Grant Humphrey has laid awake nights wondering why no one else can come up with a hypodermic needle detectable by slaughter house equipment.
“It’s not rocket science,” said Humphrey, explaining he doesn’t have a background in metallurgy or food production.
The 34-year-old high school graduate makes an unlikely David to take on well-established needle manufacturers.
He first heard about the problem of undetectable needles last October through a social connection.
Dave Wasylyshen of Canada Pork International had been given the task of finding a solution. His wife knew Humphrey, a laboratory equipment salesperson.
Read Also
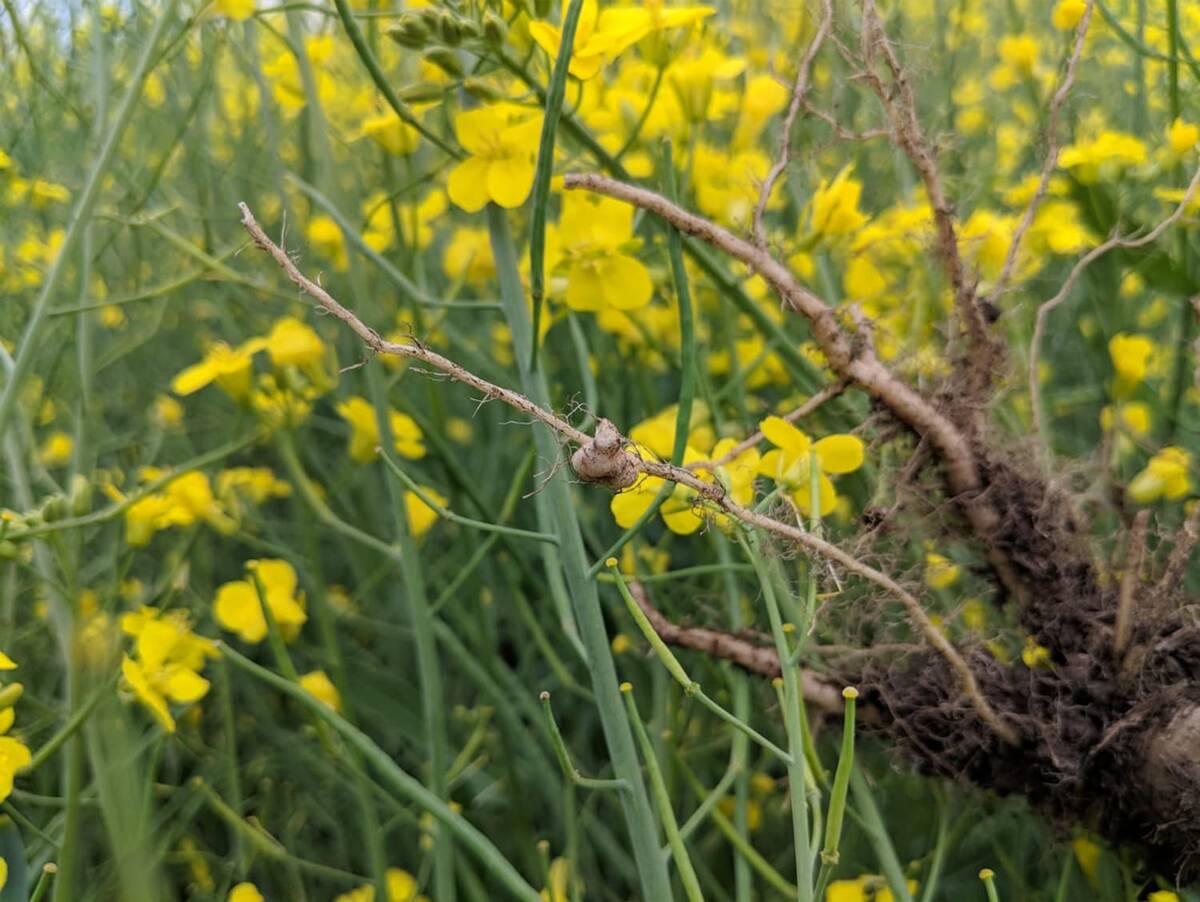
Going beyond “Resistant” on crop seed labels
Variety resistance is getting more specific on crop disease pathogens, but that information must be conveyed in a way that actually helps producers make rotation decisions.
Humphrey was surprised to learn that a standard needle placed on top of a piece of meat can pass through a packing house metal detector without setting it off.
He researched other alloys at libraries and on the internet, and talked to people in the stainless steel business about the dilemma.
When he found an alloy that looked promising, he used a hand-held grinder to make a crude prototype, roughly the size of a 20-gauge needle.
Wasylyshen imbedded the prototype in a four-kilogram pork loin butt and tested the meat at the J.M. Schneider plant in Winnipeg.
The alarm bells rang.
Ready for action
Humphrey thought he would be able to move into mass production quickly. He had been selling products for other people for 15 years, but had always wanted a product line to call his own.
However, he knew third-party independent testing was critical.
The Canadian Pork Council and the Canadian Cattlemen’s Association helped Humphrey with some research costs.
He bought 30 metres of the material at great cost, and developed a hollow needle prototype.
Wasylyshen tested 2.5, one and 0.5 centimetre pieces of the needle in meat at the Schneider plant, and found it detectable 95 percent of the time.
Then, Wasylyshen sent Humphrey to Iowa to see Paul Sunberg, director of veterinary issues with the National Pork Producers Council. The Canadian and American pork councils sponsored a joint study of the needle’s strength at Iowa State University.
But Sunberg also wanted to see test results from a larger 16-gauge needle, so that meant another prototype and another round of tests.
They found that the larger needle was detectable 100 percent of the time, said Humphrey.
He had to find a supplier for the material and a manufacturer for the needles.
Using the internet, and with help from the Canadian embassy, he found a manufacturer in China.
He field-tested the needles in barns at Concord Colony Farms near Winnipeg, and a Smithfield Farms operation in North Carolina.
Humphrey found the needle needed a stronger hub and worked with his manufacturer to develop one.
His second round of field tests concluded in mid-July at the North Carolina operation.
“We now have a viable product. It’s ready to go to market,” he said.
But because of the cost of the metal alloy, Humphrey has to mass-produce to make them affordable for producers.
To develop the needle to this point, Humphrey left his job, cashed in his savings, and invested everything he and his young family have.
He traveled to Iowa four times, and twice to North Carolina and China.
He has patents pending in Canada and the United States, and has starting working on the European patent process.
Humphrey is confident the needles will sell, but he’s not willing to risk covering production costs without firm orders from distributors.
“I’m not a very big risk-taker,” he said.