The ability to auger seed at the same rate as a rubber belt conveyor but with 4.4 percent less seed damage might catch farmers’ attention.
Researchers at Ohio State University recently moved soybean seed through a six-inch auger with poly cupped flighting, and ended up with a germination rate of 86 percent.
A rubber paddled belt conveyor, which was previously thought to be the best way to move delicate seeds, did not fare as well. Soybeans from the same seed lot had only 81.6 percent germination when moved through a six-inch tube with a rubber paddled belt.
Read Also
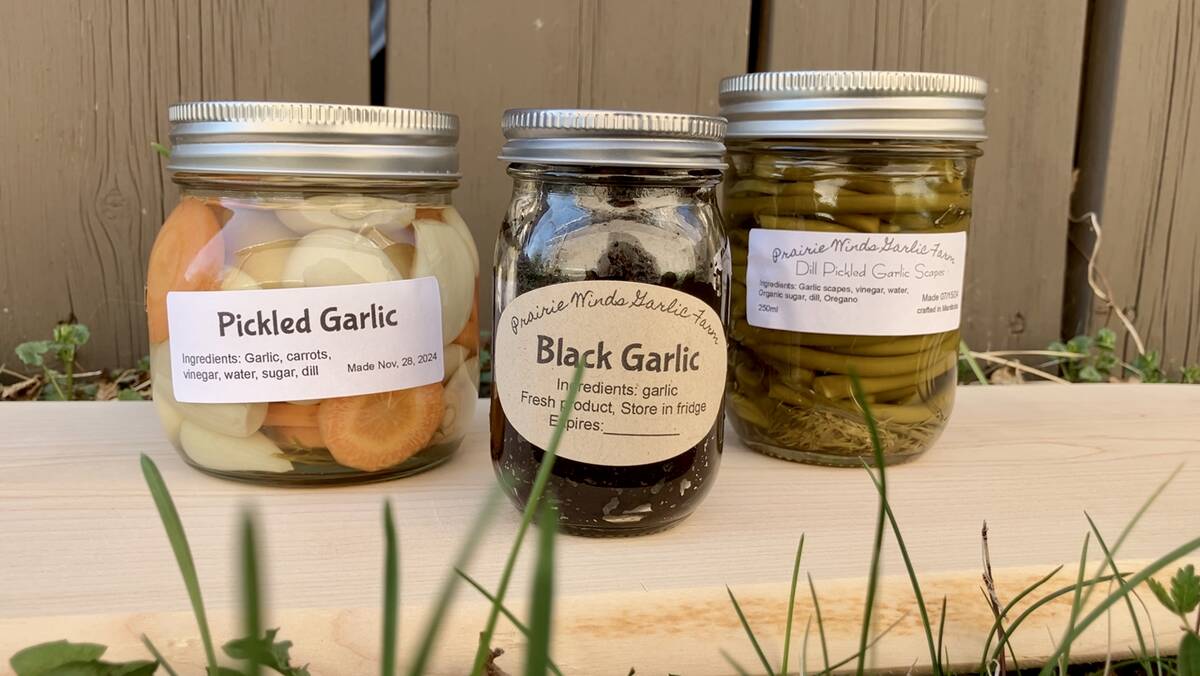
Growing garlic by the thousands in Manitoba
Grower holds a planting party day every fall as a crowd gathers to help put 28,000 plants, and sometimes more, into theground
Soybean seeds had an 80.8 percent germination rate when moved through either a conventional six-inch brush auger or a six-inch steel auger.
Seeds in the control group that were handled carefully by bucket to avoid damage had a germination rate of 87.5 percent, which was only 1.5 percent better than seeds moved by the poly cupped auger.
A five percent increase in germination is significant to the farm economy, considering that 80 million soybean acres are seeded in North America annually.
OSU researcher Randall Reeder, who was trying to find the best way to lift soybean seed with the least amount of damage, said he was surprised by the results.
Conventional wisdom for the past 20 years has been that the rubber conveyor is the gentlest means possible for moving seeds.
“Our most surprising conclusion was that the rubber belt did not come out as the winner. That was a real shock,” said Reeder.
