Guenter is a former service manager for Massey-Ferguson.
An important and seldom understood part on Agco’s Gleaner rotary N and R series combines is the pair of accelerator rolls found within the heart of the machines’ transverse or naturally mounted rotors.
The rolls’ job is to accelerate the threshed mixture of grain and chaff past a blast of air at up to four times the speed that gravity would normally provide.
The process, pioneered by Agco, is balanced so the chaff is blown over the shoe and out the back of the machine but the heavier grain is driven through this blast of air and lands on the shoe.
Read Also
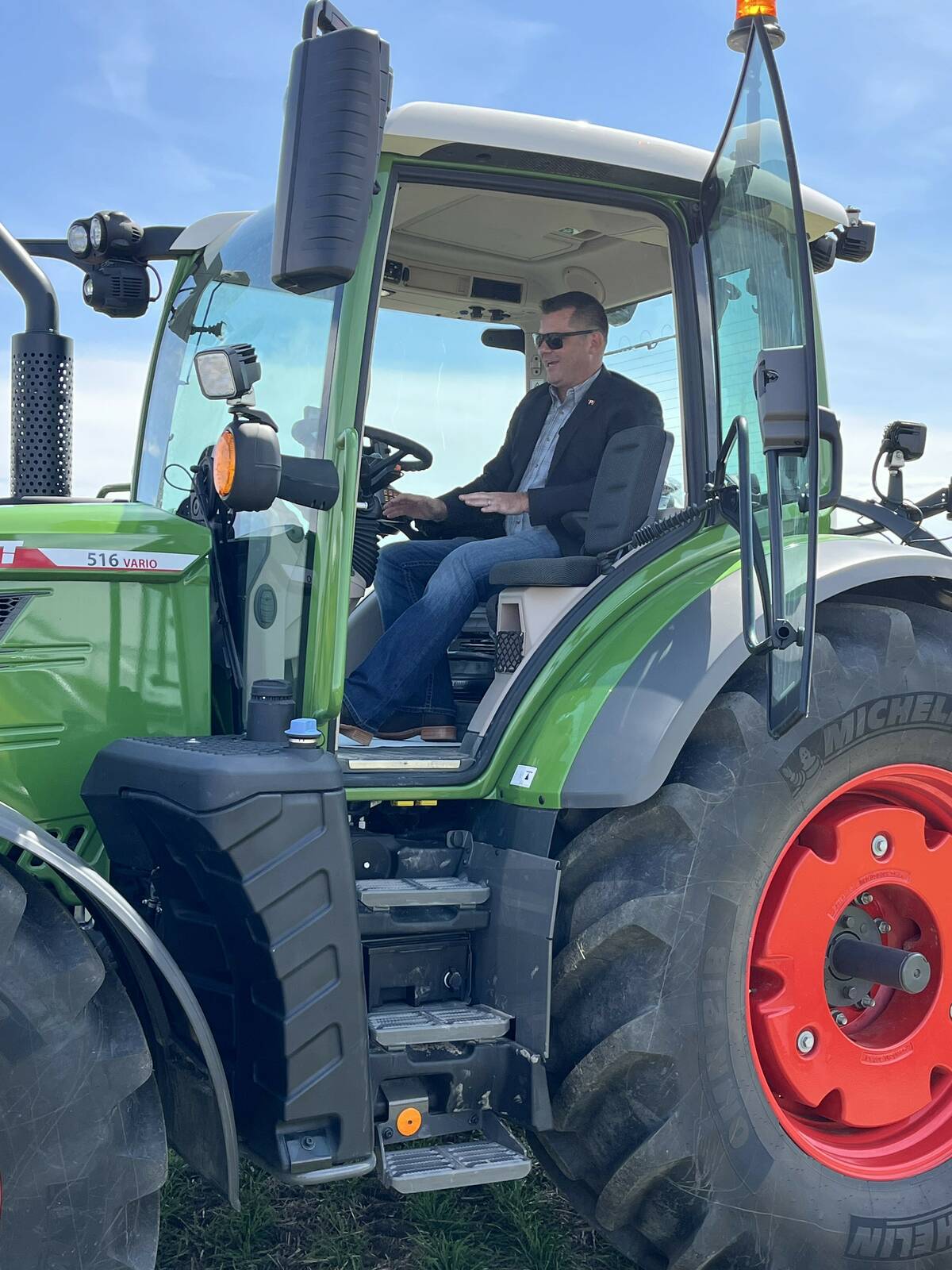
Farming Smarter receives financial boost from Alberta government for potato research
Farming Smarter near Lethbridge got a boost to its research equipment, thanks to the Alberta government’s increase in funding for research associations.
