The 2019 harvest from hell has many producers assessing their grain drying capability. This includes upgrading current systems to add capacity and automation, while for others this means a first foray into grain drying equipment.
In some regions, grain drying is a fact of life for most harvests. In other regions, there will be years and sometimes many years in a row when some harvesting patience along with aeration fans can easily accomplish the task. Sporadic, unpredictable use makes it more difficult to justify a significant investment.
With many producers upgrading their systems this year, more used dryers are on the market, but some are decades old and look rather scary. The time to buy a used dryer is after a couple years without prolonged harvests. In a wet harvest crunch, they magically increase in value. Even dryers that have been sitting in the bush for years hit the market when demand is high.
Read Also
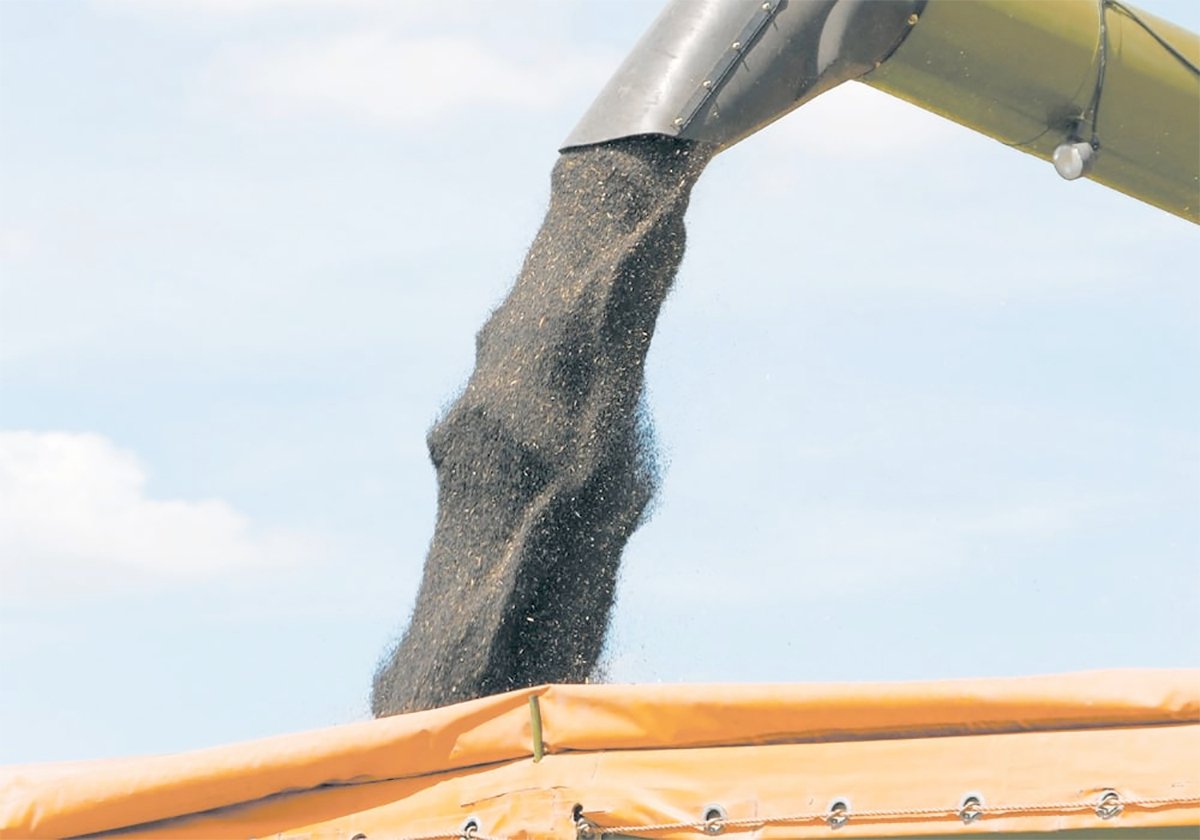
Determining tariff compensation will be difficult but necessary
Prime minister Mark Carney says his government will support canola farmers, yet estimating the loss and paying compensation in an equitable fashion will be no easy task, but it can be done.
Some producers get by with heating systems attached to aeration fans. This is a much lower investment, but certainly has its limitations. Grain at the bottom of the bin dries first and can become overly dry if you don’t keep rotating it. And it’s difficult to get a handle on just what the overall moisture content is within a bin.
Commercial drying facilities are typically attached to grain terminals. Their capacity along with access to natural gas rather makes them a cost competitive option. However, in the regions where wet harvests are not the norm, grain companies haven’t invested in drying capacity.
Extensive grain drying this fall has created a large carbon tax expense that has enraged growers. In reality, the carbon tax will inflate the price of many farm inputs, but that increased cost will largely be hidden. With propane and natural gas, the carbon tax is clearly visible and adds up to thousands of dollars for producers drying large quantities.
Producers without adequate drying options are more likely to leave crop out over winter. Drying is a significant cost, but leaving crop in the field for a spring harvest can be even more costly.
Beyond dryers, harvesting in short, cold days leads to other considerations. Without a combine equipped with a block heater, I’ve resorted to a propane heater borrowed from a neighbour to warm the engine enough to get it started out in the field. I’ll be investing in a propane heater of my own and will consider adding some sort of electric heating system to the combines for another year.
It would also be good to have a smaller electrical generator. Loading the one we have is a two- person job and it takes up a lot of space in the tool truck.
We have an ancient tandem grain truck that’s still in service. I didn’t realize until the temperature plummeted that the block heater was burned out. Despite the truck being decrepit, it needs to function when needed.
And cold weather quickly tells you which batteries are getting weak. When you count up how many batteries you rely upon, it’s a scary number. A good, long set of booster cables are worth their weight in gold, but weak batteries need to be continually culled from the herd.
A large, heated shop would certainly be nice, but that isn’t in my budget for the foreseeable future. In the meantime, how come there are never enough extension cords?
Kevin Hursh is an agricultural journalist, consultant and farmer. He can be reached by e-mail at kevin@hursh.ca.