The first step toward building a producer owned packing plant should be a cautious one, says a beef industry consultant.
“To be realistic, you don’t want people to lose their money or their investments,” said Joan Perrin, brand manager for Atlantic Branded Beef Management Inc., based in Prince Edward Island.
She warns there is already plenty of slaughter capacity in Western Canada, compared to what is available in the Atlantic provinces. Further, there is no guarantee of loyalty among producers.
“Once the border opens, people will go where the dollar is,” she said.
Read Also
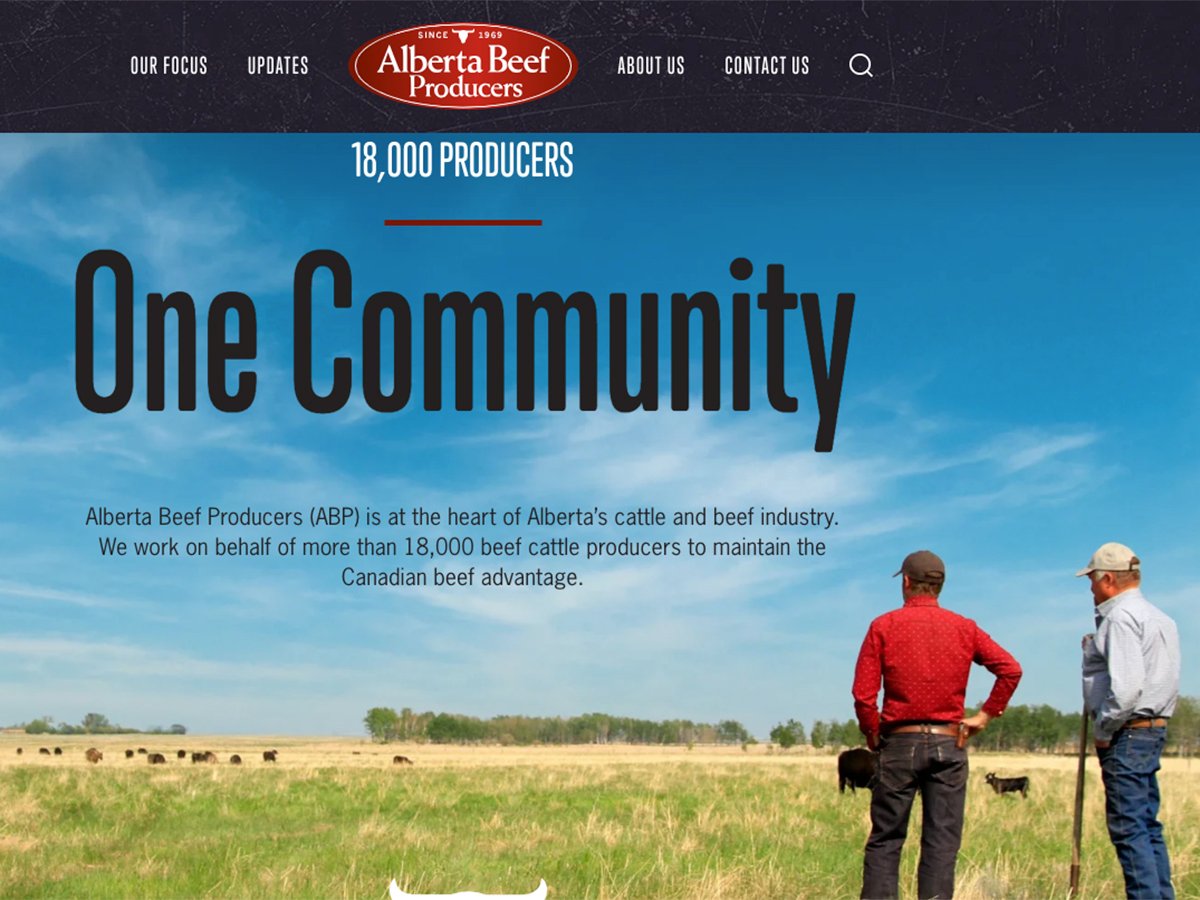
Alberta Beef Producers announces withdrawal from Canadian Cattle Association
Glacier FarmMedia – On August 12, 2025, the Alberta Beef Producers (ABP) announced their decision to withdraw their membership from…
Another question is the ongoing ability of producer-owned plants to compete with large multinational companies like Lakeside Packers or Cargill Foods, responsible for processing about three-quarters of Canada’s beef supply.
“They can double shift in the wink of an eye and put a small plant out of business,” she said.
The Maritime situation is somewhat different.
Producers there had already developed a regionally branded program called Atlantic Tender Beef Classic with a loyal customer base. The beef was sold through Atlantic Co-op, which operates 104 retail stores in the region.
The branded package was launched several years ago and was custom processed at a Maple Leaf Foods plant in New Brunswick. When the company decided to switch to pork production exclusively two years ago, farmers were forced to ship finished animals to Better Beef in Guelph, Ont., at an extra cost of $60 per head.
They decided a better alternative was building their own federally inspected beef plant in Prince Edward Island where 80 percent of Maritime cattle are finished.
Ownership is shared between Atlantic Co-op and a new generation co-operative owned by producers who bought shares in the plant and agreed to supply cattle on a regular basis.
More savings were achieved because the construction company owns the building and will lease it to the co-operative with an option to buy it outright after 20 years.
When the plant opens this September, it should handle 500 head per week and cattle must meet a list of product specifications to receive the Atlantic Beef brand.
While most of the co-operative’s ideas have proceeded smoothly, there were unexpected costs following the BSE crisis that were not budgeted in the original business plan, said Perrin.
Added costs include checking cattle’s teeth for proof of age and removing and disposing of beef byproducts and high risk materials.