At the heart of every air cart in the new line by New Holland Agriculture, beats a new metering system.
The new system was designed to apportion seed and product at high rates and provide sectional control.
The air carts have individual metering modules for each run under each product tank. The P.4950 will be launched with up to 10 runs, which will supply a 10 run air pack.
“(However), they have been designed in the future to supply product for up to a 120 foot air drill, so we have the capacity to go up to a 12 run air pack on these carts,” said Trevor Remple, product marketing manager at New Holland.
Read Also
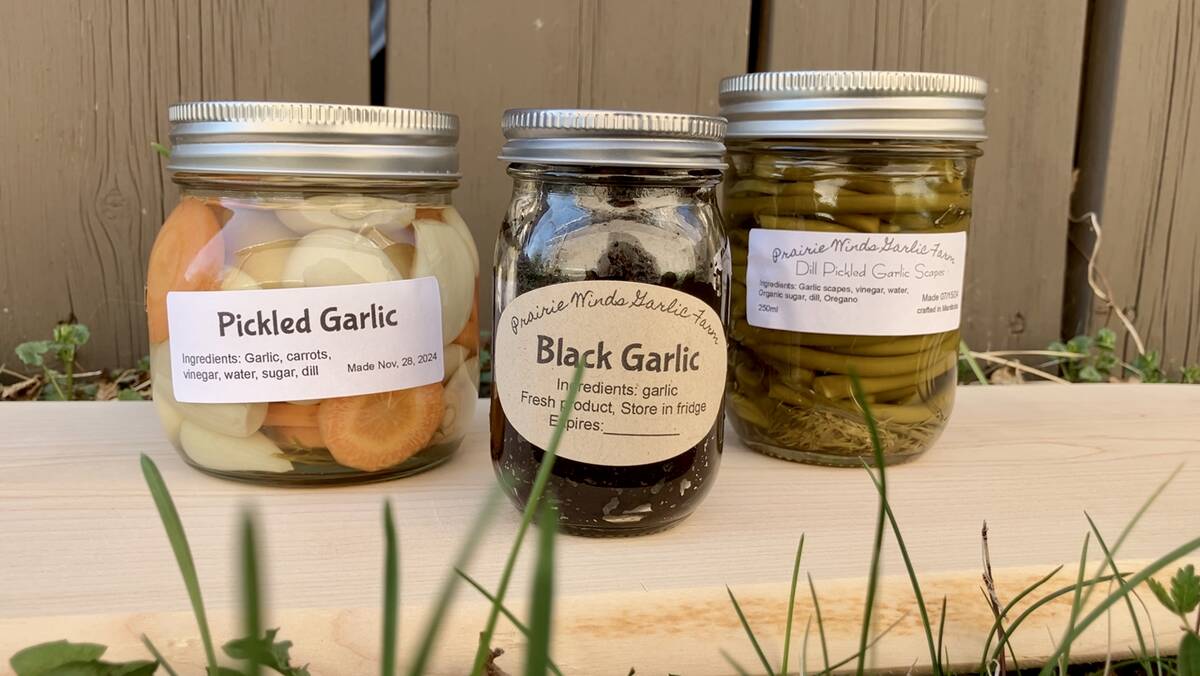
Growing garlic by the thousands in Manitoba
Grower holds a planting party day every fall as a crowd gathers to help put 28,000 plants, and sometimes more, into theground
The metering modules are powered by a 24-volt electric-drive motor, which fits onto the meter roller.
“The meter roller will supply all products, all rates, so you don’t have to change meter rollers for any of the products or any of the rates that you’re applying,” he said.
“It’s a multi segmented meter roller that has a fine segment and two coarse segments.”
Seven sizes are available: from 350 bushels with two tanks to a 950 bushel cart with four tanks, including a canola tank.
The two largest air carts are offered as tow-behind only, while the rest can be either towed behind or in between the drill and tractor.
Brakes come standard on the two largest models: the P.4760 and the P.4950.
The control monitor, called the IntelliView IV touch screen display, allows operators to set rates and make changes on the go.
Operators can move data in and out of the monitor with a USB, including prescription maps. The rate controller uses GPS technology and varies application rates by zone based on a prescription map.
The meter roller’s course sections are covered up when metering canola, and only the fine segment is used. The fine segment is covered up for most other products and the course segments are used.
“The full coarse will do pretty much all rates of fertilizer, cereals, peas and any other products,” Remple said.
“There is the option for the half coarse, but that is only ever required for some offbeat products.”
The metering modules are made of plastic and the hardware is stainless steel for corrosion resistance.
Operators can take the modules apart without tools when they need to be serviced.
Product can take four paths once it enters the meter:
- Calibration: The meter is closed, the product is calibrated through the meter and it drops out the bottom.
- Cleaning: A slide gate drops out of the way when the machine is being cleaned out. This is done by turning a lever at bottom of each tank, which opens each of the meters for each run on that tank.
- Blending: The product can be diverted into either of the two runs when operators want to blend product from any tank into either of the runs. This enables operators to apply product in a single shoot or double shoot application.
Each product run has a dedicated fan, and each fan has a dedicated hydraulic remote.
Remple said the hydraulic requirement for the air cart is 20 to 25 gallons per minute.
Three fill systems available:
- A manual auger on the smaller carts.
- A hydraulic auger is standard filling equipment starting at the 400 and 500 series carts. It is moved and operated by remote control.
- A conveyor option is available for the 400 series air carts and larger, which is moved into place by a remote control. The conveyer comes standard on the two largest models.
“The conveyer can fill 950 bushels in eight minutes,” Remple said.
“It fills twice as fast as the augers do. It’s the fastest filling auger on the market for air carts.”
The auxiliary tank is filled on the opposite side of the cart from the main fill.
“So you can start your fertilizer and come over here and fill your canola into the tank,” he said.
“It’s a ground level fill. We want to get away from having to go up ladders or move product up to the platform as much as possible. You can back your truck up to fill directly from your truck.”
Operators can also suspend a mini bulk bag over the hopper to fill the canola tank.
The largest cart in the product line, the P.4950, is 30 000 pounds dry weight.
The basic tire package has two duals on the back of the cart, which generates 29 pounds per sq. inch on the P.4950, Remple said. A high flotation package, which increases the P.4950 to 15 to 17 p.s.i. ground pressure, is available for all carts.
The company has increased its carts accessibility and safety. The staircase is a base feature on all the carts, and the catwalk on top of the tanks has been moved to the side so operators don’t have to step around tank lids.
Tank pressure sensors are standard equipment, which will alert operators if they forgot to close a tank lid after filling.
Contact robin.booker@producer.com