ST.GREGOR, SASK. — Wilfred Mollenbeck is fiercely proud of being an elementary school dropout.
He walked away from mainstream education after Grade 8 and used the money he earned from a job to kick-start his real education.
“The first thing I bought with my first paycheque was a Lincoln welder. That’s where I started,” said the inventor.
The welder was his gateway tool in what became a lifetime of designing, engineering and building an eclectic collection of industrial tools, farm machinery and structures.
By far the most noticeable oddity on the farm near St. Gregor is the Jetsons-like, 840 sq. foot house perched on top of a 12 metre tall orange pole.
Visitors from around the world have wended their way up the elaborate orange spiral staircase to have a peek at the unique home, where Mollenbeck and his wife Joan spend their weekends.
Read Also
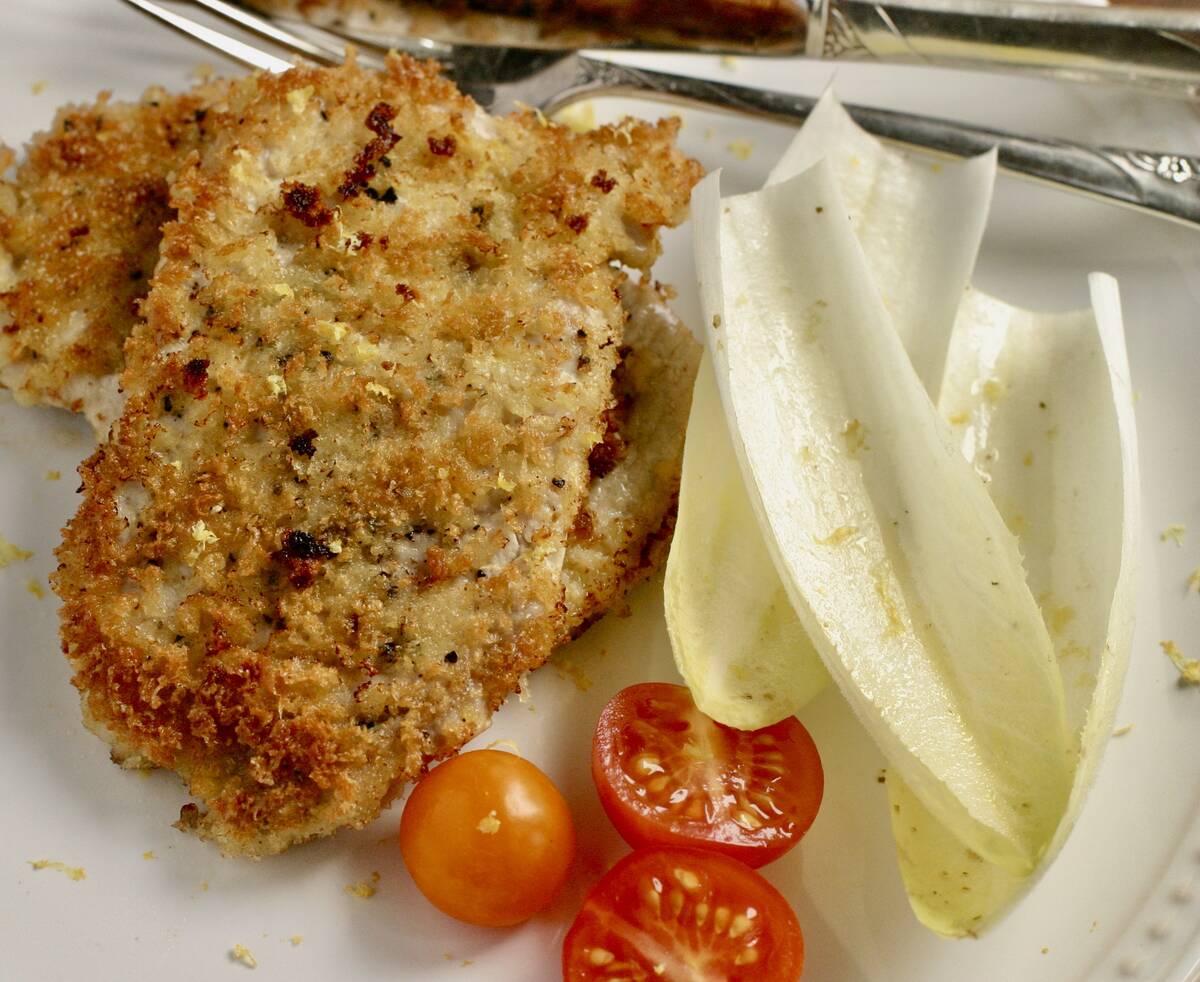
Nutritious pork packed with vitamins, essential minerals
Recipes for pork
Inside is one big open room with a bar in the middle, a bed and a bathroom. Mollenbeck handcrafted the intricate stools, chandelier and canopy bed frame using scrap metal gathered from around his shop.
