Biodegradable bags, bottles, containers | Company may look at building processing plant in Canada
Like millions of others, Michael Smith feels guilty when he eats at a fast food restaurant.
In his case, Smith doesn’t regret the fat and sugar in the meal. He feels badly about what ends up in the trash.
“Last week I ate at a (fast food restaurant) with my family. After dinner, we looked at it and saw all the plastic we had thrown away, the chip bag, the plastic bag the (sandwich) came in, the cups to the lids of the cups and the straws.”
Read Also
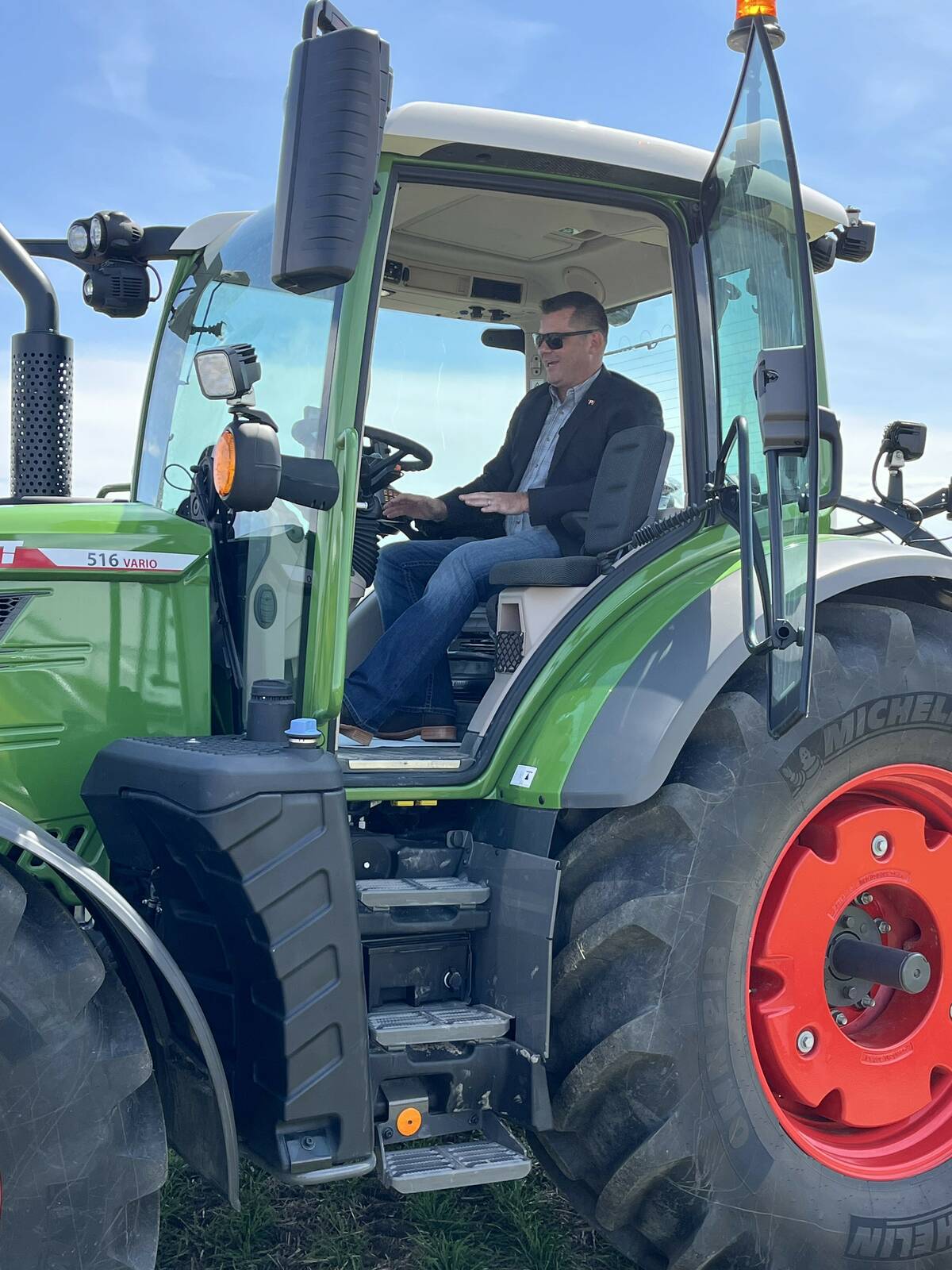
Farming Smarter receives financial boost from Alberta government for potato research
Farming Smarter near Lethbridge got a boost to its research equipment, thanks to the Alberta government’s increase in funding for research associations.
