Airflow blown outward from within rotor creates high separation at low r.p.m. with less kernel damage
Kernel damage is the price farmers pay for increasing rotor speeds to improve grain separation.
However, there is a fix, and it’s in the air.
Sunnybrook Welding’s new Axial Air Integrated Rotor (AAIR) uses an axial fan to push air into a centrifugal fan, which pumps a massive volume of air into a modified rotor.
Shooting this airflow outward through the crop mat creates better separation at slower rotor speeds. Lower rotor r.p.m. means less kernel damage while putting more seeds into the tank.
Read Also
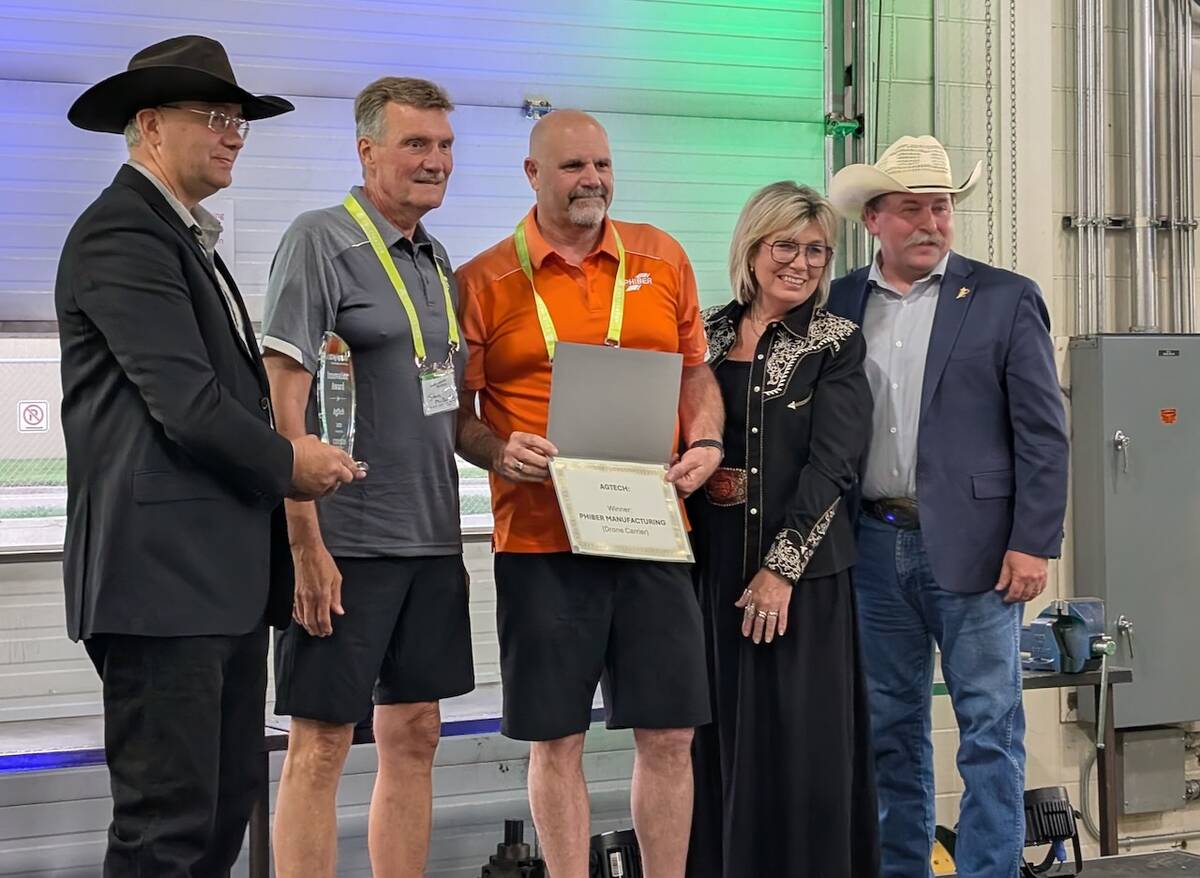
Ag in Motion innovation awards showcase top 2025 ag technology
The 2025 Ag in Motion Innovation Awards celebrated winners across five categories: agronomics, agtech, business solutions, environmental sustainability and equipment.
Until now, combine engineers have depended on impact, centrifugal force and gravity as the three main factors in the threshing and separating process. They have not considered air as a viable force, says Gerald Foster of Sunnybrook.
This historically narrow view of how to separate grain from material other than grain is now being challenged by Foster and his engineering team, widely recognized as innovators in leading edge technology for North American combines.
“Nobody has tried a pneumatic positive displacement system using air to separate seed from straw,” Foster said.
Pressurizing the inside of the rotor and injecting air radially outward through the underside of the crop might prove to have significant benefits, he added.
