Cover crops can build soil structure, which is considered a defence against compaction, but they are not always feasible
Increasing soil organic matter is one of the best ways to prevent soil compaction, said Marla Riekman, soil management specialist with Manitoba Agriculture.
“Building soil structure is your best defence against soil compaction,” Riekman said.
“It’s (organic matter) creating both food and homes for microbiology that’s helping to build soil structure as well. It’s helping to build that spongy soil structure that helps to carry loads.”
Cover crops can build soil structure and remove water from soils through transpiration much faster than using tillage to promote evaporation, but growing cover crops isn’t always feasible in a short Canadian growing season, she said.
Read Also
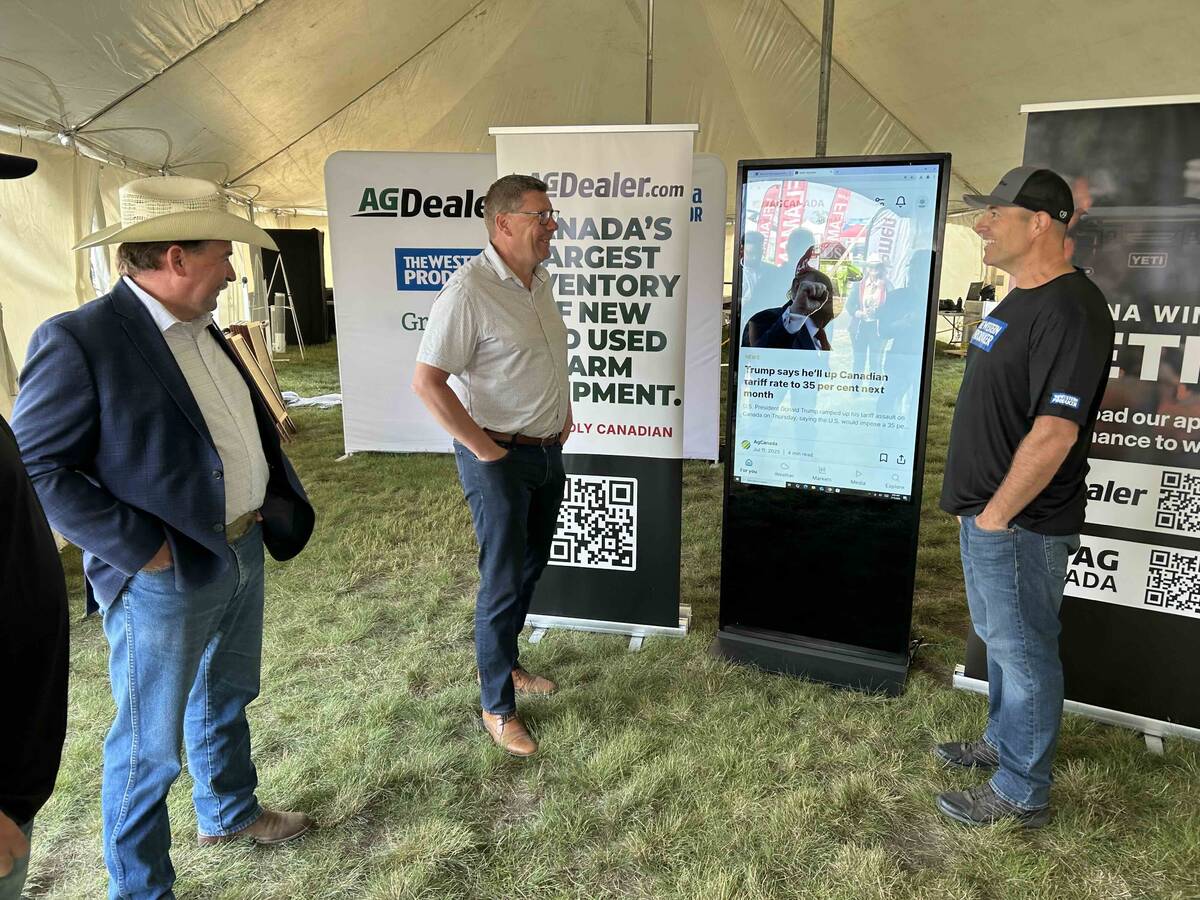
Moe and Harrison tour Ag In Motion site
Ag in Motion 2025’s more than 560 exhibitors haven’t let the smoke blanketing the province dampen their enthusiasm as the Langham farm show got under way on Tuesday morning.
Using perennials such as alfalfa in rotations can also build soil structure and prevent soil compaction because the roots can reach deep into the soil and use a lot of water, and once the crop is established, tillage isn’t required to harvest crops.
However, even alfalfa fields can incur compaction issues if equipment travel on the field during wet conditions.
Also, if there are already significant compaction issues on the field, even alfalfa roots will not be able to penetrate compressed soil layers to find nutrients and water.
The greatest risk of a field operation causing compaction occurs when the moisture level is near field capacity.
“When the soil is dry enough to till, that is when it actually has some strength to it to resist compaction.”