This is the secret of this combine’s design and is exclusive to the Gleaner and its transverse flow system. Producers will run into a multitude of problems if the accelerator rolls do not do their job, many of which they will blame on other factors.
Crop material loses acceleration when the rolls are worn or damaged. At this point, the combine starts blowing grain out of the threshing system and onto the ground.
As a wise combine operator, you will naturally reduce the air flow from the fan to keep that unexplainably light grain in the machine.
Now that you have reduced the fan’s output, the chaff won’t quite make it over the shoe, which loads it with chaff and straw.
However, because you’ve reduced air flow, you also don’t have enough air from the fan to do its other job – lift this unwanted material off the shoe. The result is a dirty sample and more losses of grain over the back end.
You probably haven’t solved the problem you started with -blowing grain on the ground – and now you are also sending it out with the chaff on the overtaxed shoe.
When it gets this bad, you start filling up the distribution trough because the rolls aren’t taking the grain away fast enough from the cylinder. Compounding the problem is that you don’t have enough separation area left and you throw even more grain out with the straw. Soon the trough becomes so full that the oscillating cage sweep at the top of the rotor starts to drag and plug.
Check the accelerator rolls for wear. You might pick up a lot more dirt than expected in some crops or in a poor year, which increases the wear rate of the rolls.
In small-seeded crops such as canola, the condition of these rolls is more critical to maintaining combine capacity. I know the maintenance book gives you a wear tolerance measurement, but in some conditions you might have to change them sooner than that.
Ask yourself if the rolls are doing their job. If not, what else can you do but replace them? But before you do that, there are two other things to check.
First, you need to know how the transverse fan functions. It works on a volume of air determined by the machine’s intake of air, or choke, rather than the speed of the fan.
The transverse fan is a round drum comprising blades that extend its full length. They are shaped so that when the drum turns, it pressurizes the inside of the drum.
To draw air from the fan, we “scoop” it with cut-off points so that we create a vacuum outside the drum. The pressurized air from inside the drum rushes to fill the vacuum just outside the drum, resulting in a powerful air flow from the transverse fan.
The amount of air is determined by the choke, but also by the distance from outside of the fan to the cut-off point.
If the cut-off point is not the same distance across the entire drum, we get an uneven flow of air across the shoe. Then you won’t be able to clean up your sample no matter how you play with the system. The transverse fan is the culprit.
The air flow pattern coming out of the opening just below the accelerator rolls can be a problem if previous maintenance has been done incorrectly. It can be evaluated by the tell-tale pattern worn on the sidewalls of the body of the combine.
The metal’s surface paint will be worn from material passing through the machine, and this wear mark will be an oval shape.
If the oval points down, this means the blast of air is blowing the chaff down on the shoe, which is not what you want. The pattern should point toward the back of the machine.
If the pattern points down, it means the rolls housing and fan housing are incorrectly assembled. To repair this, look for a row of bolts ahead of this area. These bolt the lip of the accelerator housing to the fan’s air chamber below. They should be bolted together so the upper lip is behind the lower lip. The Gleaner parts book shows the correct order for these pieces.
If these two issues are not your problem, make the drive to town and buy those new rolls.