It’s important that producers set their combines correctly before heading onto the field this harvest season.
Threshing is a key area. It is accomplished by rubbing unthreshed material between two rough surfaces: the concave and the rub bars on the rotating cylinder.
Material enters the front of the concave from the feeder chain and travels over the concave, pushed along by the turn of the cylinder. Ideally, only the grain should go through the concave and all the straw and chaff should come out the back between the concave and cylinder onto the walkers or the rest of the cage.
Read Also
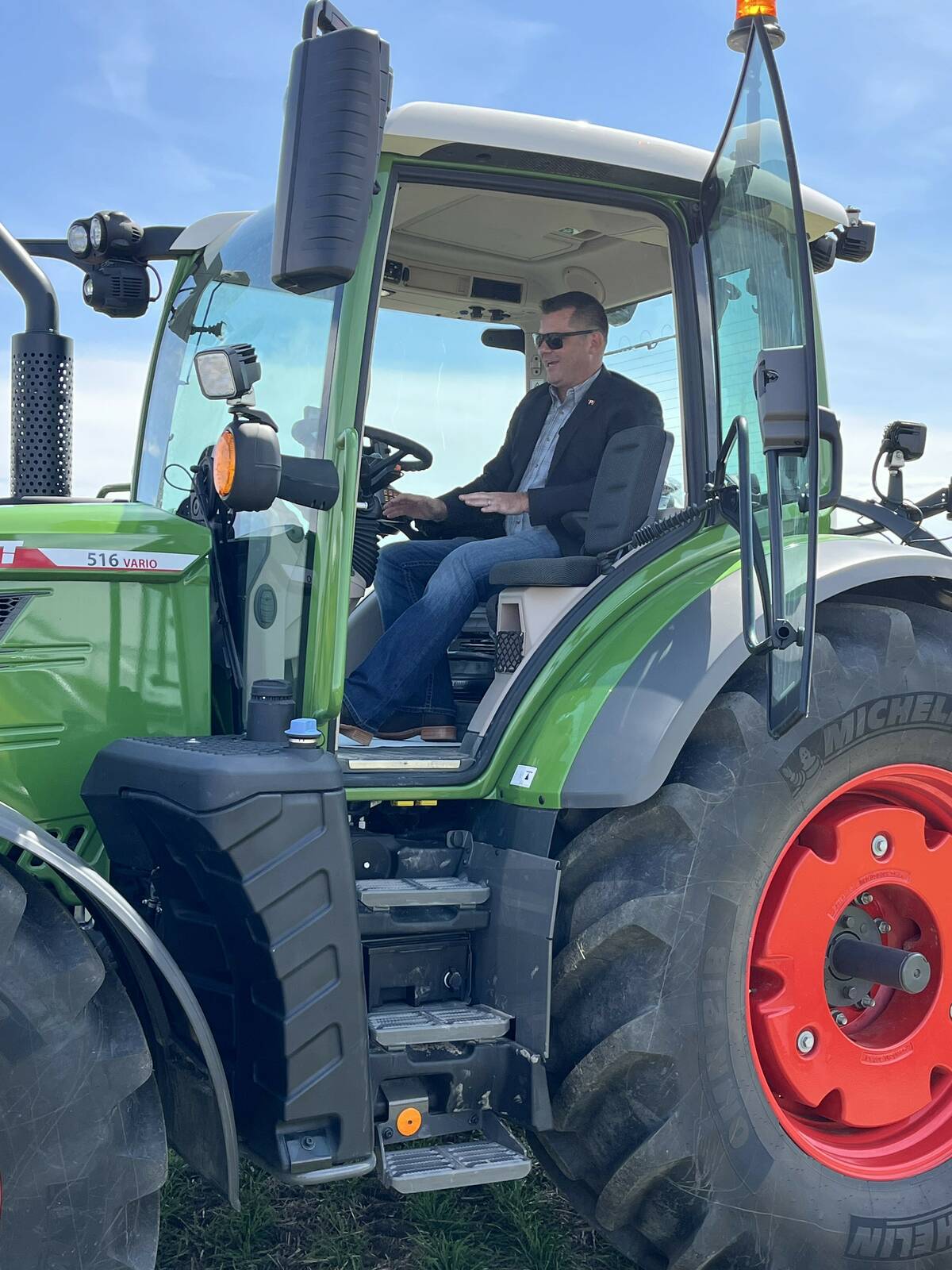
Farming Smarter receives financial boost from Alberta government for potato research
Farming Smarter near Lethbridge got a boost to its research equipment, thanks to the Alberta government’s increase in funding for research associations.
