Tungsten ribbed rollers eliminate swather slippage and double the belt life
Swathing canola is a hassle when draper drive rollers slip because they’re wet or become coated with canola oil.
MacDon thinks it has a solution.
Conventional swather drives use a steel roller with a hard rubber layer vulcanized to the outer surface. They depend on friction to drive the belt.
The problem with this system is that moisture and canola oil find their way into that critical point where the rubber roller meets the inner surface of the rubber draper.
Ideally, friction should be 100 percent at this point, and it probably is when everything is new. However, MacDon developers saw slippage where the drive roller meets the belt.
Read Also
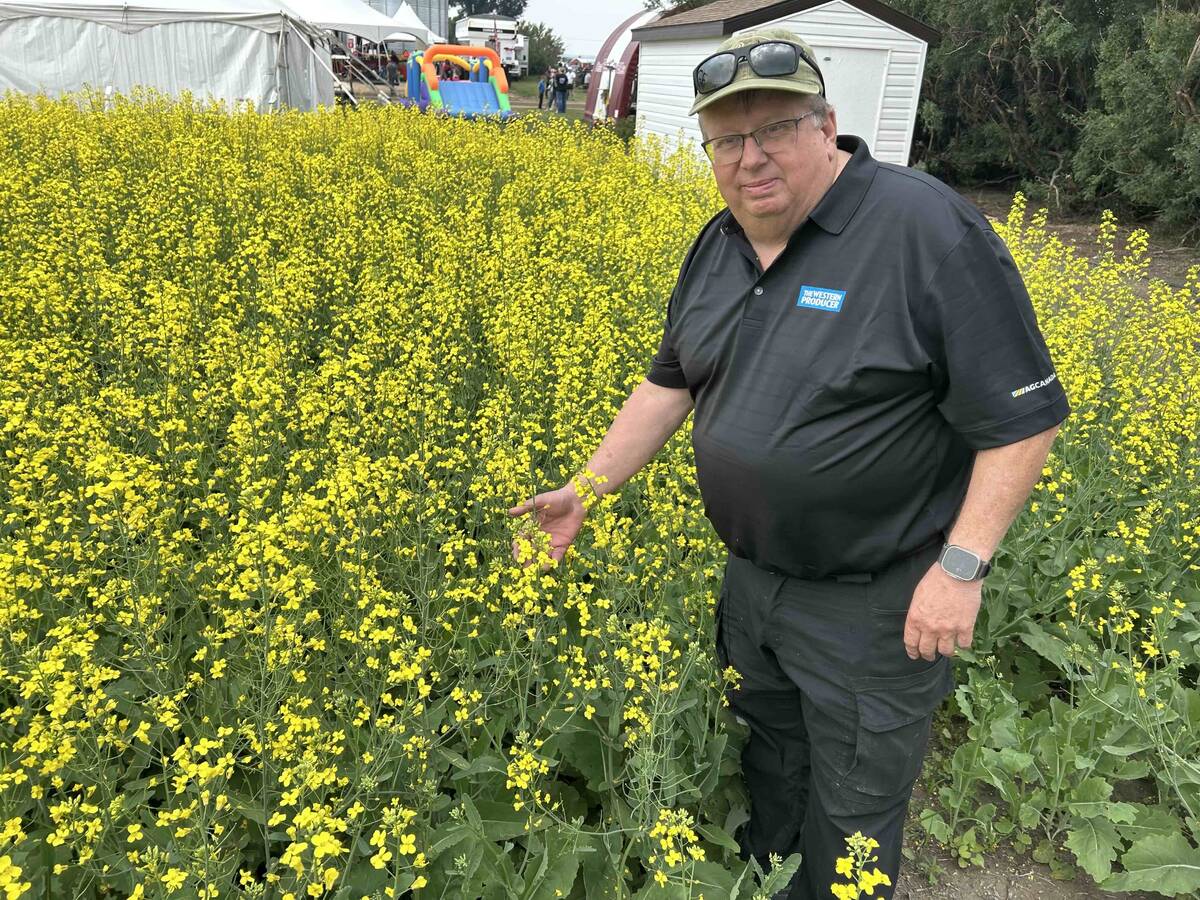
Crop conditions a pleasant surprise
Market analysts found some stressed crops and some good ones on pre-Ag In Motion 2025 crop tours,
Then Kondex, a Wisconsin-based research and development organization specializing in agricultural parts, entered the scene.
The challenge from MacDon was to develop a drive system for the draper belt that does not slip, regardless of circumstances or working conditions. As well, the design had to be simple so the entire swather didn’t have to be redesigned.
“Traction between the rubber drive rollers and the rubber surface inside the belt was not perfect,” said Keith Johnson, head of engineering at Kondex. “The slightest bit of micro slip creates heat, which actually polishes the two rubber surfaces. This contributes to poor performance in the field and ultimately deterioration of the belt and drive roller.”
Engineers delved into the challenge of reducing or eliminating slippage between the roller and draper.
They first determined that rubber rollers had too many inherent problems. Then they introduced a new concept; using raised steel ribs welded to the outer circumference original roller. Kondex engineers reasoned that steel ribs would do a better job of driving the canvas than vulcanized rubber.
After testing hard steel alloys, engineers determined that tungsten carbide ribs would give the result MacDon wanted.
“The reason we use tungsten is better wear resistance,” Johnson said.
“The abrasive soil conditions MacDon swathers work in will cause the more conventional alloys to wear faster. They won’t hold up. We tested stainless steel along with a number of other materials, but none of them have the wear resistance of tungsten. They weren’t anywhere near the acceptable level MacDon wanted.”
Johnson said the roller is a mild steel, and the tungsten ribs are applied using a process called laser cladding. The technology is similar to spray welding but uses a laser beam to control the material being applied.
He said the laser-clad rib material consists of tungsten carbide particles embedded in the matrix, which adheres to the host roller with a nearly indestructible metallurgical bond.
“The laser beam process is much more precise. The other benefit is that bond between the tungsten rib and the steel roller is by far superior to any other process or coating we’ve tried. And tungsten is very hard, so we know it will stand up.”
The designers also addressed the issue of inside wear on the belt surface.
“I admit we were a bit surprised when we saw the test results,” said Johnson. “The tungsten ribbed rollers actually doubled the life of the belts, so we ended up with far superior traction between the roller and the canvas, we eliminated micro slipping and we doubled the life expectancy of the belt.”
The Kondex tungsten ribbed roller, and MacDon, received the AE50 award for engineering innovations last year. It is available only on D65 swathers.