U of A research University asked to find creative uses for undesirable products of livestock industry
Getting rid of specified risk materials is a 300,000 tonne problem.
These materials are the suspected carriers of BSE and under Canadian law must be destroyed and removed.
However, destroying the disease agents found in brains, spinal cords and other potentially infected bits is costly. Enter researchers at the University of Alberta, who were asked to find creative uses for an undesirable product.
“The industry came to us and said, ‘we have a problem, we have a lot of material that we can’t send anywhere,’ ” said chemical microbiologist David Bressler.
Read Also
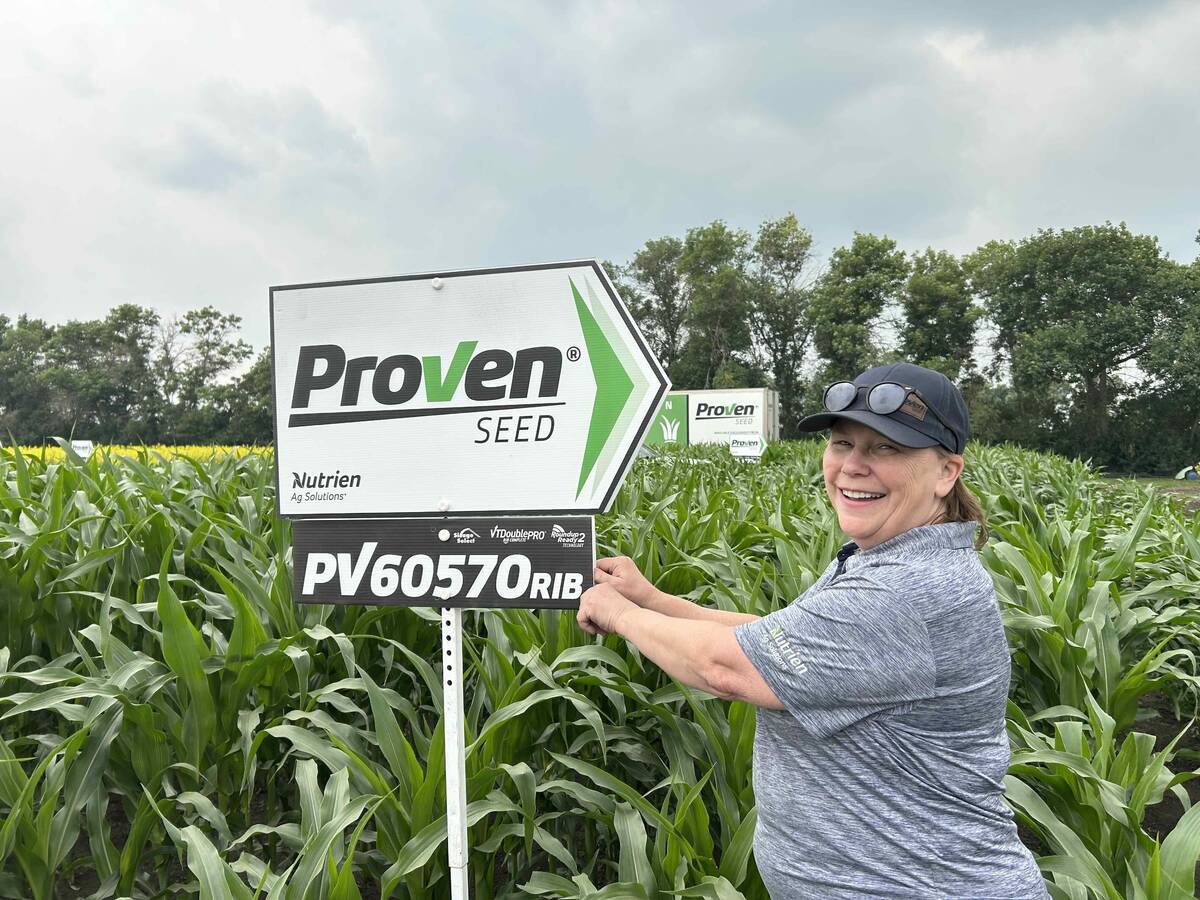
Ag In Motion 2025 site hub of activity
day before Ag in Motion preview.
He estimates separation and disposal costs are $70 to $200 per tonne. His research team is looking at making plastics and adhesives with high value, industrial uses.
“I wanted to take that protein, render it safe and now make something more valuable,” he said.
His laboratory had to be able to accept everything from raw to rendered material for the experiments.
“At the university lab I have more requirements for handling SRM than I do handling radiation material,” he said at the Alberta Livestock and Meat Agency conference June 19 in Calgary.
ALMA provided funding for the research.
The early work looked at turning blood and bone meal into firefighting foam.
The next step was breaking down the proteins to the lowest molecular form to see if they could make bioplastics or wood adhesives.
About two years ago they started figuring out what the plastic would look like. It has been tested for stress, strength and water absorption to make sure it does not dissolve in water. It proved to be a strong, durable product.
While some industries are looking at using SRM for energy or fertilizer, Bressler thinks there is higher value in bioplastics and adhesives used in car parts, fence posts and other heavy duty plastics. It will never be used to package food.
Researchers are also working on strengthening the plastic by combining it with other renewable products such as hemp or flax to cross bind it.
Adhesives were developed to make plywood, but a more probable application will be to make pellets that are burned for energy.