Henry Guenter was a service manager for Massey Ferguson for many years. Now retired, he decided to compile some of his observations on how to improve the operation of certain MF equipment. We have included a few regarding Massey combines. The rest of the information is available here: What your massey manual won’t tell you.
Your operator’s manual is a book worth studying. It has good advice but it cannot cover every situation. I have learned a lot at clinics, on farmer’s fields and talking to farmers at the dealership.
Read Also
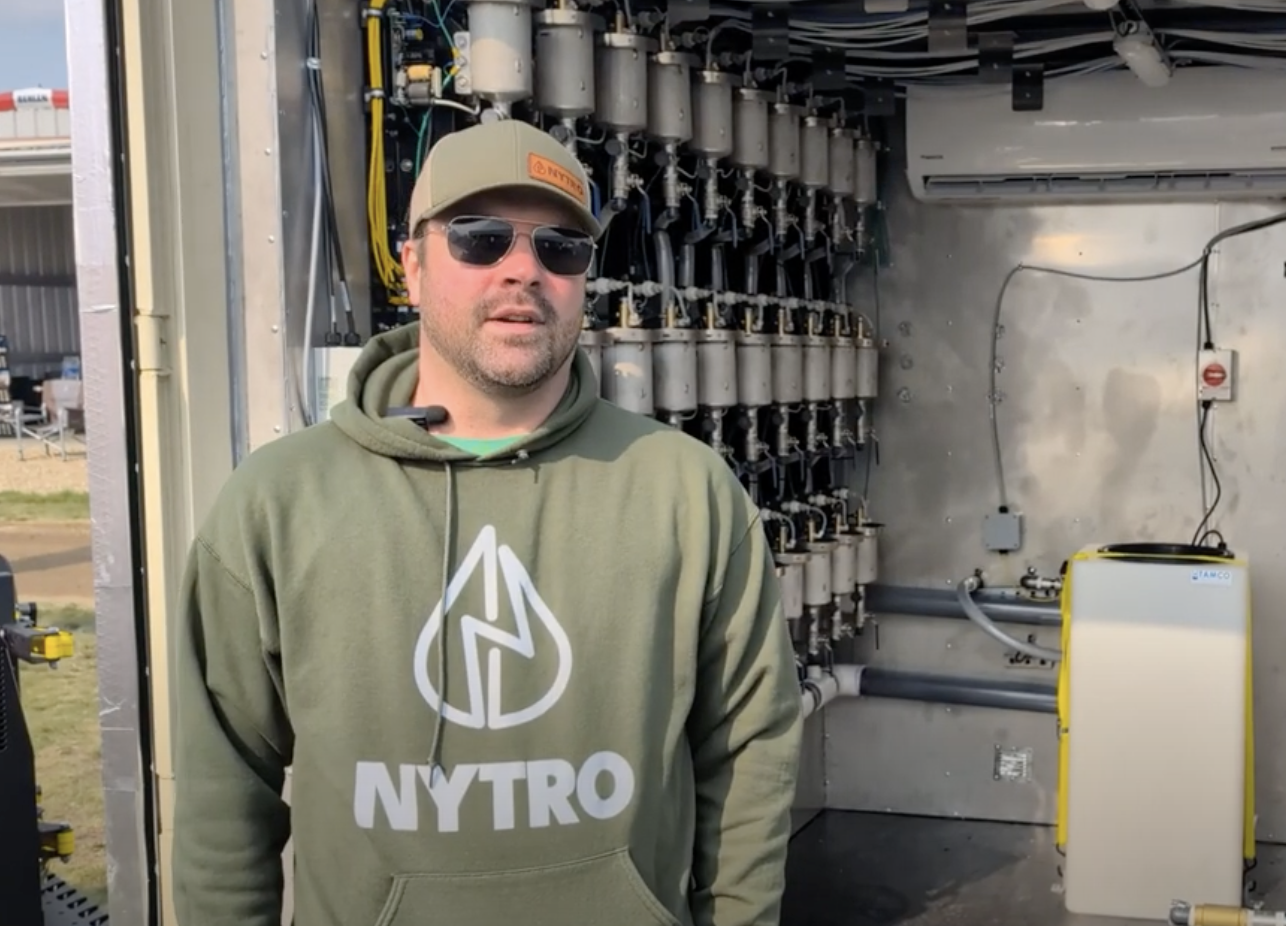
VIDEO: Green Lightning and Nytro Ag win sustainability innovation award
Nytro Ag Corp and Green Lightning recieved an innovation award at Ag in Motion 2025 for the Green Lightning Nitrogen Machine, which converts atmospheric nitrogen into a plant-usable form.
