The agri-business landscape in the western Manitoba village of Austin expands with the arrival of textile processing.
Glacier FarmMedia – The western Manitoba village of Austin has a new facet in its agri-business landscape: textile processing.
The Austin Woollen Mill, owned and operated by Bryan and Lynda Driedger, held a grand opening earlier this spring. Visitors were introduced to the steps of wool processing as they toured the new facility.
The facility could bring value-added capacity to the sheep sector in Manitoba, which tends to focus more on meat than on wool production.
Read Also
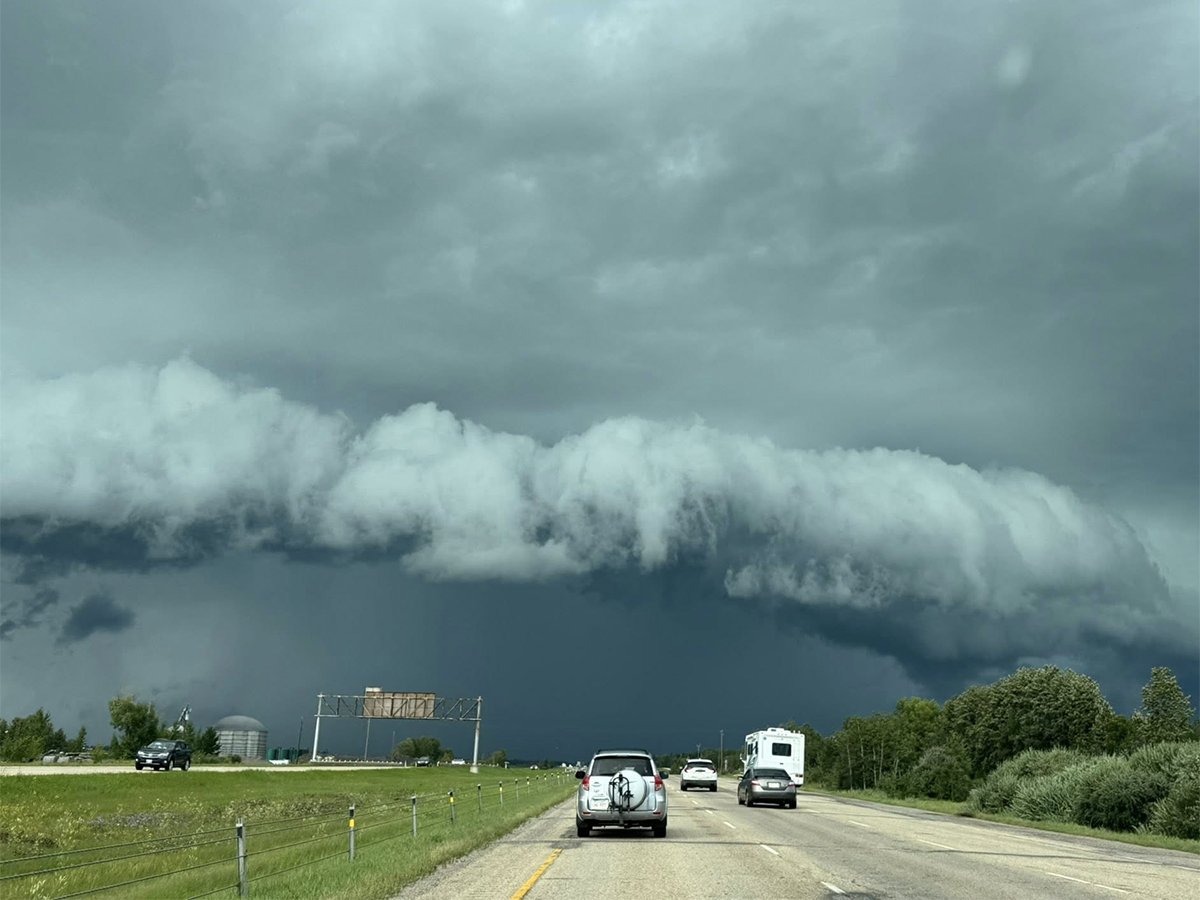
Above average temperatures expected
July was a cooler than average month right across the Prairies, with most places coming in just slightly below average.
Lack of processing has been a big obstacle for Canadian wool in general, Canadian Wool Council chief executive officer Matthew Rowe noted in a 2022 interview. Better processing and markets to support the wool value chain were among items in the wool council’s 2021-26 Carpet Plan, which set out the group’s strategic goals.
Manitoba once had several large wool mills. Now, other than the new Austin facility, there is only one: the Long Way Homestead, a family-owned and operated sheep farm and mill at Ste-Geneviève.
The facility in Austin is not connected to any one farm. Instead, the owners hope to create a business in which many Manitoba sheep farmers can sell wool or bring in raw fibre for processing.
The journey to opening a wool plant has been a learning curve for the couple.
“We actually knew hardly anything in the beginning,” Lynda Driedger said.
Their interest was sparked during a 2010 visit to Prince Edward Island. Upon their return to the Prairies, however, other time commitments reasserted themselves, and any ideas of getting into the business stalled.
Although put to the back burner, the thought of their own local wool mill never died. Eventually, the couple figured the time was right to break into the sector and started the process of establishing their mill.
The closure of a previous business on their current site gave them a landbase. The Driedgers decided the building, located within Austin’s town limits, could be renovated and expanded to suit their equipment, while also leaving room for a storefront to sell finished wool and other products.
Then they figured out where to buy and how to operate the necessary machinery. Equipment was ordered through Belfast Mini Mills in P.E.I., but there was an 18-month wait. During that time, Bryan Driedger worked on renovations and additions to the building and, once the equipment arrived, a technician from the company taught them how to run it.
There are a lot of machines required to make raw wool into a finished product. It must be skirted to remove debris, washed in hot water and dried. It goes through a picking machine to break up the locks, followed by a fibre separator.
Then it is ready for the carding machine, followed by the pin drafter, the spinner (which puts thread onto bobbins) and the plyer (which combines threads together). Then it’s on to the cone winder to transfer thread from a bobbin onto a cone, followed by a steamer and a skein winder. Dyeing may take place at this stage or earlier in the process.
When there’s a finished product to sell, marketing is required.
The mill’s opening and first official for-sale products drew nearly 300 people in April. The Manitoba Sheep Association attended with a display of different sheep breeds raised in Manitoba and the varieties of wool available.