BRANDON – It takes 93 days for a bulk volume grain shipment to reach China from the centre of Canada, says Bob Hooper, inventor of the hopper container designed for the agricultural industry.
Grain shipped by intermodal container, on the other hand, reaches China in just 21 days.
“A single intermodal container can actually make a 42 day round trip,” Hooper said.
“That means a single container can make two round trips from the centre of Canada over to China in the time it takes for a single one-way bulk volume shipment using our regular grain cars and port terminals. Turnaround time has become so important when you deal with shipping efficiency.”
Read Also
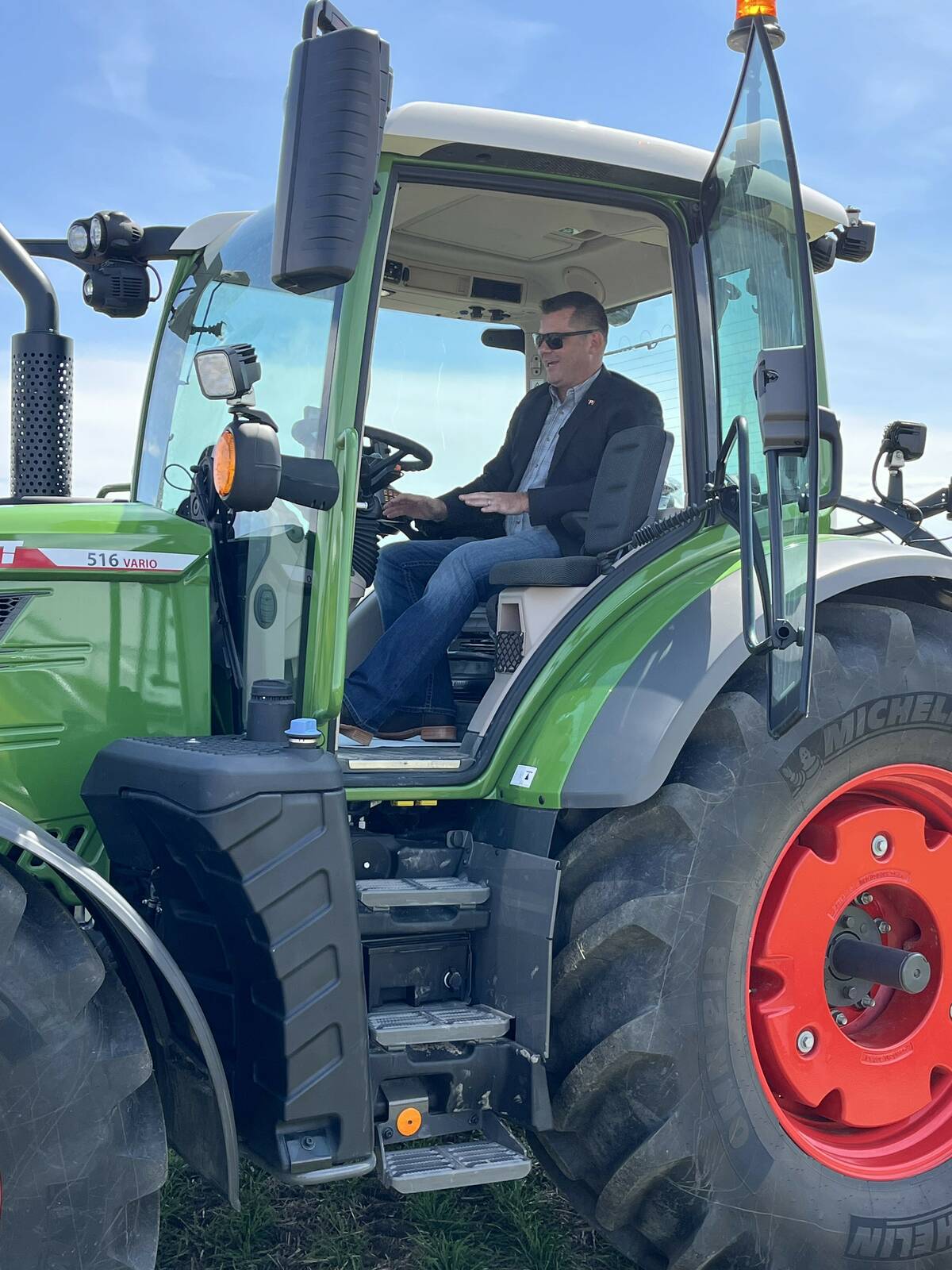
Farming Smarter receives financial boost from Alberta government for potato research
Farming Smarter near Lethbridge got a boost to its research equipment, thanks to the Alberta government’s increase in funding for research associations.
He said time really is money in the grain shipping business. Every time a shipper runs grain through an auger, he loses time and money.
As well, there is the constant risk of spillage and contamination, which often accounts for three percent of the total grain volume.
“We think the ideal situation is to load a container once and once only, on the farm, and then ship it directly to the customer.”
Hooper, a retired steel fabricator, spent years building and repairing rail cars and containers in the Transcona Canadian National Railway yards in Winnipeg. He and his three business partners, also retired CN welders, had a front row seat to study the steel and diesel side of Canada’s bulk volume shipping system.
