Picture this scene: a super-B signs in at the elevator with a load of peas, the driver proceeds to dump as instructed, and 1,000 bushels of peas end up in a 50,000 bu. designated soybean bin.
That’s a bad mistake, and a costly one at that, enough to make some people shudder.
However, it’s a mistake that occurs every day at an elevator someplace in North America, says GSI grain identification specialist Roger Price.
“The typical scenario is the truck comes in and gets mis-identified so it’s set on the wrong bin,” said Price, adding that the mistake usually happens at the time the grain is initially received, before it even gets into the system.
Read Also
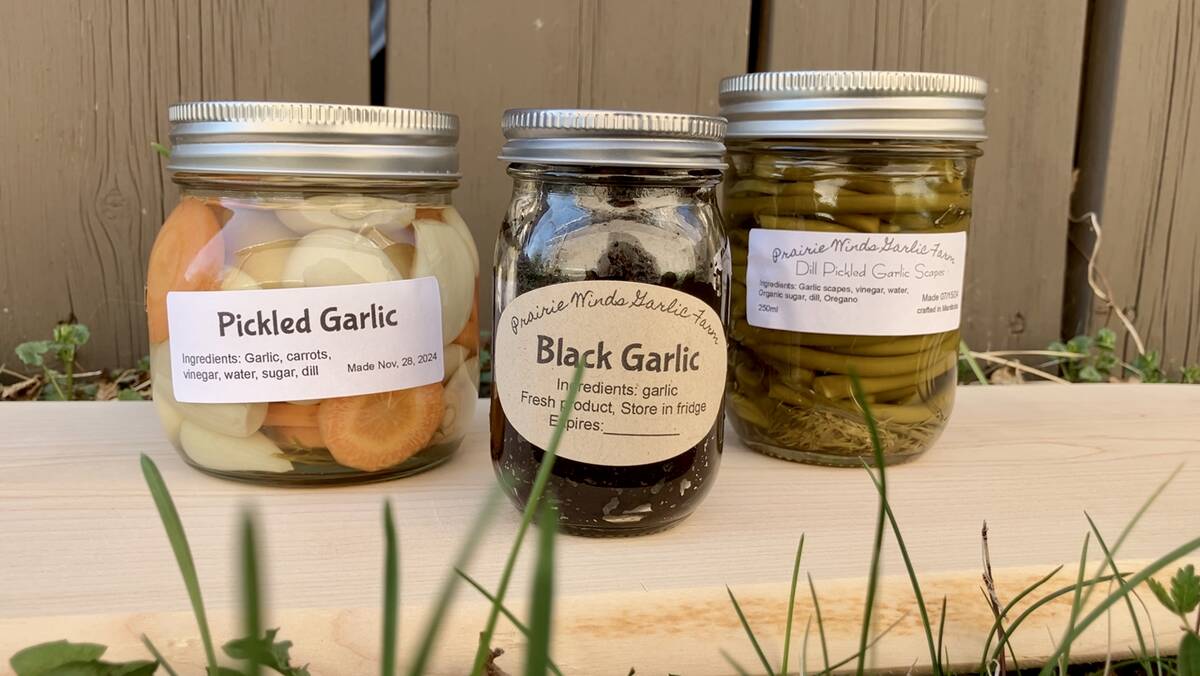
Growing garlic by the thousands in Manitoba
Grower holds a planting party day every fall as a crowd gathers to help put 28,000 plants, and sometimes more, into theground
However, if the elevator operator doesn’t know the commodity is about to be dumped into the wrong bin, there’s no reason for him to call a halt.
He said a farmer sometimes receives a radio frequency identification (RFID) tag that’s been incorrectly coded, and the entire truckload will go in the wrong bin, which no one will know about until later.
“Sometimes operators don’t even know what’s happened until later when they go to load a rail car and they see they have corn mixed with soybeans,” he said.
“Now it gets to be a really expensive situation. And how much has already gone into the rail car? I’ve seen that numerous times. It happens a lot. Plus, it ties up that bin because you don’t want to put more grain in there until you’ve emptied it to get the problem sorted out.
“You won’t make any profit after a mistake like that. Generally, if you’ve delivered soybeans to a corn bin, that’s a $10,000 mistake.”
None of the options for that bin are cause for celebration.
Sometimes the entire bin will be run through a cleaner to separate the two grains.
If it’s a mix of barley and peas or wheat and corn, it might be sold for livestock feed.
The most popular option is to hold on to that bin and gradually blend it off as foreign material or dockage into future shipments. That ties up a bin, but at least it saves the expense of cleaning it.
“Depending on what the grains are, they usually blend it off,” Price said.
“If you’ve dumped a load of soybeans into a corn bin, you’d probably try to blend it off as corn, but you might try to run some of it into a bean bin because beans have a higher value than corn.
“Bottom line is, it’s a mess. I’ve seen guys go up top a big bin with a vacuvator trying to clean it up. I’ve seen guys up there with five-gallon buckets up in the bin handing the buckets out to another guy up there.
“That is absolutely a safety factor. You hear about grain engulfments all the time. Going into these big bins these days just isn’t smart. You should stay out of those bins. If there’s been a mistake made and people are trying to get it cleared up quickly, that’s precisely when you’re in no state of mind to climb up a bin.”
Price said the key is to stop the mistake before it happens. Although RFID is used at many facilities to direct deliveries and prevent grain mixing, the problem can still occur because of operator error or a mechanical glitch.
He says GSI has just introduced a new high-tech grain identification system that uses sensor cameras that illuminate grain with multi-spectral light to analyze hundreds of images per second.
The system, called BinRite, can be integrated into existing programmable logic controller protocols or have a stand-alone PLC. If the identified crop type is being misrouted, the fully automated system will stop the grain flow and sound an alert.
BinRite will be available for installation mid-summer at Canadian elevators. Initially it will identify corn, soybeans, white wheat and red wheat. Other grains will be added later.
“BinRite automatically takes output from the sensor and co-ordinates it with (an) existing automated control system. It can be set up to shut the gate off or shut a belt off. Set it up any way you want it,” Price said.
“You can install the cameras anywhere you think there’s a need to monitor what’s flowing through your elevator system. Some elevators have them on every shipping leg, just to make sure they’re loading the correct commodity. In fact, you could install a camera on every single spout to potentially eliminate all mistakes.
“BinRite will help elevator operators avoid the problems that result from mixed grain, including shrink, broken space, shipping delays, shipment rejections, steep discounts and strained buyer relationships.”
BinRite sells for US$8,000 for the camera, wiring and integration into an existing control network.