Unlike millions of others, Smith is doing something to reduce the amount of plastic in restaurant trash cans and in landfills. He is the chief operating officer of Meredian Holdings Group, a Georgia company turning canola into biodegradable plastic.
Meredian has built a bio-plastics processing plant in Bainbridge, Ga., using a process initially developed by Proctor & Gamble. Meredian scientists have refined the technology and can now manufacture a plastic polymer called polyhydroxyalkanoate (PHA) from canola oil.
“We can use any kind of oil that has a fatty acid, (which) will form a polymer,” Smith said.
“But canola is the best value of us. The strains that we use convert, dollar for dollar, more PHA from canola than we do from other seeds.”
The company has reached production stage after several years of development. This fall it signed contracts with Georgian farmers to produce 5,000 acres of canola.
And in early November, Meredian announced a $3.5 million investment to upgrade the plant to prepare for next year’s harvest.
“Several of our Fortune 100 customers are gearing up for increased volumes of biodegradable resin pellets to replace their petro-plastic products,” Paul Pereira, Meredian’s chief executive officer, said in a statement.
“This is a very exciting phase in MHG’s history, as we introduce products into the market that will revolutionize the way we view waste.”
Pereira, in a speech promoting Meredian and its technology, held up a coffee cup made from PHA bioplastic. He said the product breaks down rapidly after disposal.
“You can use it once, throw it in your backyard and in 90 days it’s gone,” he said.
Smith said global demand for bioplastics is large because companies want biodegradable packaging, whether they be food storage bags or beverage bottles.
“The worldwide plastic market is 660 billion pounds (annually),” Smith said. “Our market is not the issue. The desire for the product is well above what we’ll be able to make over the next 20 years…. We’ve got one customer … they make a product, just one product, that is two billion lb. per year. They’re asking us: how can we supply them.”
Smith said more than 300 million acres of canola would be required to produce enough PHA to satisfythe global plastic market.
Greg Calhoun, a company director and farmer in southwestern Georgia, has agreed to grow canola for Meredian.
He experimented with canola about 15 years ago, but like other Georgia growers, quit growing the crop because there were no buyers or processors in the region.
Calhoun said winter canola is a fantastic fit for growers in southwestern Georgia because it’s an opportunity to make money when the land is normally idle.
“We can double crop cotton, peanuts and soybeans behind this canola without any yield reduction in our summertime crop,” he said.
“You could be looking at making $150 an acre for wintertime canola and then make $250 an acre for a springtime crop.”
Calhoun grew 400 acres of canola for Meredian last year and planted 2,000 acres this fall. The farmland around Bainbridge is fertile and irrigation is common, so growers are accustomed to high-yielding crops.
Calhoun said canola grown in the area should yield 50 to 65 bushels per acre.
Smith estimated the Bainbridge plant would need 100,000 acres of canola when it reaches full capacity.
Meredian’s future challenge will be scaling up production to satisfy demand.
Smith said the company is committed to a manufacturing model called agro-facturing, which involves buying feedstock from local growers.
“We (want to) have plants in Canada, plants in North Dakota, plants in Brazil … and plants in Germany that only go a few hundred miles out to get their feedstock,” he said.
“The next two to three years we’ve got to start expanding rapidly…. Whether we do that with us building facilities or whether we license the technology and have others build it, that would be part of the decision making for our board of directors and our shareholders.”
More stories about Georgia’s emerging canola industry can be found in future issues of The Western Producer.