We ask manufacturers to put more and more gadgets into our implements and vehicles. We want voice recognition, hard drives to store client lists and our favourite music. The climate control has to have zones and work automatically. Remote start is a must, as is the built-in garage opener. The list goes on.
One thing all these “required” items have in common is they require electrical power. It would be easy to bang in a bigger battery and alternator to handle the load and increase the size and number of wires used to run these “necessities.”
Read Also
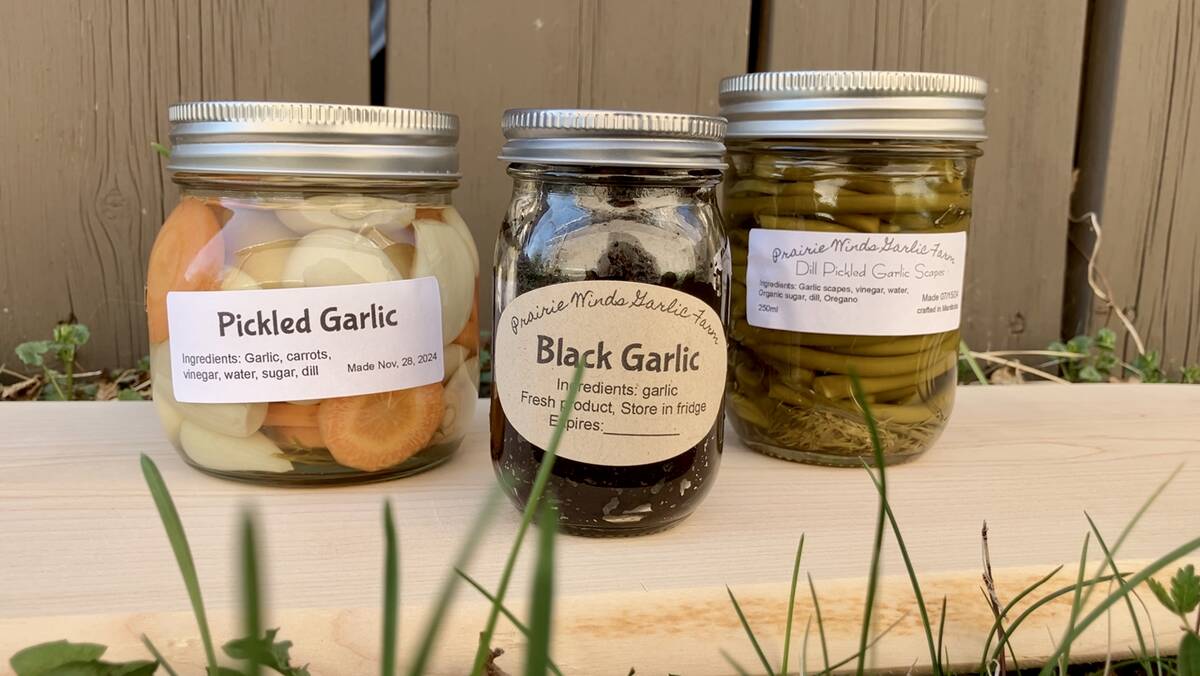
Growing garlic by the thousands in Manitoba
Grower holds a planting party day every fall as a crowd gathers to help put 28,000 plants, and sometimes more, into theground
However, copper is expensive and has weight. Every kilogram of added weight can reduce fuel economy by 0.01 to 0.1 litres per 100 kilometres. As well, how do you make them all fit into the available space?
Consider the direct costs of engineering, building and fitting a new wiring harness, along with the penalties in real dollars of lower fuel economy, and then consider the possibility of lost sales to competitors.
The solution was to have you drive a computer.
Your new truck or car may be a bit bigger than your laptop, but it performs the same way. Except for the steering and brake pedal, everything else in the instrument cluster, the engine and transmission are computer activated. The brake and steering are likely computer assisted in some manner.
Multiplex wiring along with computer-like controls are the answer for now.
Multiplex in this instance means getting a wire to do more than one job. As well, wire voltages will vary. Higher voltage can actually mean a lighter duty wire and therefore less weight. The end product is a wiring system in your car that is no larger than in the past and can do seven or eight times the amount of work.
In computer terms, the system uses “buses” as a way to package information. When you activate a “key,” which can be a lever, point on a touch screen or sensor, the computer loads the bus with information received from the “key.” You turned the left signal light so that’s the information the bus takes to the left signal lights. It gives this signal to the circuit board, which is like a receiving computer, and the signal light blinks. When you shut it off or step on the brake, other busses are loaded and sent down the same wire with the necessary information.
A simple task you say. To a computer it is.
However, programming the computer isn’t. When your tail light doesn’t work, putting in a new bulb may not fix the problem. If the problem is in the tail light circuit board, you may have to replace the entire tail light assembly. Or, you may have to go to the dealer to see if the programming is still sending the right bus to the right place.
One unexpected benefit of increased electrical power consumption and better fuel economy is that your alternator no longer charges all the time. The need for fuel economy is so great that under numerous driving conditions, the computer shuts the generating part off. That means you run off your battery for part of your drive. If it wasn’t fully charged to start with, it’s conceivable that your new car could shut down because the battery runs out of juice. The cost of reprogramming is so great that it’s cheaper for the company to install new batteries.
As for that defective tail light, the cost of the assembly was slightly more than $300. An electronics tech friend fixed it for about $75. He is now on retainer — a bottle of good scotch at Christmas.
Charles Renny is a Canadian professional automotive reviewer.