FARGO, N.D. — Closing the seed trench in a muddy field is a problem some manufacturers have solved, but at the expense of compacting the soil, thus inhibiting emergence.
Daniel Wipf says he and his father have figured out the solution, in the form of a notched closing wheel they have dubbed Pro-Stitch, featuring big teeth interspersed with small teeth.
“We were having trouble getting our seed slot to close up in wet conditions,” Wipf said.
It’s a common problem when there’s too much moisture during seeding, he added.
Read Also
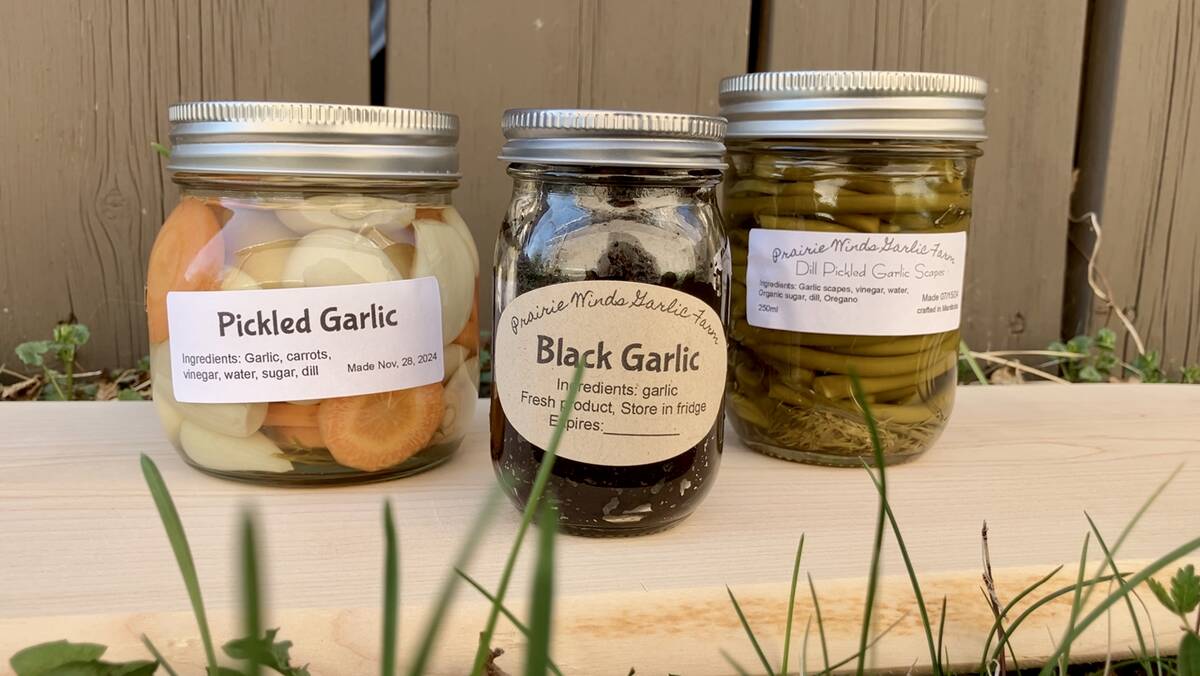
Growing garlic by the thousands in Manitoba
Grower holds a planting party day every fall as a crowd gathers to help put 28,000 plants, and sometimes more, into theground
The Wipfs manage a 10,000 acre farming operation at Lake Andes in south-central South Dakota, using planters and air drills to put in their various crops.
Like other areas of the prairies, they have experienced above average rainfall in the past two decades.
“We tried lots of the different closing wheels and different setups, but nothing worked the way we wanted,” he said.
“So my dad came up with this closing wheel as a better solution. It gets the seed trough closed without causing sidewall compaction.”
Pro-Stitch closers for corn planters come in pairs and sell for US$205 per row. Pro-Stitch closers for no-till air drills are single wheels and sell for $105 per row.
Both types are simple to install by replacing the original equipment manufacturers closing wheels. Most of their work has been with planters.
“For a planter, we install one closing wheel in the front hole and one in the rear hole, about 10 inches behind the coulter, and offset,” Wipf said. “The teeth interlock with each other all the time. Soil pressure causes a tooth from a front wheel to lock automatically into a notch on a rear wheel. That takes care of itself.
“The wheels are set to be about two inches apart at the bottom, so they firmly push the soil against the seed and stitch up the seam. That’s why it’s called Pro-Stitch. We always tell people to run it at the lowest possible down force so the seed can emerge when it’s ready.
“The small tooth at the bottom of each notch is called an ejector tooth because it kicks out any roots or stalks that get caught between the two wheels.”
Wipf said all steps in the manufacturing process are carried out in the family’s own factory, including the UHMW wheels.
Some of the one-piece wheels are cut with a CNC cutter from blank UHMW sheets. Others are moulded using a 400F compression moulding process. All flanges and fittings are stainless steel and all bearings are OEM, so finding replacements is easy.
For planters, the wheels are available for JD, Case, Kinze and White. For air drills, the wheels are available for JD and Case.
“We have customers who’ve had really good success planting wheat through a planter using our Pro-Stitch closing wheels,” Wipf said.