However, this ideal is not always possible to achieve. All the chaff will go through the concave with the grain, creating the need for the shoe or sieves. As well, some of the grain might be carried out with the straw. Your job on the combine is to get as close to the ideal as possible.
There are two things to check when determining combine efficiency:
- What kind of losses are on the ground behind the machine?
- What kind of a sample is in the grain tank?
It is wise to keep the sieves wide open so that everything threshed goes into the grain tank without going through the threshing cylinder a second time. People tend to close the bottom sieve when they find unthreshed material in the tank, but that severely cuts capacity.
When setting the threshing area, set the cylinder speed first. A general rule is that you set it as fast as you can without cracking grain.
Cracking is the result of speed, while crushing happens when grain is caught between chain and sprocket or concave and rub bar. You will have damaged kernels no matter how careful you are, but you should get less than one percent.
Speed provides capacity as well as momentum to carry the machine through the tough spots and keeps the cylinder from “slugging.” Speed may have to be limited in dry conditions because breaking straw will overload the shoe and cause losses.
In rotary combines, changing the threshing cylinder speed also means changing the separation cylinder speed. Because separation is accomplished by centrifugal force, the faster it turns, the more it can handle. Again, this determines capacity.
It is also important to set the clearance between the concave and the cylinder. When you push the concave up tighter against the cylinder, it forces more grain through the concave. Your best setting is where no grain escapes from between the concave and cylinder. You might end up with a clearance of “0” cylinder/concave.
Here is where the rotary shines. Instead of one pass over the concave, the material makes three passes so clearances don’t have to be so tight. Then it goes into a cage with the rotor spinning inside, and grain is driven out by force. The rotary combine can handle two or three times as much material because of its design.
Sometimes you will have whitecaps in the grain tank. The temptation is to close that bottom sieve just a little. That will clean up your sample but also reduce capacity and add a few more cracked kernels. It’s better to add one or two filler plates to the front of the concave to keep the material against the cylinder longer before it falls through the concave.
The chaff and the grain will fall onto a pan in front of the shoe. This pan shakes it back onto the sieve where the wind, created by the fan, can blow the chaff away. There should be just enough wind to blow the chaff out the back end but not partial heads and unthreshed kernels. They go back to returns.
Operators often set the bottom sieve so the grain falls through the sieve. This will give “fingers” of air that are strong enough to blow grain out if there isn’t enough volume to lift the chaff. However, this will result in losses as well as a dirty sample.
The bottom sieve must be open enough to let air through so chaff can be lifted on the top sieve. This is a big issue on small seeds such as canola, but it also applies to other crops.
Maintaining air flow will help handle a heavy chaff load on the top sieve. If this results in a lot of unthreshed kernels in the tank, fix your threshing problem back at the rotor or cylinder. Options include installing blanks or buying new rub bars. The more you thresh everything the first time, the more capacity you will have.
Trouble-shooting
Problem: Losing grain over the walkers.
Causes:
- Grain is slowing down because the belt is slipping, either because it is too loose or shiny. You can sometimes make a shiny belt work by rubbing a little brake fluid into the sides.
- Grate under rear beater is bent down (Massey Ferguson).
- Curtains over walkers are not in place.
- Too much clearance between concave and cylinder.
- There are too many blanks in the concave.
- Walkers are running too fast. This is
an issue with older pull type combines. Set high idle to 1,000 r.p.m. not loaded to 1,000.
- The operator is driving too fast.
Problem: Grain lost over the rotor.
Causes:
- Too much concave clearance.
- Rotor speed is wrong.
- Too many blanks in the concave.
- Grain lost over the shoe.
- Too much wind.
- The bottom sieve is closed too much.
- Accelerator rolls in bad shape (Gleaner).
Problem: Too much return.
Causes:
- Unthreshed kernels in the tank.
- Blanks needed.
- Rub bars are worn out.
- Cylinder is running too slow.
Problem: Cracked kernels in the tank.
Causes:
- Cylinder is running too fast
- Too much return.
Henry Guenter, now retired, is a former service manager for Massey Ferguson.