It took two years to build the structure, which is secured by wires attached to I-beams embedded in eight-metre-deep concrete pilings.
“I got started on it and then I couldn’t quit because once I get going on a project, I’m kind of obsessed with it,” said Mollenbeck, who has no formal training in architecture or engineering.
The original plan was far more grandiose. It was going to be a three-level house with a glassed-in pool on the top level. And it was going to be three times as high.
There is a simple answer for why the project was scaled back.
“That’s all the pipe I had,” said Mollenbeck, who adds a chuckle to the end of pretty much everything he says.
He was similarly nonchalant when asked why he built the structure in the first place.
“I don’t know. Crazy people do crazy things,” he said.
“I always keep telling people my dad never wanted to build me a tree house, so I thought I’d build myself a decent one.”
Many of his creations appeal to local farmers, regardless of whether they were inspired by genius or insanity. Mollenbeck has sold about 100 grain trailers that he designed and built from scratch. He has also had success selling his grain hopper cones.
However, mass production is not his thing. It gets tiresome and boring.
“I build one-of-a-kind and then I get on with life. I just don’t like production line stuff,” he said.
“I could have turned a lot of things into a business if I wanted to, I guess, but I really wasn’t interested in that kind of stuff.”
What has become a business is Mollenbeck’s 8,800 sq. foot shop where he and his sons, Dennis and Kevin, repair farm equipment.
The boys have been working in the shop alongside their father since they were in diapers and welding since they were five.
“We were always around him, so we always watched what he was doing,” said Dennis.
“We started pretty young, making stuff and playing with things, tearing motors apart, you name it.”
Dennis is involved in most facets of the operation. He helps run the 2,700 acre grain farm and fixes and paints farm equipment in the shop.
He remembers his father giving the children free rein to build all kinds of things when they were young, such as go-karts, quads and hovercrafts.
“If we didn’t have a tool, we’d learn how to make it,” said Dennis.
Most of Kevin’s time is spent running the farm’s crane, which is hired out to lift roofs, bins and steel structures for buildings.
“At times it can be pretty hectic. You don’t know which way to turn,” he said.
The next generation is already busy in the shop. Wilfred and Joan have seven grandchildren from their two sons and two daughters.
Joan said their children and grandchildren have always gravitated toward the shop.
“They just love it,” she said.
“They’re just there and he helps them a little bit.”
The grandchildren are the reason the couple keeps 20 head of cattle, 50 hogs, some chickens and a dairy cow on the farm.
“The grandkids need a little bit of work, too. It’s a good experience for them. It’s nice to have your own meat and eggs and milk.”
The shop is filled with industrial tools built for a fraction of the cost of those sold in stores.
Mollenbeck has two homemade press brakes that bend and crimp metal into all sorts of shapes. They were made from I-beams bought from a salvage yard for $1,500 and hydraulic cylinders bought at auction sales.
The smaller three-metre long brake cost $5,500 to build. Mollenbeck cringes at the price of the six-metre, 2,000 tonne unit, which grew to $15,000 because he was in a hurry and had to buy new cylinders.
He estimates a factory press brake of that size would have cost $250,000.
On the other side of the shop is a cutting table Mollenbeck “cobbled together” in one afternoon.
“Please don’t laugh when you see this,” he said.
The tool consists of a drill attached to a gearbox from an angle grinder, and there is a holster where the cutting torch sits. It can cut a three-metre long sheet of 14-gauge steel in 30 seconds.
The $400 creation would have cost him about $50,000 in the store.
“I can’t afford the factory built stuff,” said Mollenbeck.
Fire destroyed the old shop five years ago. The new one, which cost $1.5 million to build, features two cranes that can reach any corner of the shop. It has 12 tie-downs buried in the concrete floor for straightening mangled frames.
“Most people don’t fix stuff like we do. They bring us some pretty impossible stuff to fix,” he said.
“Sometimes you sit there for an hour scratching your head first, trying to figure out what you’re going to do.”
The repair shop and crane business bring in more revenue than the farm, but Mollenbeck has innovations for the grain side of the business as well.
He and his sons built a grain dryer and cleaning plant from scratch, including the legs. An auger is mounted on an old Massey Harris combine, a homemade bale burner provides heat to the entire farmyard and the old 15-metre self-propelling swather he built in 1987 is still used today.
Any spare time Mollenbeck gets is spent on other projects, such as making a miniature Napoleonic canon out of scrap metal, flying his Cessna 172 and dreaming up his next inventions.
“I’ve got a lot of things in the back of my mind,” he said.
“I don’t even want to tell you (what they are). They’ll lock me up for sure.”