He said it was obvious to them that not only is the rolling stock in the grain car system obsolete, but so is the concept of multiple loading and unloading. The idea of the conventional grain terminal isn’t far behind, he added.
Hooper said the world’s shipyards are building more container ships and fewer bulk volume ships for products such as grain.
They are now designing ships to carry 12,000 to 15,000 containers.
“Not only do ship owners get faster turnaround because of faster loading and unloading at port, but they also get better flexibility. If you own a ship with 12,000 containers, you can theoretically carry 12,000 different products. That makes your ship more valuable because it serves your customers better,” he said.
“That ship is never waiting in harbour for the right rail cars to arrive or the right grain shipments to build up in the terminal. If you own a grain ship, it just ships grain. If you own a container ship, it ships just about anything.”
A key feature of Hooper’s invention is that it fits every flatbed highway trailer, rail car and ocean going vessel equipped to haul containers.
That means whenever a freight train or ship is moving, it can carry grain along with the containerized lumber, televisions or lawnmowers.
In essence, grain movement blends into the overall system. Grain transportation no longer requires specialized highway trailers, railway cars, ships, inland terminals or port terminals.
“We load a container in the centre of a continent and we quickly move it to port. There’s no waiting for a special train,” Hooper said.
And when it arrives at its destination, there is no waiting for a grain ship to arrive.
“You can even load and seal the container right on your farm and it remains sealed until it arrives at the destination.”
He said there’s less handling of the product, less auguring and less exposure to contamination. There is no longer a need to touch the product once it’s loaded.
“Sellers can guarantee food safety and identity preservation for their buyer. With more and more IP (identify preserved) contracts, we need sealed containers to meet the criteria.”
Hooper predicted that when the country’s large grain terminals reach the end of their lifespans they will be replaced by new terminals designed to exclusively handle containers. The big port terminals and inland terminals will disappear from the Prairies, he added, just as the wooden elevators have.
Hooper said the idea of a hopper bottom container tailored for agricultural products came suddenly.
“As soon as we started talking about it, we knew we could design a better container for shipping grain and granular products,” he said.
The plan Hooper and his partners came up with was to build stackable 20 and 40 foot hopper containers specifically for grain and granular agricultural products. They named the containers SideTrackers.
“All four of us have spent a lot of time working on grain cars. We know there’s a very high cost involved in having special rail cars just to haul grain. And the farmer is the one ultimately paying that price,” he said.
“If you can find a way to haul more efficiently, the farmer can save money. If you can build grain containers that simply merge into the existing intermodal global system, it will save farmers money.
“Actually, anyone who transports any kind of granular bulk commodities that flows can benefit with these containers.”
Hooper said SideTrackers give the transport industry more handling flexibility. Conventional containers used around the globe are designed so the 20 footers are on the bottom and the 40 footers are on top.
Whenever the yard needs to access a 20 foot container, the 40 footers need to be hoisted out of the way. Even in situations where the 20 footers need to be taken first, the 40 footers must still be piled on top.
“All that repositioning is very time consuming and costly for the railroad. That’s a cost they pass on to the customer. I think we can eliminate that cost, at least for grain containers.”
He said SideTrackers are engineered to be fully compatible with all other containers now in use. The difference is that they do not require the 20 footers to go to the bottom of the pile. They can be mixed and stacked in any combination.
Grain flows into the top of a SideTracker through a 24 inch hatch. All mechanical controls can be worked from ground level to avoid climbing to the top. Controls are enclosed within the framework to prevent damage from the loading equipment.
Hatch covers also stay within the parameters of the outside dimension, whether open or closed, to prevent damage.
Grain flows out through a 20 inch hatch at the bottom of each hopper. The hatches line up top to bottom.
“If you have a stack of containers four high, each containing a different product, they can all be emptied one by one without removing any containers from the stack and without mixing product. All unload chutes and fill chutes line up perfectly. Locating pins on the frame keep everything aligned.”
A 20 foot SideTracker has two individual compartments and a 40 foot unit has four separate compartments. Each compartment is eight feet wide, 10 feet long, eight feet high and carries 20 tonnes of wheat. Hooper said the containers can be made of steel, aluminum or stainless steel if intended for granular fertilizer.
Shippers are able to mix and match container sizes because the 40 footers have centre supports to accommodate 20 footers stacked on top, unlike conventional 40 foot containers.
This provides six contact points for weight distribution instead of the regular four contact points.
Who will buy SideTrackers?
“We had farmers in mind when we first came up with this idea,” Hooper said. “It’s ideal for a producer who does a lot of IP contracts. I would think a group of farmers might get together to buy a bunch of containers, something like a co-operative. If you can arrange fast overseas turnaround, one container can haul a lot of product in a year.”
Even with 60-day turnaround, he said one container can make six round trips per year.
Hooper hopes to build the first prototypes this summer. He and his partners have not yet established a price.
For more information, contact Bob Hooper at 204-222-7604 or visit www.sidetrackersweb.com.