Lower combustion temperatures increases power and decreases nitrogen oxides creating healthier fuel efficiency
A miniscule mist of hydrogen and oxygen sprayed into the air intake of a diesel engine can burn cleaner and lower fuel consumption by 10 to 20 percent.
The unique HydraGEN technology is based on the fact that flame speed of hydrogen is nine times faster than the flame speed of diesel. Burning diesel in the presence of hydrogen creates faster and more complete combustion, resulting in higher peak pressure closer to top dead centre, commonly referred to as TDC. This higher pressure forces the enhanced diesel fuel to perform more work.
Read Also
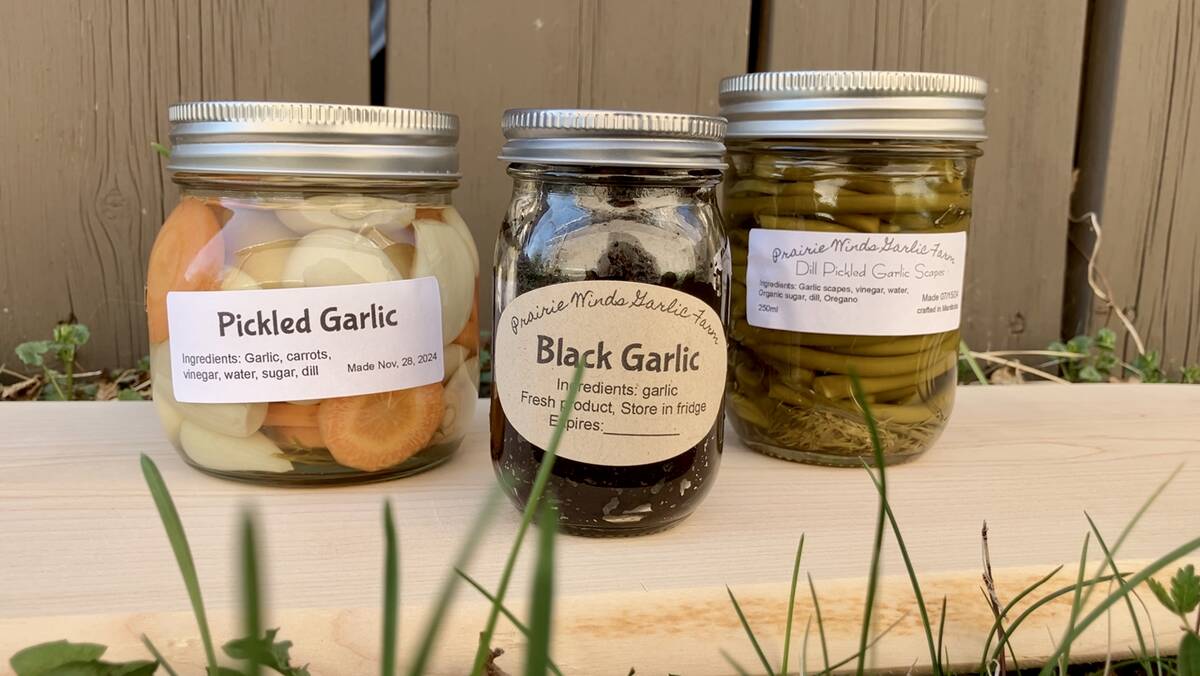
Growing garlic by the thousands in Manitoba
Grower holds a planting party day every fall as a crowd gathers to help put 28,000 plants, and sometimes more, into theground
The technology called HydraGEN was recently released by a new Canadian startup called dynaCERT, which has 200 units operating in marine, stationary genset and over the road applications in the Toronto area and Europe.
There are also a small number of test HydraGEN kits on ag sprayers and spreaders in Canada, said dynaCERT chief engineer Robert Maier in an interview.
Maier said the company needs farmers with new generation ag equipment capable of connecting to their satellite server to carry out trials. It would enable the company to track farmers’ fuel consumption and graph it.
“That always makes customers happy,” he said.
“We aren’t agricultural people, but we do know that a diesel engine is a diesel engine whether it’s in a highway tractor or a four-wheel drive ag tractor or out on a ship. Our technology is universal.”
Maier emphasizes HydraGEN is nothing like using hydrogen as a fuel. Rather, it’s using hydrogen and oxygen as catalysts to extract more work from a given volume of diesel. Maier’s system uses a trace amount of hydrogen to make the diesel combustion more complete.
“Instead of injecting hydrogen into the fuel, we mix a small amount of hydrogen into the air intake. It mixes with the air to form a homogeneous blend going into the combustion chamber.”
Maier said the addition of trace hydrogen does not raise the combustion chamber temperature. It lowers that temperature, which in turn lowers nitrous oxide emissions. It is produced by the reaction of nitrogen and oxygen gases during high temperature combustion. The higher the temperature, the more nitrous oxide escapes into the atmosphere.
