A short-lived period of fat profits has turned into a scramble for a few crumbs of profit for the Canadian beef packing industry.
Tight margins have forced federal plants to run well below capacity for fed cattle, but cow kills are up substantially, said Anne Dunford, a market analyst at Canfax.
“Just from the numbers perspective we are not utilizing what we have,” she said.
Feedlots have been able to avoid a backup by exporting about 18,000 head each week to the United States.
Read Also
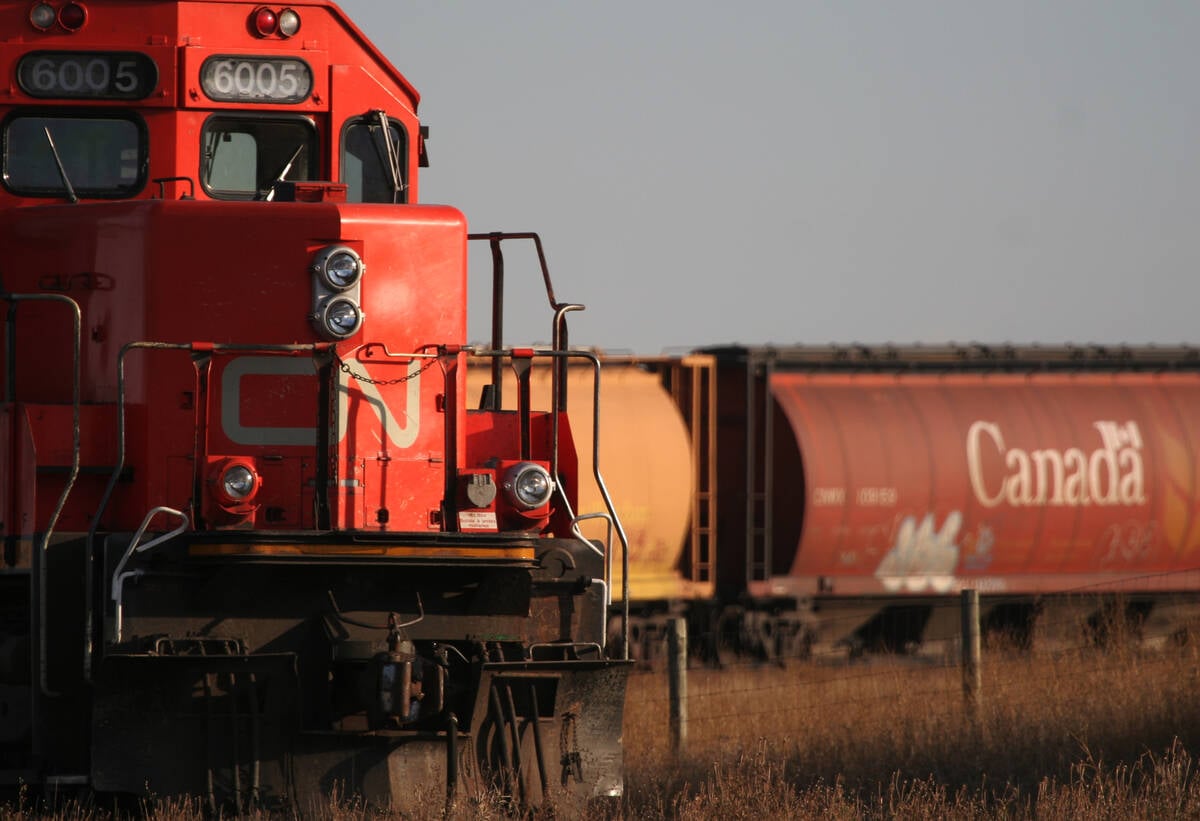
Canada-U.S. trade relationship called complex
Trade issues existed long before U.S. president Donald Trump and his on-again, off-again tariffs came along, said panelists at a policy summit last month.
Packers don’t post plant profits, but analysts know margins have been tight in both countries, she said.
“Right now we are watching the numbers and the data. We don’t have all the answers,” Dunford said.
Kill rates could step up as summer nears and beef demand improves.
“It’s an ever moving phenomenon. You always get exits and entries happening in the industry and it is hard to say where we are,” she said.
Kevin Grier, a meat and livestock market analyst with the George Morris Centre, said in the Canadian Cattle Buyer newsletter that Canadian packer margins were poor at the end of 2005 and the first month of 2006. In response, packers cut fed kills while boosting the more profitable cow kill.
The main Canadian packers are operating 10,000 below capacity. Packers have often slowed their kill pace to push boxed prices higher and cattle costs lower, but usually it is a short-term tactic.
If this is a longer-term strategy in both Canada and the U.S., it will hurt cattle prices in the normally stronger spring market.
Conference Board of Canada analyst Michael Burt noted the dismal situation in his 2006 winter report on the food processing industry.
The average profit margin in the food processing complex is between one and three percent.
Packer profits dropped when beef prices fell last year but cattle prices increased after the border opened in July. Unexpectedly high energy costs added to the pressure.
“Their output prices are falling and their input costs are going up so that has really squeezed the margins for the beef processors,” Burt said.
With the major packers operating at less than capacity, it calls into question the need for additional Canadian beef processing capacity.
“If you want to get the most value out of our cattle, you should process them here rather than export them,” he said in an interview, but added producers are free to export to U.S. slaughter plants if it makes financial sense.
“In the long run, if we wanted to insulate ourselves from another incident like the BSE crisis, it would be wise to line up processing capacity with herd size, but it is a moving target.”
The stronger Canadian dollar has also hurt Canadian packers. They are forced to more closely align operating costs, particularly labour, with the U.S., said a recent National Beef Industry Development Fund report produced by George Morris Centre, Informa Economics and Kurt Klein at the University of Lethbridge.
“During the 1990s packers were very low cost relative to the U.S., largely due to the cheap dollar. As of 2006, this low cost dollar shield advantage has largely eroded,” said the report.
“Clearly the appreciation … will force Canadian packers to improve their competitive position, or risk failure in the market.”
But the problems packers face may be even more fundamental.
U.S. plants have been faltering for two years so new strategies focused on managing capacity are needed.
This is a mature industry where large corporations use volume to make profits from narrow margins. Yet many of the big players are struggling.
Multinational corporations are reporting severe losses, said analyst Steve Kay in his report to the U.S. National Meat Association annual meeting March 13.
Fed cattle processors may have lost as much as $700 million US in 2004 and 2005. Tyson Foods will lose $128 million in beef in its current quarter, meaning a loss in beef operations over three quarters of $205 million.
Nine U.S. plants have been closed to protect their parent companies.
Several of those operations might have survived had the U.S. not lost its export markets and the ability to kill Canadian cows, both events caused by BSE.
Kay predicts plant survival will depend on running close to 90 percent of capacity most of the year.
As the U.S. cow herd expands, plants should be able to recover somewhat if demand remains strong and key export markets like South Korea and Japan reopen to U.S. beef. But negotiations to restart trade show little progress.
Further, domestic retail demand improved every year from 1998 to 2004, but fell three to four percent in 2005. It has continued to slide in the first quarter of 2006, said Kay.
That probably cooled the enthusiasm of those wanting more packing plants for Canada following a two year struggle when BSE closed borders to trade. Many proposals have faced the reality of what it costs to go into the beef processing business.
“It is just a lot harder than they thought to put the cash together. I think they ran into roadblocks when it came to putting the financing together,” said Doug Price, a major shareholder of Rancher’s Beef set to open in May.