The folks who follow the debate over aerial application’s rotary atomizers versus conventional hydraulic nozzles say it’s like comparing apples to oranges.
The common ground on the ground says they’re both round and supposedly good for you, fruit and nozzles.
A chief argument put forth by atomizer proponents is that conventional nozzles lack the ability to put product down into the crop under the canopy. That factor was explained in detail by atomizer builder Micronair’s Tim Sander when he visited Yorkton Aircraft last month to give workshops on the use and maintenance of the British company’s products.
Read Also
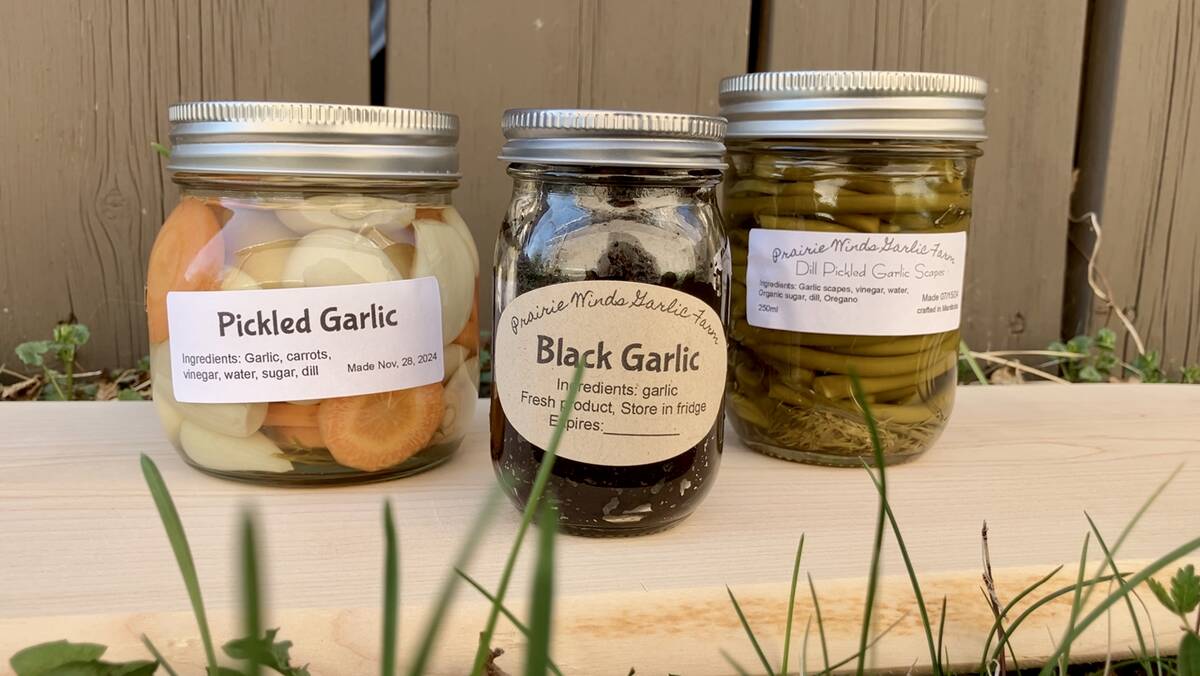
Growing garlic by the thousands in Manitoba
Grower holds a planting party day every fall as a crowd gathers to help put 28,000 plants, and sometimes more, into theground
Discussion about small spray droplets isn’t just about the numbers and the coverage you can get on a card laying on bare ground. More importantly, it’s about penetrating a dense foliage canopy, said Sander.
“When people compare coverage from a traditional hydraulic nozzle at three to five gallons per acre to a rotary atomizer at two gallons, they’ll produce water sensitive cards showing you small droplets from the rotary and lots of big droplets from the hydraulic nozzle. Opponents of the rotary then claim the hydraulic nozzle has as good or better coverage,” he said.
“But if you put that card deeper in the crop where the spray does more good, it’s a different story. Insects and weeds hide within that canopy. And when spraying fungicides, coverage is especially vital down in the foliage with the higher humidity because that’s where the disease lives and thrives.
“South America is the world’s biggest user of low volume fungicides. They found lower water volumes with smaller droplets gave the best results. They started out where you are now in Canada and the States at high volumes. Then they gradually went to low volumes.”
Micronair conducts wind tunnel tests that compare every major rotary and conventional nozzle on the market. Sander said the re-search is ongoing because new nozzles are introduced all the time.
The wind tunnel allows engineers to conduct what Sander calls a “perfect test” because it eliminates all outside variables that affect results when tests are run with real airplanes in real conditions. It’s impossible to repeat those same conditions on any given two days or even within the same hour of one day. Wind tunnel conditions are precisely repeatable, so results are more accurate.
“You put in all your operating parameters such as flow rate, air speed, temperature and everything else,” he said.
“We use a laser droplet sizing analyzer, which gives us very accurate results.”
Micronair’s website has an extensive nozzle spread sheet containing its data, called Droplet Size Calculator, under the heading Tools. The necessary password to access the tool is available to Micronair customers.
“There’s been a huge amount of wind tunnel work done in different countries, obtaining drop size data with rotaries and with various hydraulic nozzles. Countless studies show the droplet size spectrum with rotaries is narrower than that with a conventional nozzle,” he said.
“The atomizer eliminates big droplets. A big droplet holds a lot of product, which represents a big loss of volume and therefore loss of coverage. If you break a big droplet into smaller droplets, you put more useful product on the crop. Plus, the research shows that a rotary reduces the fines, which are the ones that can drift and evaporate.”
For more information, contact Sander at tsander@micronair.co.uk or visit www.micron.co.uk.