A $1.3 million project that turns manure into electricity at a Cudworth, Sask., hog farm is now generating power and a second phase that will produce fertilizer is on deck for 2005.
“It went smoother than we expected, which was great, and that’s certainly in part due to the company we work with in Germany,” said Clayton Sparks, sales and marketing vice-president of Saskatoon company Clear-Green Environmental Inc.
The German firm Krieg and Fischer has designed and built more than 100 biogas plants around the world, he said.
Read Also
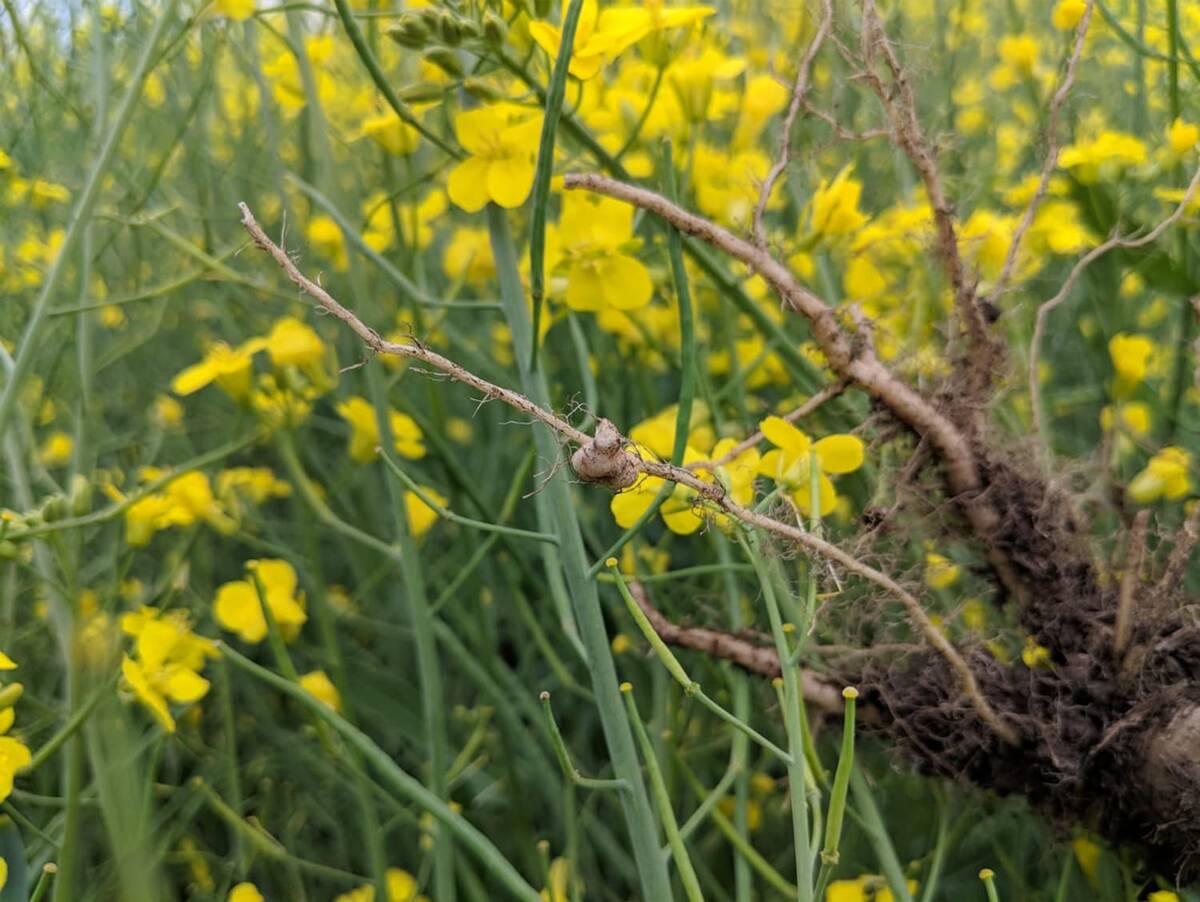
Going beyond “Resistant” on crop seed labels
Variety resistance is getting more specific on crop disease pathogens, but that information must be conveyed in a way that actually helps producers make rotation decisions.
