Ag and energy | Efforts taken to keep all field equipment clean
EDMONTON — The discovery of clubroot changed the way farmers, fieldmen and the energy industry look at cropland.
A farmer pulling out of a muddy field with the wheels tossing clumps of mud onto the gravel road may be spreading clubroot to everyone driving over the clumps of mud.
A custom sprayer operator racing from field to field during the busy spraying season may unknowingly be tracking clubroot between customers.
“Clubroot is out there. It is part of what we deal with,” Paul Muyers, an Edmonton area crop consultant with Solid Ground Solutions, told the International Clubroot Workshop held in Edmonton last week.
Read Also
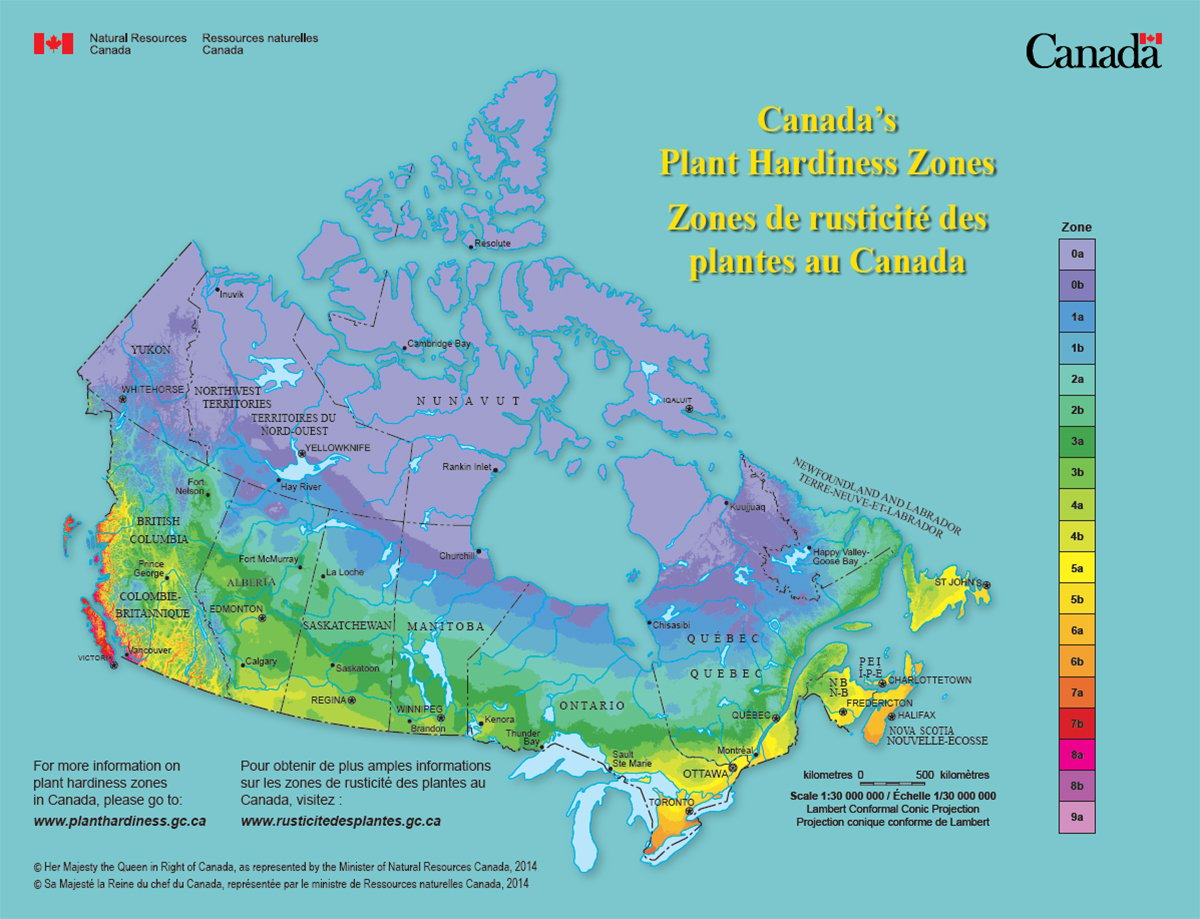
Canada’s plant hardiness zones receive update
The latest update to Canada’s plant hardiness zones and plant hardiness maps was released this summer.
“My farmers assume they have the disease and so do their neighbour.… They will not lose their mind that they have clubroot.”
Instead they need to control what they can by using clubroot resistant varieties, knocking off the larger clumps of soil and washing excessively dirty machinery, he said.
However, washing a vehicle after leaving each field may not be realistic in the busy seeding, spraying and harvest season, said Muyers, who sends pictures of his cleaned vehicles to farmers as a way of showing he is doing his due diligence.
Andrea Bullinger, a soil scientist with EnCana, a North American energy company, said clubroot has changed the way they operate in agricultural areas.
She said their style of natural gas development is to drill a well in eight hours. They want to get in, drill the well and quickly move on to the next well, hoping to drill three wells a day.
When clubroot started to appear, farmers began asking the company to soil sample for clubroot before it entered and ensure that all the equipment was washed before entering the fields.
“There was a real potential for reduction in our development. We needed to respond rapidly,” said Bullinger.
“By the end of 2007, 50 percent of land owners were asking what was our plans. Up to 25 percent were demanding we were washing and disinfecting our equipment.
“The cost of washing and disinfection of equipment for the construction of one coal bed methane well was estimated at $43,00 per well and used 112,000 litres of water.”
Bullinger estimated that the cost of washing all the equipment between fields in all of its drilling and pipeline operations would cost $47 million a year.
“The additional costs and water use would make the play unprofitable, but it didn’t make the issues any less important,” she said.
Bullinger said the company established a protocol that was practical and reasonable. All machinery is cleaned by hand between fields and washing equipment is now considered part of regular maintenance. Contractors who arrive on site with dirty equipment are sent back at the supplier’s expense.
“We take pictures and document them. You only have to do it once or twice before they quit sending dirty equipment.”
Drilling crews on land that is known to have clubroot follow special mitigation plans set out by the agricultural fieldman or the landowner, she said.
The company trained 15,000 people in six months on the seriousness of clubroot and how to reduce its spread.
Shannon Leggo of ATCO Electric said the company has developed best management practices to reduce the spread of clubroot and other diseases when crossing fields.
Leggo said it does “appropriate levels of cleaning” that can be dictated by the landowner, the fieldman or the company’s own rules.
Depending on the area, it will use mats to prevent driving on the fields, have air compressor stations for cleaning the soil and set up wash and disinfection stations.
It also has log books that include receipts for washing equipment as one more way to assure landowners they are trying to eliminate the spread of clubroot and other soil borne diseases or weeds.