The other big surprise was that the poly cupped auger seeds germinated nearly as well as the control group, which were moved without machinery.
Reeder has no experience with canola, but he was willing to extrapolate from his soybean project.
“The more prone any seed is to damage, the more important it is to have the gentlest conveyance possible. Sensitive seeds simply need better treatment.”
Canola growers who typically see a germination rate of 50 to 60 percent are taking note of the poly cupped technology and wondering if it might work for their tiny round seeds.
However, research hasn’t been done on how poly cupped auger flighting might benefit canola seeds coated with protection products that easily flake off because of rough handling.
There’s an assumption that gentler handling of canola seeds will result in less flaking, but nobody knows for sure without validated field trials, said Todd Botterill, western Canadian distributor of Travis seed carts, one of the few companies bringing poly cup technology to Western Canada.
Reeder said it’s difficult to distinguish the shape factor from the soft plastic factor in the unique poly cupped flighting. Either may have a positive effect on small canola seeds.
However, he said the one thing he’s sure of is that the combination of the two factors reduces seed damage.
“This flighting has a distinct cup shape around the tip of the flighting,” he said. “It’s designed to reduce damage caused by seeds being trapped and crushed between the flighting edge and wall of the tube.”
One theory is that the cupped edge directs stray seeds back into the main herd rather than allowing them to be stuck against the inside of the tube.
“I think the softness of the poly might be more important than the cup shape, but that’s so hard to determine,” he said.
“But we know that steel flighting is thinner and has more of a harsh edge compared to the poly, which has a thicker gentler edge.”
Reeder said OSU embarked on the study because the small seeding window and expanding farm size have forced growers to become more efficient at seeding time.
As a result, many producers use a dedicated gravity wagon as temporary seed storage and then transfer seed from the wagon directly into the product tank on their planter or drill.
Reeder said the process of lifting seeds from the gravity box and transferring them to the tank is where a lot of seed damage occurs.
Research projects conducted in the 1990s support Reeder’s statement. They compared conventional steel augers of the time to the new rubber belt systems and found that rubber belts on seed carts improved germination rates.
The OSU experiment that compared the poly cupped flighting to the steel auger, brush auger and rubber belt conveyor used seed lifting machines that were 16 feet long and set at a 35 degree angle.
All machines were adjusted to move 10 bushels per minute. This volume is at the low end of the range used on the farm, but it’s also the rate that causes the least amount of seed damage, so it gives better comparison results.
Speeds were varied with each type of machine, but the volume re-mained 10 bu. per minute.
The germination tests found that lower r.p.m. with a tube carrying more grain proved to cause less seed damage than higher r.p.m. with less grain in the tube.
The most extreme case was with the brush type auger. The germination rate was 78.5 percent running at 800 r.p.m. Seeds run through the same auger at 370 r.p.m. had a germination rate of 85.5 percent, representing a full seven percent benefit as a result of the slower auger r.p.m.
The team determined that slower was better because more grain in the auger served as a buffer and reduced the number of seeds that contacted the edges of the flighting.
As well, seed exit speed was re-duced at the nose when r.p.m. was reduced.
Reeder said seed damage can be dramatically reduced by installing padding at the nose on all types of augers and conveyors.
“The research team is convinced that the conveyance mechanism isn’t the only factor at play in moving seed,” he said.
“What happens when seed hits the top end of the auger is also important. Regardless of what auger or conveyor type you use, ensure that padding is installed at the nose where the seed changes direction. In any kind of operation, seed damage is always greatest at the point where it changes direction.”
A plastic deflector isn’t the same as padding because many plastic products have a surface hardness rating comparable to metal.
Reeder said seed damage is greater if the auger shows wear or wobbles within the tube.
Worn out motor mounts, bearings, shafts or any other component that causes excess bounce or shaking should be repaired before running seed through the machine. What works for commercial grain criteria isn’t necessarily good enough for seed.
“The important thing we can take away from this is that the combination of the poly material and the cup shape flighting create a huge benefit to the producer.”
For more information, contact Reeder at reeder.1@osu.edu.