“They’ve went through it a number of times, made the mistakes, know what works and what doesn’t and it’s been good having them on board to coach us through this first one,” said Sparks.
Manure from the 1,200 sow farrow-to-finish operation is heated to 37 C in a large enclosed tank called a digester and bacteria are introduced to feed on the organic matter. Methane gas, a byproduct of the digestion, is formed, metered and channelled into four SaskPower micro-turbines that convert the biogas into electricity that is fed into the power grid.
That creates 120 kilowatts of green power, enough to power 30-40 homes. Hot water from the micro turbines is pumped back to warm up fresh manure from the barns in a closed loop system.
Cudworth Pork Investors Group gains a waste management facility from the deal. Before partnering with Clear-Green, CPIG applied the manure to 2,400 acres of land as fertilizer. The method raises social and environmental issues.
“Anytime that there is a barn being built there is opposition and they always talk about ground water contamination and odour. Those are probably the biggest issues that are out there. I believe with this project we are addressing both issues,” said Don Kolla, CPIG general manager.
He said the hog operation had to adjust flushing schedules to ensure the consistency of manure necessary for the buffer tank, but he said those changes were minimal.
Kolla called the project an experiment based on cost efficiency. To be accepted in the hog industry, the cost of the power generation technology has to be comparable to what an operation pays to handle and dispose of its manure.
“If it’s going to be the same, it’s going to eliminate a lot of the headaches and is going to be the way of the future,” he said.
For SaskPower, participating in the project demonstrates the feasibility of producing energy from manure. In the next decade the utility will have to make a decision on replacing 2,000 megawatts of electricity generation because a number of generating units will have reached the end of their life. The manure project is one of several alternative energy pilot projects with which it is involved.
“These green power projects are really useful because they allow us to add power to meet demand and are still environmentally friendly,” said Larry Christie, SaskPower spokesperson.
“They are also giving us time to more clearly understand what the large technology will be in the future when we have to make that decision on the big power plan.”
Terry Page, supervisor of distributed generation and supply development projects at the power utility, said the startup experience at the Cudworth plant went well.
“We waited for the quality of the gas to reach a point where the turbines could actually burn it. And that took some time but is one of the things you have to deal with during startup. And once that happened the thing just took off and the turbines just gobbled up that gas and are producing electricity and it’s been running very well.”
Sparks and Kolla agreed the biggest challenge in the project was related to its wintertime construction, which was costly and resulted in some major underground repiping.
Phase 2 of the project, which will add equipment to extract, process and refine nutrients from the digested manure to produce high-quality organic fertilizer, is scheduled for construction this winter and should be completed by next fall.
The nitrogen, phosphorus and potassium mix will be blended down into a concentrated liquid organic fertilizer and sold primarily to off-farm markets such as golf courses, greenhouses and organic operations.
“It’s got a lot of appeal when it comes to the niche markets of organic, earth friendly, recycled types of labels where they’re not using chemically produced nutrients,” said Sparks.
Clear-Green wants to do a second demonstration project at another Saskatchewan hog operation that will process more than manure. It plans to produce energy and fertilizer from dead stock and slaughter waste, fulfilling an increasing need for alternatives to rendering. Because of controls introduced to prevent the spread of BSE, dead stock and slaughter byproducts that once were rendered into animal feed and other products must now be disposed of in other ways.
“What we’re proposing to do in this project is put in some specialized equipment where we can accept dead stock from (the partner’s) operation and a number of different hog operations in the area. So we would have manure, dead stock and slaughter waste from a slaughter plant nearby.”
Manure is a fairly consistent solution, but dead stock and slaughter waste processing would include skulls, hoofs, bones, hide and hair that need to be liquefied, he said. They would have to be treated before going to the digester.
“We’re looking at utilizing a thermal pressure hydrolysis process. It uses high temperature and high pressure that liquefies anything that goes into it.”
Sparks said the heat and pressure would destroy pathogens and conceivably be able to deal with specified risk materials, tissues that in BSE-infected cattle contain the agent that may transmit the disease.
The project would process about 30 percent more material annually than the Cudworth project and double the gas production.
The end use of the energy is yet to be determined.