VANCOUVER – Food companies in British Columbia are facing additional costs and red tape-induced headaches caused by new U.S. regulations aimed at preventing terrorists from tampering with imported food.
The new regulations include the Customs-Trade Partnership Against Terrorism, or C-TPAT, meant to reduce inspection time for imported goods, and a U.S. Food and Drug Administration rule that takes effect Dec. 12, which is designed to reduce terrorists’ ability to contaminate U.S.-bound food.
The policies require exporters to register with U.S. authorities and, in many cases, upgrade their record-keeping and security procedures.
Read Also
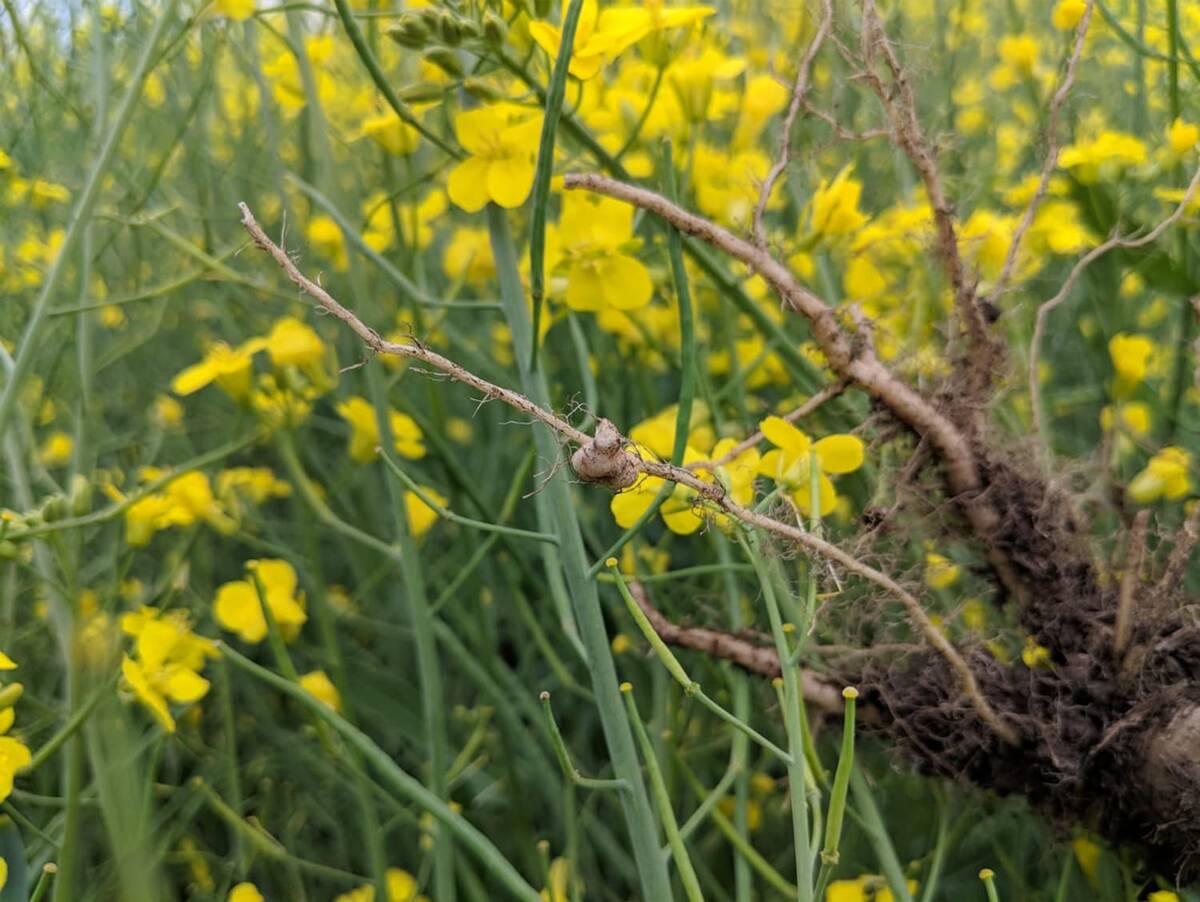
Going beyond “Resistant” on crop seed labels
Variety resistance is getting more specific on crop disease pathogens, but that information must be conveyed in a way that actually helps producers make rotation decisions.
Registration under the FDA rule is a one-time procedure for processing plants, packing facilities and warehouses handling product shipped into the United States. Farms, restaurants and retailers are exempt, but the rule is projected to affect about 205,000 businesses globally and incur first-year implementation costs of $435 million.
Most B.C. companies don’t mind registering with U.S. authorities, but object to the greater paperwork and notice of shipments they must give after Dec. 12.
Brian Tieszen, president of Richmond-based Sun Rich Fresh Foods Inc., estimated the new regulations will increase Sun Rich’s paperwork by about five percent.
Because the proposal requires that companies notify U.S. authorities of shipments by noon the day before arrival at the border, Sun Rich also faces a significant decrease in the shelf life of its U.S.-bound shipments of fresh fruit.
Sun Fresh processes 60 million pounds of fruit each year and ships 80 percent of the production at its Richmond and Toronto plants into the U.S.
“We would welcome any reduction in the notification time,” Tieszen said.
Brent Shantz, logistics manager for B.C. Hot House Foods Inc. in Surrey, is equally adamant. He said B.C. Hot House would probably reassess its packing operations in Canada if the final regulations don’t allow for same-day notification of shipments.
“We would probably end up having to move our distribution into the U.S.,” he said.
“Thirty-six hours gets us all the way down to L.A.”
An FDA spokesperson said last week changes to the notification period are pending. U.S. Customs and Border Protection agreed in May to standardize its import requirements with those of the FDA, and last month authorized a notice period, which it said would require no more than one hour for imports by truck and four hours by air and courier.
The FDA expects to release a final version of its regulations in October, two months before the implementation date.
Meanwhile, the C-TPAT regulations are prompting businesses to upgrade their security systems and protocols.
Langley-based Driediger Farms Ltd. ships about 45 percent of its berry production to the U.S. and employs 100 people directly and another 100 people on contract at peak season.
Co-owner Rhonda Driediger said the business bought a security camera in response to C-TPAT regulations but it was something it would have done eventually anyway.
“It’s an expense, yes, but the camera system is beneficial,” she said. “We’re going to have to look at these things in the future anyway, so we might as well do it now.”
The Original Cakerie Ltd., a Delta producer of frozen desserts supplying food service and retail outlets across North America, also had to increase its security measures to comply with the new regulations.
Steve Rutherford, manager of warehousing and distribution, termed the upgrade a “big expense.”
The Cakerie installed a card-access system and parts of the plant now have restricted access. Rutherford expects the company will eventually have to install gates.
“We have access to a relatively large chunk of the population,” he said. “(U.S. authorities) want to make sure their food supply is secure.”
The FDA said a typical food-borne illness such as salmonella can cost the U.S. economy between $19,000 and $35,000 per person per year.
It believes registering food producers will prevent and shorten outbreaks. But it added the probability of a food-borne terrorist attack, and the effectiveness of the FDA rule are impossible to determine.
“FDA is unable to quantify the benefits of registration arising from preventing or lessening the impact of a food-borne outbreak,” stated an FDA analysis released this spring.
Peter Mitham writes for Business in Vancouver.