeable future for cattle, but for now we should be happy with this needleless technology.
The technology also eliminates the issue of disease transmission through blood, such as can happen with diseases like bovine leukosis.
The beef industry now gives all intramuscular shots in the neck muscles, but reactions and scarring can occur along the needle track, which reduces meat tenderness and adds gristle that then must be trimmed out.
Buying the equipment that’s re-quired to move away from needles will have an initial cost, but the money saved by not having to buy needles will eventually pay for that investment. It will also eliminate disposal issues, which will ease environmental concerns.
The vaccination gun works by pressing against the hide. The gun discharges the set amount of vaccine when enough pressure is reached.
It can discharge in increments of 1/2 cc to 2 1/2 cc. For higher amounts, such as a four cc dosage, the gun is set on two and discharged twice.
There are also plans to develop larger guns that will handle up to five cc dosages and be able to eventually handle antibiotics as well.
The gun can administer product either intradermally (within the skin), subcutaneously or intramuscularly depending on how the pressure is set.
There is a permanent mount model and a portable backpack unit, which we hope will soon be able to be demonstrated to producers and feedlot processors.
This route of administration has been tested against the conventional route and response has been as good or better with the newer approach.
Intervet USA, which is marketing the new technology, has found that the new approach is efficacious. Although not statistically significant, there was a slight advantage to the new technology over administration with a needle.
The epidermis, or outer skin layer, is a mammal’s protective covering, so lots of cells are present to mount an immune response when exposed to a disease challenge. It makes more sense, then, to keep vaccinations near the surface or even in between the skin layers, like we do when we test an animal for tuberculosis.
This is a totally new method of administration, which means the current vaccines would have to be run through trials to prove their efficacy with the new technique.
The risk of accidental vaccination is much less with this method because pressure must be applied to discharge the product.
The cattle tolerate this application far better than a needle, although proper restraint speeds up the process with any route of administration.
Operator fatigue will be less because compressed air does most of the work. This is especially true these days, where high numbers of treatment crews are women and the automatic guns have really not been designed with them in mind. The automatic guns require a larger hand, but this is not an issue with compressed air.
The system must become more portable to use in the field and must be able to stand up in our inclement weather, but I envision the day when all vaccinations could be given this way.
It may also become mandatory, just as Canadian Cattle Identification Agency ear tags are now mandatory. This would be to the benefit of our entire industry.
Remember, no matter how good vaccination technology becomes, it is still not a replacement for poor management. Response to vaccinations will be greater if you are well managed with regards to nutrition and parasite control.