However, when the soil is very saturated and equipment causes deep ruts, compaction is likely not happening deep in the ground, Riekman said.
Riekman said managing water is important because producers need to minimize the need to perform field operations in wet conditions, when compaction is most likely.
She said the hardest category of compaction to address is deep compaction, which can be a metre or more deep.
“The reason no one wants to talk about this is because this is when we start to talk about grain carts,” Riekman said.
“This is the stuff we want to be more concerned about because sure we can till a little deeper and break out some of this surface compaction if you’re going to use tillage in order to fix this problem, but the further it goes down into the soil the more impact we’re putting deeper into the soil. This is the level of stuff we can’t fix as easily.”
When possible producers should spread out the weight of their equipment to as many axles as possible, which Riekman said producers should keep in mind when they upgrade their grain carts.
Shallow compaction is another type of compaction that happens 15 to 20 centimetres under wheel tracks.
It’s important to consider that 80 percent of the compaction occurs in the first pass, Riekman said, and the next three passes will only cause an extra 20 percent compaction in any given spot.
“I like the concept of control traffic farming (CTF), but it’s a difficult thing to do,” Riekman said.
“But you can stick to a more deliberate pass, so not going to a full CTF, but not allowing the grain cart operator to just drive across the field. Instead, have a plan of where we’re going to have grain carts running, and sticking to that.”
She said keeping tires inflated to the right pressure is critical to manage shallow soil compaction, and that tracks aren’t necessarily better then tires at reducing soil compaction.
“Tracks have less slippage, but if your duals are at the right pressure they are about the same when it comes to actual compaction issues,” Riekman said.
When a tractor is parked on concrete you shouldn’t be able to stick your finger under the edge of the tread.
“If you can stick your finger under the edge of that tread, probably you’re over inflated, the tire is too round, that tread is supposed to be flat to the ground,” she said.
Another kind of soil compaction is a hardpan that is typically a three to five cm thick layer of soil just below the depth of tillage, which builds up after years of plowing at the same depth.
“Equipment is causing that pressure down below, and it’s smearing the soil down below so you get that hardpan buildup,” Riekman said.
“You’re disconnecting all of the roots, any of the biopores, root pores that are there so it’s not connected to the soil surface and sometimes that can actually affect how water is going through the soil.”
She has observed fields in Manitoba where consistent use of vertical tillage equipment caused a hard pan five cm deep.
“I don’t have a problem if they (vertical tillage equipment) are primarily used for residue management. I do have a problem if they’re primarily used for soil management because they’re not actually good soil managers,” Riekman said.
“Those high speed disks are designed to pulverize soil, and that is going to mess up soil structure, and that’s not going to help you when you are trying to build it to help you through these situations.”
She said if growers are using tillage they should rotate their tillage depths to reduce the chance of causing a hardpan layer.
Hardpan layers can persist for years after a farm has transitioned to no-till production.
“When you have a long-term buildup of compaction, like a hardpan, it’s not going away overnight,” Riekman said.
“I’ve seen 30, 35 years (of fields under zero-tillage management) in Manitoba that are still hardpan, on nice clay loam soils.”
To find a hardpan take a shovel and start digging to see if the roots are growing horizontally because they are unable to penetrate a compacted layer.
“I want to dig up that root and I want to look at it because that root is actually going to tell me a lot of what’s going on in the soil. I can also see what the structures look like, I can feel where these tight areas are as I’m digging a hole,” Riekman said.
Before growers use tillage to address soil compaction, they need to find out exactly where the compaction layers are in their fields.
“First determine the depth of compaction and then only run right under it,” Riekman said.
She said a study on heavy clay in the Red River Valley used subsoiling to reduce compaction, and the researchers tested how much the soil compacted in subsequent years.
“By year two and year three the soils recompacted itself, with travel over the field, or whatever’s happening on the field,” Riekman said.
“Subsoiling would have to be done on a rotational basis because the soil is going to recompact itself.”
A separate study was conducted in Iowa where researchers used a subsoiler on half of a field and left the other half alone, and then monitored the fuel use to get a cost of subsoiling on a per acre basis.
“They took yield for the next couple of years to see if they got enough of a yield bump to pay for the extra cost of subsoiling. What they found is they had a 50-50 chance of paying for it,” Riekman said.
“What they said in the end is focus on the headlands or the areas that you know are really tight. It’s an expensive proposition, going and subsoiling, let’s just stick to the areas that really need it.”
She said if you are going to subsoil, don’t do it when it’s wet because you can potentially cause more problems, including smearing on the sides of the shank gouges in the soil.
“They say your soil needs to be dry enough to crack and shatter. So they say it’s best at terminal wilting points. This should be after harvest when the crop has pulled everything out, in a drier fall,” Riekman said.
Over time, soils can churn themselves over through wetting and drying cycles, which creates cracks in the soil that plant roots can get in and open up even further.
“This is Mother Nature subsoiling the soil for you,” Riekman said.
“We have a lot of these soils that have this shrink-swell capability with the clay content in the soils. When you’ve got that clay, it cracks open, and some of these cracks can be five feet (1.5 metres) deep.”