When you think of materials used to make a car, you might name steel, plastic, rubber and even computer parts.
You can add flax to that list.
Durafibre, Inc., a joint venture of Cargill Ltd., the Saskatchewan Agri-Food Equity Fund and Sask-Can Fibre Inc., has joined forces with Michigan auto parts manufacturer Cambridge
Industries.
The companies have found a way to use long fibres in flax straw to make moulded auto parts.
Cambridge uses a blend of flax fibres and plastic, called flax polypropylene, to create a mouldable material to form the rear shelf panel of the 2000 Chevrolet Impala. This material is comparable to fibreglass.
Read Also
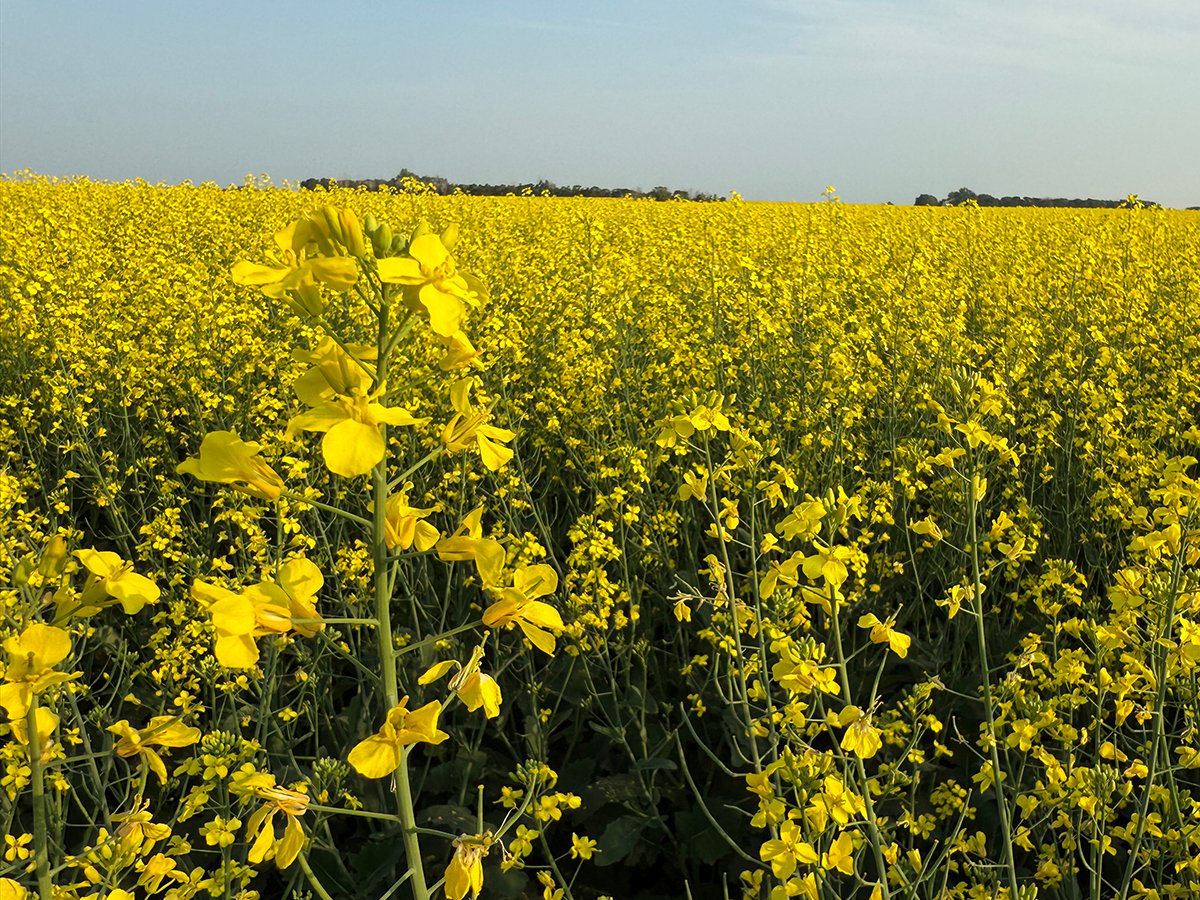
Canola council cuts field agronomy team
The Canola Council of Canada is cutting its agronomy team as part of a “refreshed strategic framework.”
Although the manufacturing process started in June, the companies spent five years developing the technology to extract the long fibres.
“This is like a miracle,” said Durafibre manager Barb Isman.
“We took a raw product people didn’t understand and a process that wasn’t invented yet to a market we’ve never dealt with.”
The Durafibre plant in Canora, Sask., buys flax straw that farmers usually burn. The strong, wiry fibres can’t be tilled into the soil and there aren’t many alternative uses.
The company will go into a field, bale the straw and haul it to the plant, where the long fibres will be extracted, cleaned, and sent to the Cambridge factory. The remaining straw will be refined into cellulose fibre that can replace wood flour in construction materials.
The fibres will be blended with plastic and formed into a mat that can be made into interior car parts.
Farmers who sold their flax this fall received about $5 a tonne, and Isman said a spring program through Durafibre would pay about $10 a tonne for the straw.
Fibreglass alternative
She said the flax product is not as strong as fibreglass, but it is an alternative because it is lighter, cheaper to produce and recyclable. It also makes good use of material that is usually wasted.
“The very thing that makes it (flax straw) annoying to the farmer, its strength, makes it a good natural reinforcement,” Isman said.
She estimated the plant would be able to use 40,000 tonnes of straw per year within the next five years in automotive applications. Durafibre has also sold flax straw for use in the pulp and paper industry for currency.
The companies have invested $4 million in the project. The Canora plant has 20 employees, and Isman said there is the capacity to double that number as the business grows.
The companies are experimenting with different flax varieties and harvesting methods. Even the kind of combine used can make a difference in the color, strength, and overall consistency of the finished product, said Isman.
She estimated it will take at least five years to achieve consistency in the natural fibres.
“We know it has an impact, we just don’t know what it is yet. This is a brand new segment for agriculture.”