Burning dirty fuel in a turbine destroys the equipment but one company hopes to solve the problem with new technology
Many farmers in oil and gas country navigate by the gas flares.
These flares are a double edged sword. They mean jobs and additional income from access or rights, but they are bad for the environment and a waste of energy.
The options are to close the wells or convert all that gas into electricity on-site.
Governments around the globe are doing just that by forcing petroleum companies to address flaring.
The reason for turning wellhead gas into electrical energy is simple. It’s easier to move energy to the destination through wires than through pipelines.
Read Also
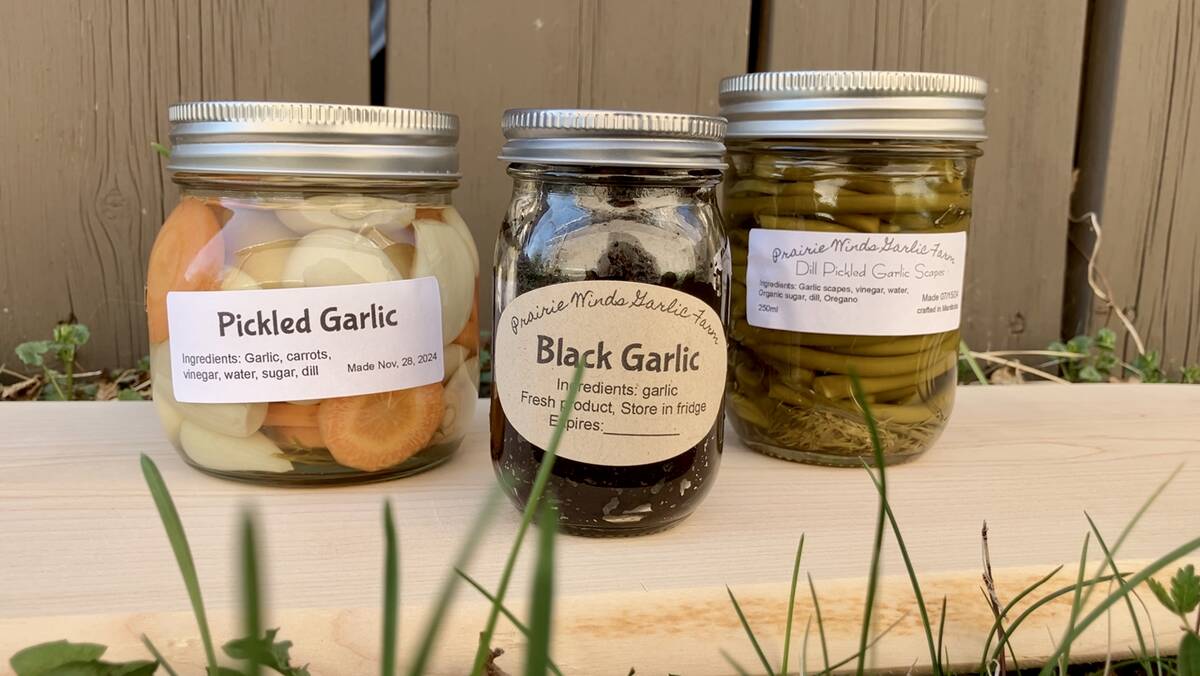
Growing garlic by the thousands in Manitoba
Grower holds a planting party day every fall as a crowd gathers to help put 28,000 plants, and sometimes more, into theground
However, burning dirty wellhead gas in a turbine is a good way to destroy millions of dollars worth of delicate equipment, according to retired industrial electrician Pat Barry, a veteran of the northern Alberta oil fields.
“A gas turbine normally should last 10 years. At this one particular site we serviced north of Grande Prairie, their dirty fuel would destroy a turbine in about a year,” Barry said.
It was good for his business, but not so good for the company that owned the well, he added.
“They were using the same turbine that’s installed on the C-130 Hercules. It’s about 5,000 horsepower, and it absolutely must have clean fuel. Bad fuel takes the blades right off. That’s a $3 million repair bill. They had a big scrubber unit on site, but it just wasn’t doing the job. We sold them a lot of turbines.”
The economics of turning wellhead gas into electricity goes up in smoke if you’re continually replacing expensive turbines. Most of the dirty, low-grade gas coming off the wellhead is methane, although every well has a different mix of gases and chemical components. Within any given well, the mix can change from hour to hour. Real time tuning of the device to produce optimal power without frying the blades is a complex challenge.
This situation has fostered dozens of startup companies dedicated to solving the problem. One of those firms is LPP Combustion located in Maryland.
Alberta native Michael Klassen is co-inventor of the proprietary LPP technology and one of the company’s founders.
“What we always see coming off the wellhead is a random mix of liquids and gases,” Klassen said.
“We take that whole mix and run it through a device we call a fuel conditioner. This is not a scrubber. The fuel conditioner is totally different technology than scrubbing.”
Klassen said the wellhead stream is typically a blend of methane, ethane and propane along with heavier components, each with its own chemical properties and burn characteristics. The challenge for LPP is to turn the liquids and gasses into a fuel that can safely spin turbines.
He said the LPP fuel conditioner is basically a vaporizer, which creates a homogenous fuel that yields a controlled, uniform flame. To help accomplish that, the LPP fuel conditioner injects inert gases to manage the heating value of that stream.
Klassen said the fuel conditioner creates what he calls a substitute natural gas. LPP takes the higher hydrocarbons — the C2, the C3 and C4 gases —and changes them so they match the heating value of natural gas. The ratio of injected inert gases to wellhead gases determines how closely he can mimic a high-quality clean natural gas. If it isn’t, the result can be that $3 million repair bill.
“When our substitute natural gas gets into the turbine, the turbine sees that the substitute has the same energy content as a natural gas stream. The turbine doesn’t see any difference between what we’re putting in and what true natural gas would be,” he said.
“Depending on the composition of the fuel coming into our fuel conditioner device, we can vary the condition so it matches the condition of any natural gas. And we do that on the fly. When the incoming composition changes, we instantly change the way we condition it so it continues to match the characteristics of natural gas the turbine is looking for.
“We’re not doing anything to change the carbon structure of any of the components. We’re only changing the heating value and putting it into a vapour phase the gas turbine is accustomed to seeing with natural gas.”
This all happens automatically and instantly through the use of sensors and the controller.
The LPP fuel conditioner requires a certain amount of electrical energy in order to vapourize the wellhead stream. To meet that need, Klassen said they simply tap into a small percentage of the electrical power produced by the turbine.
He said the apparatus and procedures to turn liquid into vapour meet all the same safety criteria of the gas industry.
Klassen said LPP Combustion is only 10 years old, and it’s taken that long to develop and test the technology. Its first commercial-scale fuel conditioner is going into service in Nova Scotia this winter. It has a number of portable conditioners on trailers that it has been using in fracking fields around North America to conduct tests.
“We can take the composition of gases currently being flared and turn it directly into electrical power,” he said. “We don’t need to strip it or scrub it. We just vaporize it and shoot it into the turbine.
“Flared gas is a tremendous waste of energy and money, plus it’s a danger to our environment. We can make a dent in that.”