The new Jaylor D series dump wagon features a number of innovations based on conventional European design merged with fresh Canadian technology, all aimed at reducing turn around times.
When you’re pulling 85,000 pounds of trailer down a public road, safety has to be your overriding concern, says Jaylor engineer Trevor Sutcliffe. He says safety dominated the design discussions for the D series dump wagon.
Those discussions date back almost 15 years when he emigrated from England, where he also designed wagons for agriculture.
“We’ve incorporated the conventional design you commonly see in European carts with some fresh Canadian thinking,” says Sutcliffe.
Read Also
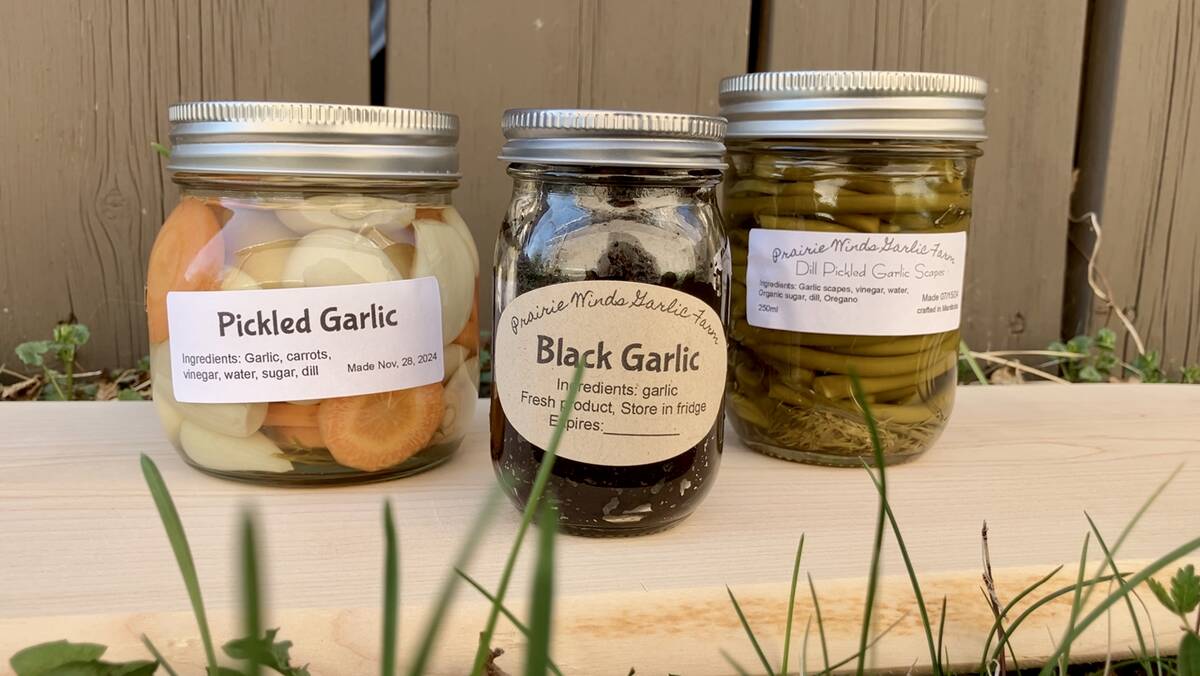
Growing garlic by the thousands in Manitoba
Grower holds a planting party day every fall as a crowd gathers to help put 28,000 plants, and sometimes more, into theground
He says that the only real European component is the basic idea of using a tractor with big brakes to pull a cart with big brakes that dumps out the back. That concept, along with the necessary big-brake tractor technology, began making the Atlantic jump about 25 years ago.
“Jaylor is using a number of totally new ideas that nobody else has tried yet in dump wagons. One of these is the double acting dump cylinder. Almost everyone in the business uses a multi-stage single-acting cylinder. The cylinder raises the box and then the weight of the box pushes the cylinder back down again. But it requires a lot of oil,” says Sutcliffe.
“We use a double-acting cylinder like you’d find on an excavator or payloader. The oil is circulated continuously rather than used in one direction then dumped into a reservoir.”
He says this speeds up cycle time because the double-acting cylinder pulls the box down quicker than gravity.
“That’s an economic benefit. The other benefit is a very low oil requirement. A tractor needs to move 83 litres of hydraulic oil to raise the box. But the double acting cylinder is full of oil from the start, so less than 15 litres are pumped from the tractor reservoir to raise the box.”
