Hot water | Dairy producers using solar system find savings in less than seven years, says company official
WOODSTOCK, Ont. — Dairy farmers who heat hot water with electricity can pay for a solar system in less than seven years.
That’s been the experience of John Rood and his sons, who operate Zolarayz, a solar thermal installation and maintenance business near Woodstock.
Rood said the dairy side of his solar thermal business has been particularly busy over the past two years.
“These systems will usually pay for themselves in 60 to 70 months,” he said.
“Some are milking twice a day and some are milking three times a day.… All of a sudden they’re up to 240 gallons of hot water a day. That’s not uncommon.”
Read Also
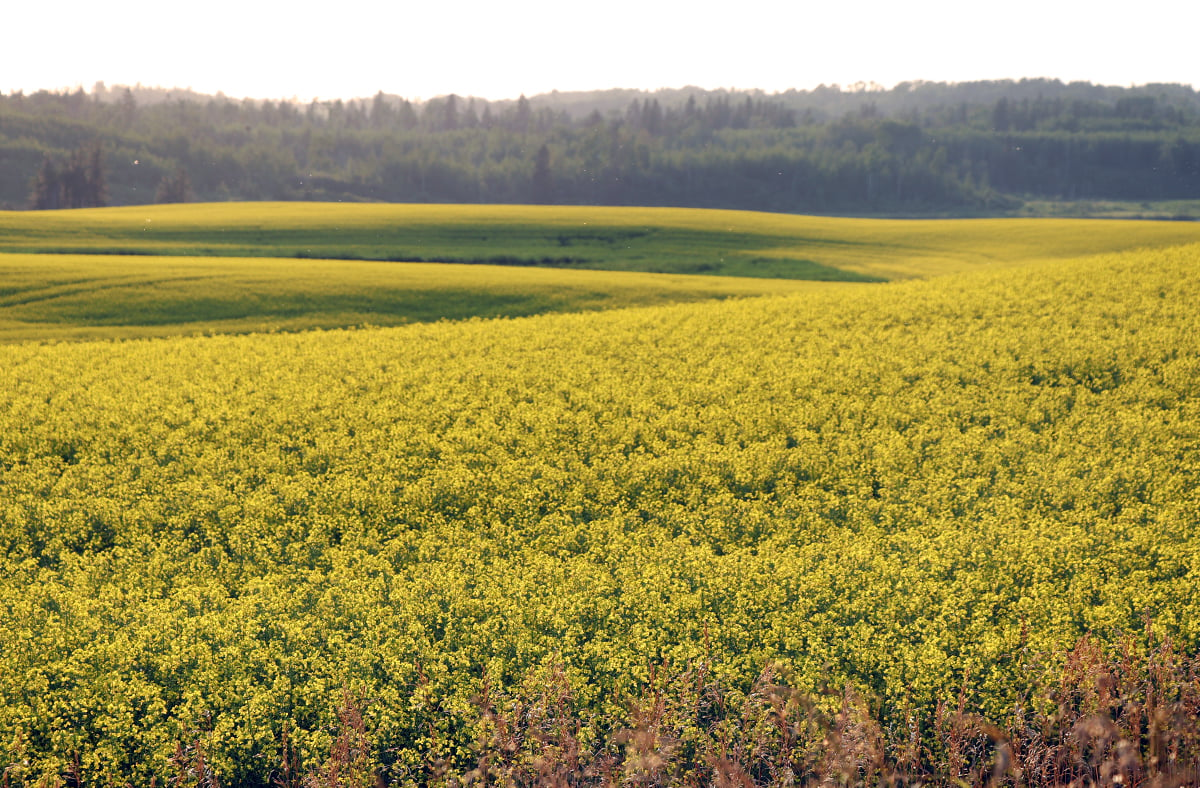
Agriculture ministers agree to AgriStability changes
federal government proposed several months ago to increase the compensation rate from 80 to 90 per cent and double the maximum payment from $3 million to $6 million
Rood said the payback is based on pure economics: no subsidies are involved.
“I don’t think it’s really healthy to build a business on subsidies, in my perspective anyway.”
Suni Ball of Enerworks Inc. in Woodstock agreed, but neither he nor Rood would complain if Natural Resources Canada was to reinstate its incentive program for solar thermal, which paid up to 30 percent of the cost for installations.
Enerworks designs and assembles solar thermal systems, but a lot of its sales are to U.S. customers. The U.S. government offers a 30 percent tax credit and many states also offer incentives.
Ball sees sense in this bottom-up approach to energy because it offsets reliance on traditional forms of energy rather than spending tax dollars to build additional natural gas, coal or nuclear power plants to meet peak electrical loads. In addition, fossil fuel that would otherwise be exploited are left for a future generation.
Glazed solar collectors lie at the heart of Enerworks’ solar thermal systems. The evacuated tubes are particularly efficient.
Flat glass systems are less expensive and are used when less than optimum efficiency is good enough.
Enerworks’ evacuated tubes absorb 95 percent of the sun’s light. The energy is collected as heat in the copper core and transferred to a solution so it can be circulated to where it’s needed.
Almost none of the heat can escape from the tubes because of the insulation of the absolute vacuum. The outer glass remains cool to the touch even if the core temperature of a tube is extreme.
Ball said Enerworks uses German-designed tubes with a single glass construction. Competing collectors often use a double glass construction that is less effective because the sun’s rays must pass through two layers of glass.
A solar glycol solution is used to transfer the heat to where it’s needed. He said evacuated tube systems operate from 50 to 90 C.
Heat exchange systems in dairy barns preheat the water used for washing. It’s then transferred to the regular water heater, which may or may not fire up, depending on the temperature of the water being delivered.
Radiated floor systems are often the choice for space heating.
Enerworks installed a large solar thermal system at Oxford Gardens, a large retirement home in Woodstock. The system is backed up with natural gas.
It uses solar thermal to warm Oxford Gardens during the cold months, but when outdoor temperatures rise it provides energy-efficient cooling.
“This technology was discovered more than 100 years ago. It used to be the primary way refrigeration was done,” Ball said.
Ball said the system is more efficient than compression refrigeration systems, although both work by “removing heat” rather than “adding cold.”
Heat from the solar thermal array on the Oxford Gardens rooftop drives the chiller by boiling the glycol in vacuum conditions at 7 C.
Two heat exchange systems circulate through the cool vapours rising from the glycol.
One cools the air coming in from the building to 14 C. The other leads to a cooling tower where an evaporation system is used to extract the heat.
“Essentially you’re using a 400 watt motor to get 105,000 watts of cooling power,” Ball said.
Rood and Enerworks are currently consulting with a mushroom producer interested in providing cooling power for his growing facility.
However, instead of using solar thermal as the energy source, the idea is to draw heat from the process used to transform spent mushroom substrate into charcoal.
Ball said thermal systems, whether used for heating or cooling, don’t necessarily need to rely directly on the sun as the energy source.