Fans have traditionally been used to clean chaff from grain on the shoe; they have not served as part of the separation process. Foster said his patent lawyer was surprised when his research discovered almost no evidence of combine engineers using air in separation and threshing.
Sunnybrook is starting off with a Gleaner S series combine for prototype test purposes. Its design simplicity and modification gives researchers easy access to the sideways rotor, but the Gleaner is already a high performance machine because of its 360 degree rotor. As such, it may not prove the full potential of AAIR.
However, Foster said they had to start somewhere. Sunnybrook manufactured all Gleaner rotors from 2002-12, so its experience with the S series made it an easy pick for the prototype.
“We don’t want to look specifically at any one brand of rotary combine because this pneumatic concept is universal,” he said.
“It applies to any rotary type combine.”
The company plans to eventually test the concept on all rotary machines, he added.
Foster said the company’s engineers had no problem envisioning airflow as a major force in the separating/threshing process when developing the system.
The challenge was figuring out how to put pressurized air into the rotor and then make it shoot outward to fluff the underside of the mat uniformly along the entire length of the rotor.
They thought about sending airflow through the centre of the shaft, but that involved switching from the current two-inch diameter shaft to a heftier four-inch shaft to make room for an air passage down the center. It would also require a 20 horsepower compressor, with power robbed from the combine or generated by an independent auxiliary engine.
The team determined that a two-stage compression system with fans could create the necessary volume of moving air, considering that volume is more important than actual pressure. Because the rotor is spinning anyway, why not simply mount the two fans to the stub shaft at the non-driven end of the rotor?
Gleaner uses a solid stop sign-shaped steel plate to hold the bearing at the rotor end wall. The plate bolts to the cage frame and the side wall of the combine. Foster said his design keeps the plate in its original position, but it will be modified so that it’s 75 percent open to let air push from the axial to the centrifugal fan.
To regulate the volume of air entering the AAIR, the operator adjusts a second steel disc to cover or uncover the opening. As the rotor and fans turn faster, more air whistles through the plate. Minor adjustments in the cover disc control the exact air volume entering the rotor and subsequently blowing out into the crop mat.
The rotor end wall spool is cut out and moved 10 inches inward from its original position, and a new extended end shaft is installed. The recessed spool accommodates the blue blade axial fan and three curved steel centrifugal fan vanes welded to the end wall.
The 10-blade axial fan has adjustable vanes, but the blades will be locked in position once the best pitch has been determined.
“It’s a benefit to have adjustable pitch on the axial fans so we can tune the system, but there’s no need to ever change the pitch once we lock them down,” he said.
“We’re buying high end axial fans, and the only way they come is with adjustable blades. We’re installing them on a shaft that accelerates from zero to 1,000 r.p.m. in just two r.p.m., powered by 250 h.p. Cheaper fans just won’t take that. We make the steel vane centrifugal fans ourselves.”
Funnelling all this fresh pressurized air from the dual fans into the underside of the crop was a bigger challenge. The three curved centrifugal blades each force air into a raised hollow steel channel welded to the rotor surface.
The three channels run the full length of the rotor and are capped to hold air pressure at the far end, near the drive box.
The top surface of each channel has six air release louvers with the opening measuring three inches long and a half inch wide. Foster said the characteristics of pressurized air dictate that some sort of slider valves are needed on each individual louver so they can be tuned independently.
The airflow within the channels pulled about a half inch of water at 200 r.p.m. in lab tests, meaning it was far from being a raging storm. However, the flow was also not uniform.
“That’s where the headaches start,” he said. “The first louver measured wind at 9.5 m.p.h., but the second hole was sucking air into the channel instead of pushing air out. Well, that’s not what we wanted.
“It seems that an Italian guy by the name of Venturi got involved. The air within the channel was moving so fast that when it whizzed underneath that second orifice, the Venturi effect pulled air into the channel. The fix was simple. We just put in longer bolts for the slider valves and that was enough to break up the full speed air flow. Those are the surprises you never anticipate in these projects.”
Rotor balance is not a problem because each channel weighs exactly the same, and they are evenly spaced around the rotor at 120 degree intervals. As well, the rotors are balanced after all work is completed.
Foster said it wouldn’t be a problem to install six channels if that became necessary.
Foster said the first step is to show that positive air displacement can be a benefit in the processor of a combine.
“Combines are about maxed out in terms of physical size,” he said.
“Class eight and nine axial flow machines are burning 20 to 25 gallons per hour of diesel. The real work going forward will be using air more effectively in displacing grain versus MOG (material other than grain).
“Some crops will likely be better candidates than others. Fine seed crops like canola may be very responsive; larger seed maybe less so. Our hopes are that we can reduce friction, conserve power and process more material.”
For more information, contact Foster at 780-789-3855.