Sutcliffe says this eliminates the cost and complication of an auxiliary oil reservoir. Conventional multi-stage single-acting cylinders can use so much oil they run the risk of draining the tractor, causing serious damage.
“For example, (some conventional units were) particularly bad for having an oil transfer problem. If you used too much oil, it would set off alarms that actually shut down the engine and even turn off the computer.
“A lot of farmers have no choice but to use their 250 horsepower tractor just to pull a wagon. They don’t really need that much power, they just need the oil capacity you get with that big of a tractor. With our wagons, we use a 150 h.p. tractor to pull the same load because we have such a low oil requirement. That’s another big money saver.”
Sutcliffe says most people assume that working the oil so hard creates cooling problems. But surprisingly, the opposite is the case.
“It’s really kind of crazy the way it’s worked out for us. If you drain your tractors oil with an implement and then pump it all back in again, you know you get a lot of foaming. The oil gets stirred up and agitated.
“But when you’re just circulating oil in a closed system, the oil level stays consistent. We don’t get anywhere near the amount of foaming or agitation. And cooling has not been an issue.”
The new D wagons are built with cambered highway axles. On wagons with conventional solid axles or walking beam suspensions, the inner edge of the tire surface always wears quickly while the outer side still has plenty of tread. The inside bead carries 80 percent of the weight as the wagon is pulled down the road straddling the crown.
Jaylors solution was to build their suspension with positive camber so tires on both sides of the wagon run flat on the road surface. The tops of the wheels are farther apart than the bottoms.
“We put a fairly aggressive camber on the axle so the weight is carried equally on the inside wall and the outside wall of the tire. We weld the axle onto the walking beam at an angle. The road has a camber to it, especially a gravel road where the crown down the center is noticeably higher than the shoulders. Our tires match the road’s camber.”
Again, safety was a factor explains Sutcliffe. A wagon with 80 percent of the load riding on the inner walls of the tires is not a well handling implement. With uniform weight distribution across the full face of the tire surface, the tires do a better job of gripping the road, the wagon’s handling is much safer and the owner gets more miles out of those expensive tires.
The idea of an up and over tailgate has been common on European farm wagons for a long time, says Sutcliffe. A regular tailgate that’s hinged at the top, like those on any North American gravel truck, has some basic design flaws. They are often damaged because the load gets jammed up solid against it, or it may be wide open but a high heavy load bangs against it on its way down. Conventional tailgates can retard the sliding movement of product, and that’s bad news for the cycle time.
Jaylor’s up and over system uses a hydraulically operated gate that lifts high up and over the load, clearing the top of the trailer by four feet, allowing any type of load to slide out un-impaired. A heavy wet load of corn silage or distillers grain slides off never touching the tailgate. Sutcliffe says faster cycle times and reduced tailgate maintenance are two significant business benefits.
The other feature contributing to quicker turn-around times is the tapered box that’s four inches wider at the tail than at the front. Because the box becomes gradually wider as the load slides back, wall friction is cut.
“When we put our trailer side by side with some other brand(s), our load will be gone by the time the other wagon is 75 percent up. A straight side box will often hold the load until the box is all the way up… but the greater issue is safety. When dump trucks and big trailers roll over, it’s because the load is stuck at the very front of the box and the guy has to start jerking it around to loosen it up. We get the load to slide down while the box is still going up.”
Another piece of Jaylor technology is a hydraulic mechanism between the axles and the frame. The operator can move the axles toward the front or the back on the go. This adjusts the weight balance fore or aft.
“A lot of guys put a huge tractor on the front of a dump wagon simply because they need that weight to get enough traction in the field. Now, by moving the trailer axles, the operator can get whatever tongue weight he wants.
“It’s another safety factor. We’ve heard of a lot of accidents over the years when a guy is hauling grain with his dump wagon on a frozen road. Most of these accidents happen because he doesn’t have enough weight on the back of the tractor. He’ll hit the brakes and go sideways and end up in the ditch or maybe into oncoming traffic. The sliding axle lets him put as much weight as he wants on the tractor.”
The Jaylor approach to suspension on the tongue is different too. Sutcliffe says he uses a spring from a highway truck, which other trailers also do.
“The rubber suspensions normally used on dump wagons are so hard they don’t do anything when the trailer is empty. The tongue is always banging and crashing around. Whereas our system is quite soft when the wagon’s empty. It’s a lot less wear on the tractor and driver.
“Instead of mounting the spring parallel to the tongue, we mount it the other way. When you’re empty, one side of the spring is always working. When you’re loaded, the other end of the spring engages.”