NIVERVILLE, Man. – Al Sawatzky watches while two dead feeder pigs are dumped from a front-end loader into an opening at the top of a long steel chamber.
A worker then empties four garbage bags of wood shavings into the chamber before closing three metal doors over the opening.
Sawatzky said that in about 14 days the pigs, weighing about 450 pounds in total, will be rendered into compost, but “we have done it even quicker than that,” he added.
Sawatzky works for Puratone, a company in Niverville, Man., best known for hog production and livestock feed manufacturing. The equipment he was helping demonstrate is called the Biovator, a composter that Puratone engineers designed to compost dead hogs.
Read Also
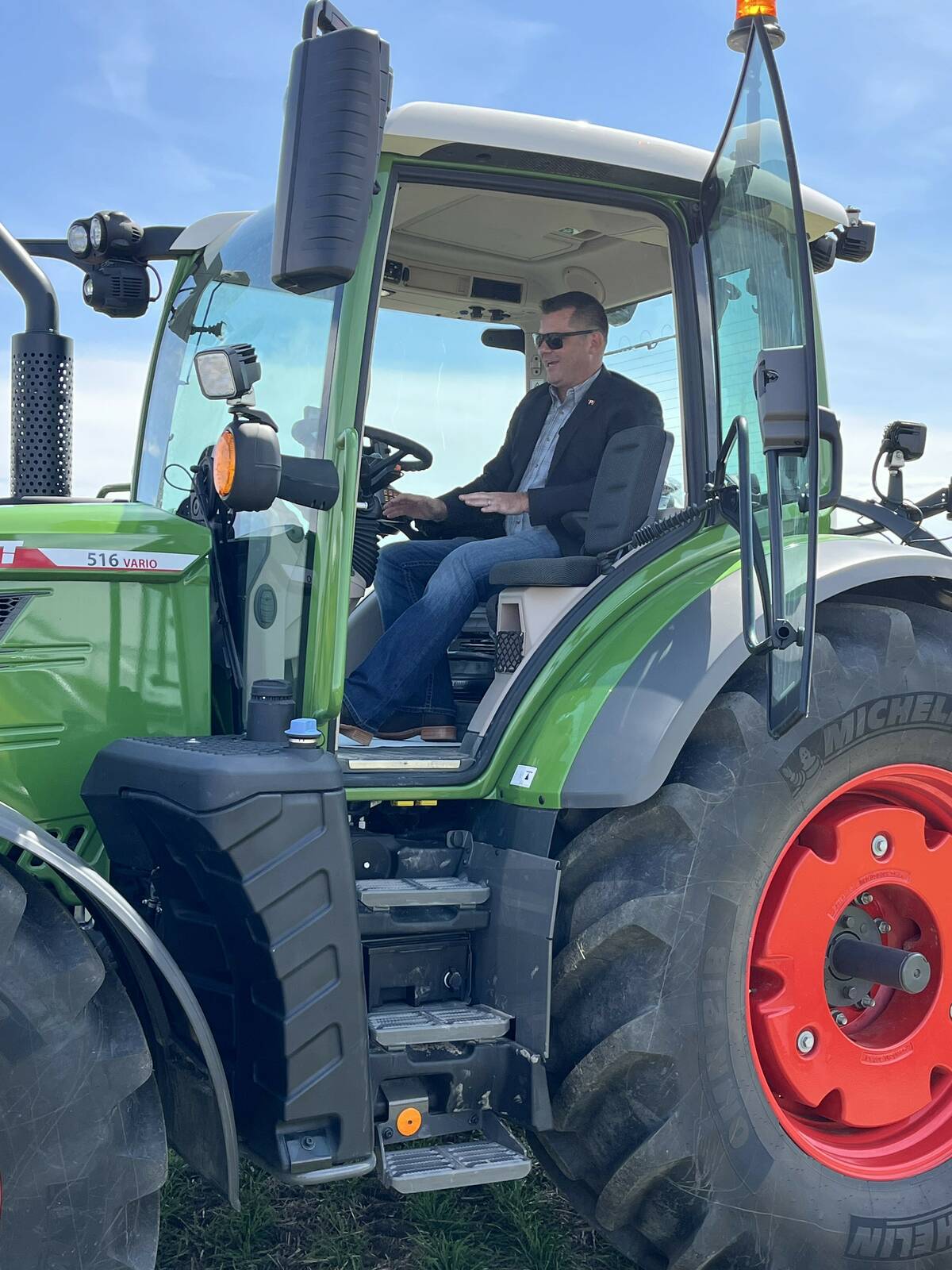
Farming Smarter receives financial boost from Alberta government for potato research
Farming Smarter near Lethbridge got a boost to its research equipment, thanks to the Alberta government’s increase in funding for research associations.
“Basically what we’re doing is helping Mother Nature move along a little quicker,” he said.
Puratone is marketing the equipment as an alternative to traditional methods for disposing of dead hogs. The company promotes it as a cost-efficient and environmentally sound solution that exceeds provincial regulations.
The composter has five standard features:
- The steel chamber is a long, round drum that is four feet in diameter and 30 feet long. The chamber is coated on the outside with sprayed-on foam insulation to help keep in heat generated during composting.
- Three doors are mounted at one end of the chamber for loading dead hogs and wood shavings. An opening at the top of the chamber is used to check on composting progress. Composted material is removed through another hatch.
- The chamber is mounted on a steel skid with four heavy-duty rollers.
- A one-horsepower motor mounted on one end of the skid drives a gear box, heavy-duty bearing, sprocket and chain that turn the steel chamber on the rollers. Sawatzky said the vessel and its contents will turn slowly, 16 minutes per revolution. The motor is usually turned on twice a day for an hour at a time, which is adequate for composting. A timer can be installed to regulate the motor.
- Steel paddles or fins attached to the inside of the chamber carry the composting material from one end of the chamber to the other.
Sawatzky said the Biovator costs about $30,000, which Puratone considers comparable to, or more affordable than other options.
The company maintains that the Biovator reduces odour and disease-causing organisms because dead animals are disposed of quickly and heat from the composting process tends to kill most pathogens.
Because the equipment is fully enclosed, leaching and problems with wildlife, insects and rodents are avoided.
The composter can handle an average of 2,000 lb. of dead hogs a week or 100,000 lb. a year.
In the winter, hot, moist air from hog barn exhaust fans can be piped to the Biovator through a duct to keep conditions suitable for composting.
Sawatzky said company engineers are considering the idea of designing a larger version that could accommodate dead cattle.
The Biovator demonstration occurred during the national Living With Livestock conference held last week in Manitoba.
Producers, researchers and government officials attended the three-day conference to talk about environmental challenges facing livestock production and innovative solutions available or under development to address those challenges.