Rear beater speed
There is a speed at which the engine develops full horsepower and that is also the speed at which the combine is the most efficient.
On the combine with the rear beater speed of 740, you will have the best results at about 710.
This means you should be able to push the forward speed ahead increasing load until the speed drops close to 710, but the closer you get to 710, the more the engine seems to want to “hang on.”
You should be able to increase the load on the engine at this point without losing an appreciable amount of speed. If you push the combine until the speed drops to 680 or 690, you will not only notice an increase in losses, you are also getting close to plugging it.
The shoe and the walkers are designed to run at 710. Slower or faster will create losses.
This is a major issue on the pull-type combine because owners seem to think they have to push the throttle ahead to keep the speed at 1,000 rpm no matter what the load.
The combine is running too fast and you will have losses. Also you will have damage to the shoe, pitman arm and bearings because the combine will tend to run too fast when the load comes off at the corners.
Losses from the return
All unthreshed material goes back to the separator to be threshed again. This is called the return system. Many combines have something to handle unthreshed material. Usually it is fed back to the main cylinder. Obviously, the less you have in this system, the better.
On the MF combine, the rethreshed material gets blown onto the pan under the walkers. There is enough force to blow it to the left side and if there is a lot of it, you will encounter a lot of loss on the left side of the shoe in a strip about six inches wide.
Later combines had two paddles mounted to the bottom of two walkers directly in the path of this flow of material so that when one was up, the other was down. They can be installed in earlier units.
Concaves
In Canadian equipment there were two different concaves, a narrow spaced and a wide spaced. This referred to the distance between the rods.
The narrow spaced was introduced to take care of the hard-to-thresh Neepawa wheat.
It held the material up against the cylinder longer but that was also its weakness. The narrow space cut capacity in large kernel grain such as barley or durum.
Some owners tried to increase capacity by removing every other wire or rod. They found out that by removing them in just one bar, they gained about half a mile an hour.
If you decide to remove every other rod, make sure to close the holes left in the concave. The straw will weave into these holes and make a perfect basket.
Spot welding warps the concave. Bolts will cut capacity. Silicone is too soft. An epoxy like liquid steel is probably the best.
That will create a concave that is much like the wide spaced one, which could lead to another problem.
With all this experimenting you might notice losses over the left side of the shoe. You have overloaded the return and too much material is getting through the concave before it is threshed.
The answer is to put in concave blanks. You might need to blank as many as eight bars before you cured the problem, although at this point you haven’t got a lot of capacity left.
The blanks that fit underneath the concave are a lot better. They leave the bars exposed so they are threshing. You don’t need as many blanks. They are also easier to put in. You can pull the front of the grain pan out like a drawer.
The concave diameter is bigger than the cylinder. This means when you set the back of the concave tight against the cylinder, you cannot bring the front tighter than 5/16 of an inch because the middle will touch.
Walkers
For grain loss in this area, check the grate behind the concave. It should be within an inch of the rear beater.
When you plug the combine, it is possible to bend this grate down but then you won’t have the aggressive action you need. You can see this grate through the inspection hole on the right side of the machine.
The row of belt-like curtains behind the beater should have a natural curl to the back. If they are installed with the curl forward, the rear beater will eat them up.
Shoe
Air flow pattern on the shoe can be a problem. In some crops you never seem to get the air just right. You seem to get a lot of chaff in the bin and if you increase the air to blow it out, you start to lose grain.
The problem is an uneven air flow coming from the fan. On that type of fan, the air comes in from the ends and is in a crossing pattern when it gets to the shoe, so you will have dead spots.
With the combine running, spray different coloured paints into each intake and then check the bottom of the shoe and it will tell you the story. Some parts will be all colours and some parts will have no paint.
The answer is the fan dividers that were installed as standard in 1983. They will retrofit all combines.
Shoe assembly
Sometimes you will hear a pounding or feel a shudder that is much more noticeable when the combine is running empty.
Turn the combine over until the shoe is all the way back and of course the grain pan will be all the way forward. You will probably see that one corner of the shoe touches the frame and the opposite corner of the pan will touch the frame.
At this point it might not quite touch but you can see the wear marks. This can cause enough vibration to crack the walker body and shoe pan, break the pitman arm and ruin the bearings.
To square the shoe and pan to the combine, switch shims from side to side under the rocker shaft bearing supports.
Never add or remove from the total.
If the shoe and the pan are both touching on the same side, the rocker shaft is not properly welded.