Building is finished on world’s largest cricket rearing facility and testing begins for the largely automated insect farm
About four-billion crickets will soon be moved into a new facility in London, Ont.
Aspire and construction partner Ellisdon finished building the project in May and are now installing and testing the systems so they can begin commercial production in a few months.
The building took 18 months to complete, with some delays from the COVID-19 pandemic.
Scott Chatterson, construction manager at Ellisdon, who managed the construction of Aspire cricket facility, said Ellisdon “thrives on these kinds of jobs.”
“We like taking on new stuff. Things that haven’t been done before. Things that are difficult and challenging, so we were super excited to be part of the process.”
Read Also
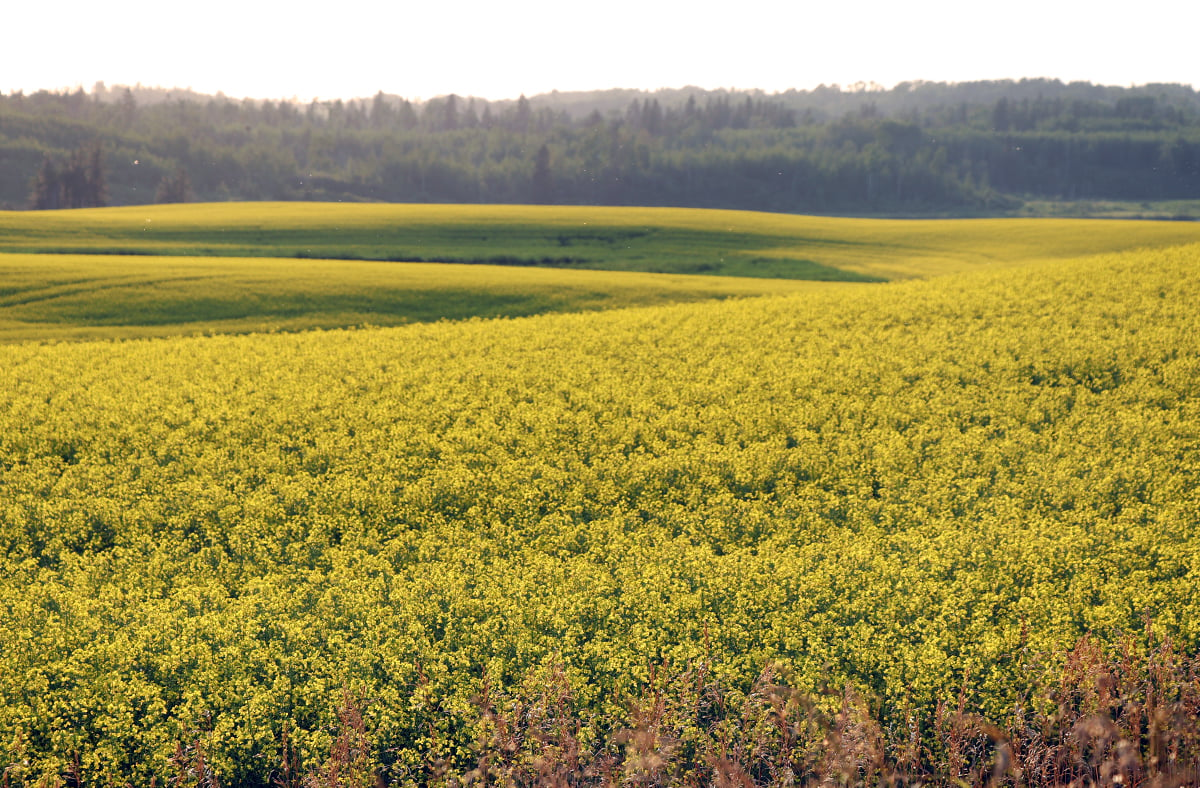
Agriculture ministers agree to AgriStability changes
federal government proposed several months ago to increase the compensation rate from 80 to 90 per cent and double the maximum payment from $3 million to $6 million
The project is the first of its kind. Ellisdon took a team approach because the design was still being developed as construction started.
“We were trying to learn the parameters of what we were trying to design to, so it really came down to a team effort with our mechanical subcontractor, electrical subcontractor, our engineers and Aspires people.”
The automatic storage and retrieval rack in normal manufacturing plants don’t deal with living creatures, so a big challenge was making sure oxygen was filling the room and making sure the temperature was properly maintained.
Humidity control was also needed, along with knowing how much water was needed and how much got evaporated, because crickets like it at 32 C. They also had to equip it with sprinklers in the event the racks caught fire.
“We’ve got two, 80,000 tonne HVAC units on the roof that are supplying air into the (storage and retrieval rack) and the ductwork coming out of them is big enough to drive a small car through.”
Mohammed Ashour, chief executive officer of Aspire, said London was chosen as the location for many reasons.
“We had to contemplate a number of criteria,” said Ashour. “This is a first of its kind construction project that’s really never been done before anywhere in the world.”
“We wanted to be in a city that had a business environment that was very friendly to embrace such an undertaking, while at the same time having a level of rolling up your sleeves mentality that allows us to get things done.”
Aspire received a $10-million grant from the federal government that went into the construction of the project, along with funding from Next Generation Manufacturing Supercluster, created to help advanced manufacturing capabilities in Canada.
The facility is expected to produce about 10,000 tonnes of edible cricket product annually, which is a substantial source of protein for humans and pets, while also producing the same weight in cricket feces that will be used as fertilizer.