“One of the secret nuances of pollution control on diesels — government decided citizens don’t like seeing soot going out the stack. But soot just falls back to the ground as carbon. They eliminated soot by raising the combustion temperature, thus creating more NOx which is the real environmental pollutant.”
Maier said the HydraGEN reactor is housed in a totally enclosed case. Every component is either plastic or stainless steel. It operates without pressure and it only functions when the engine is running. There are many kit sizes, each engineered to meet the needs of different displacements, from small cars up to 100 litres engines for gensets. Maier said they can build HydraGEN reactors for bigger engines if needed.
Regardless of size, each unit draws a small amount of either 12- or 24-volt power from the vehicle or 120 volt from a standard receptacle. This powers the electrolysis inside the HydraGEN case.
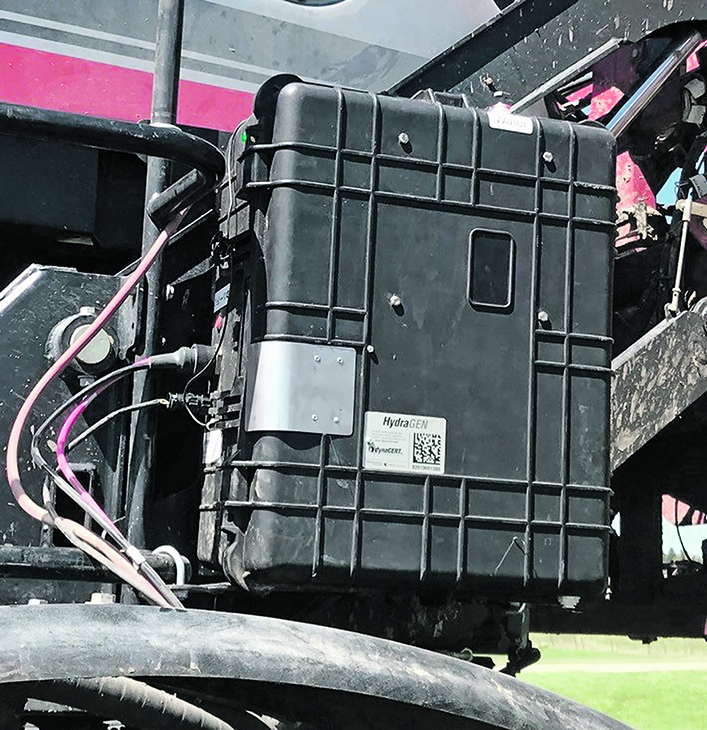
“The company started in 2004 with a pressurized device called the JetStar, a totally different concept from what we have today. It weighed about 300 pounds, whereas most of the reactors we have today weighs less than 50 pounds. It’s all contained in something that looks like a carry-on suitcase. Very easy to mount on any machine.
“There’s an internal catalyst. We use potassium hydroxide as our electrolyte to produce the H2 and O2 gas in the electrolyser. The electrolysis happens in a sealed non-pressurized reactor that uses electrolyte with distilled water and electricity to convert water into H2 and O2.
Readers with a sharp eye for chemistry will note that an extra molecule of oxygen mysteriously appears in the blend entering the engines air stream. There’s an explanation. The HydraGEN process requires two water molecules to capture that extra oxygen molecule. So, it’s expressed like this. 2-H2O + electrolysis = 2-H2 + O2.
“We consume a small amount of distilled water to obtain our hydrogen and oxygen. A typical two-litre fill will last 70 to 90 hours, depending on what the engine is used for. You’ll have to fill your diesel tank more often than the water tank.”
When gaseous hydrogen (H2-g) is burned in the presence of gaseous oxygen (O2-g) two new substances may form, one of which is liquid water (H2O-l) and the other is hydrogen peroxide (H2O2-l).
HydraGEN technology on test
Third party tests were conducted by the University of Ontario Institute of Technology, the PIT (Powered Industrial Truck) Group and Continental EMITEC. Here are the validated results.
- Up to 19.2 percent reduction in fuel consumption
- Up to 88.7 percent reduction in NOx emissions
- Up to 46.7 percent reduction in CO emissions
- Up to 9.6 percent reduction in CO2 emissions
- Up to 57.1 percent reduction in THC emissions
- Up to 55.3 percent reduction in particulate matter — no black smoke
- Increased engine power and torque
- Extended engine and oil life — lower maintenance costs
- Up to 60 percent reduction of diesel exhaust fluid use
- Reduction of diesel particulate filter replacement period by 33 percent
Maier said there’s an indicator light to tell the operator when he needs to add water. The operator buys a jug of distilled water and sticks one end of a hose into the bottle, the other end onto the filler valve, and presses a button. The HydraGEN device pumps in the correct volume of water and the operator back in business.
A typical installation on a 15-litre Cummins engine costs about $10,000, which includes installation and satellite monitoring. Highway truck payback is nine to 12 months.
“The heavier the load, the better our system seems to work. On one of the test trucks hauling water, they documented a 20 percent fuel saving.”