DAWSON CREEK, B.C. Ñ For anybody who has ever worked in a hog barn, trying to stuff an unco-operative, 110 kilogram hog into a wooden crate to be weighed each week is the worst job.
It was sheer bull work, said Rocky Morrill, president of Peace Pork, which owns hog barns in the Peace River area of Alberta and British Columbia.
“To move a pig through a scale you are moving, with your knees or your body, a 220 pound (100 kg) pig into a box where it didn’t want to go,” said Morrill.
Read Also
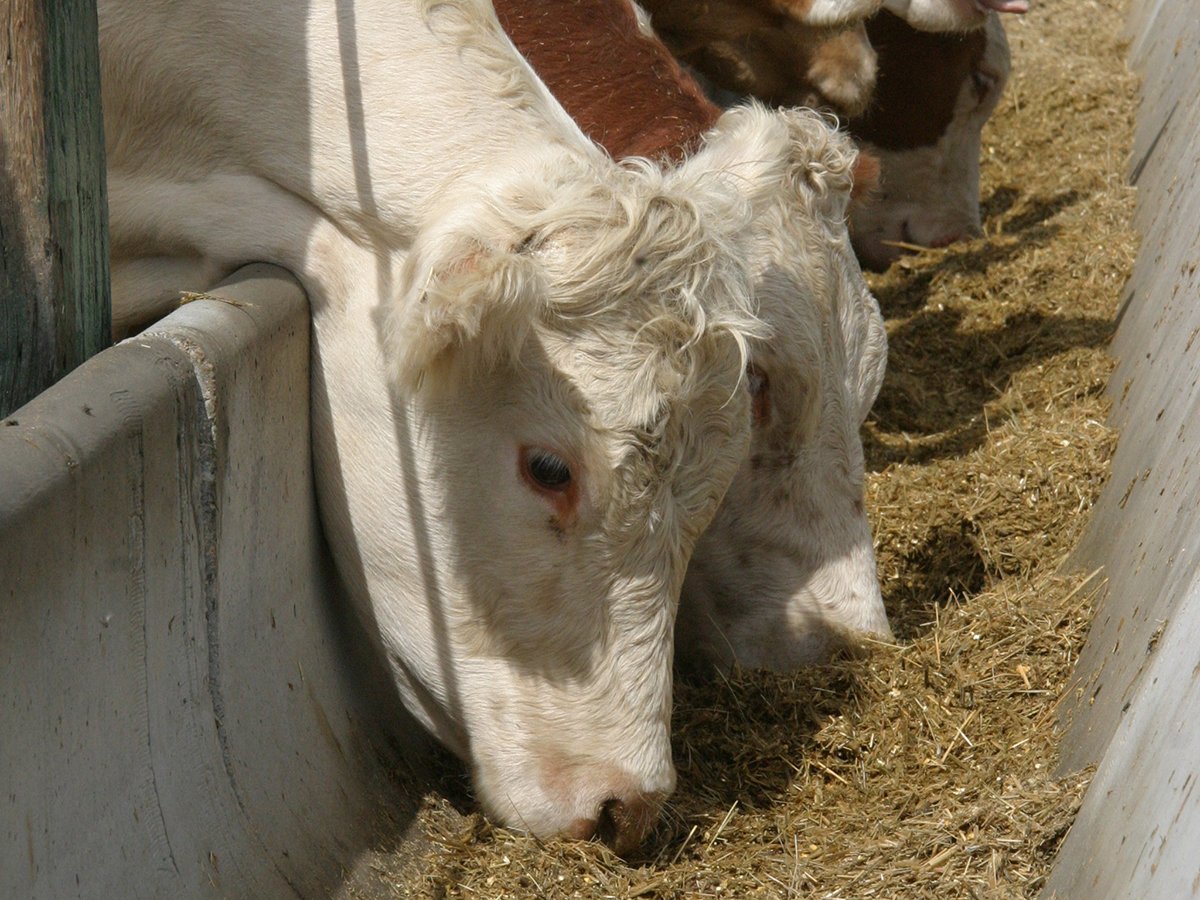
Alberta cattle loan guarantee program gets 50 per cent increase
Alberta government comes to aid of beef industry with 50 per cent increase to loan guarantee program to help producers.
“It was a very difficult task. It would take hours and it was very hard work.”
In an attempt to make life easier for the staff and to save money by not shipping underweight or overweight hogs to slaughter, Peace Pork converted all its finisher barns to include an automatic hog weighing system in 2003.
“We just went out and did it,” said Morrill from his Dawson Creek office.
The company spent $500,000 buying 50 of the automatic sorting scales, two for each barn, and switched the barn from small pens to group housing where hogs have free run of the barn.
Now, about 24,000 finished hogs in the company’s own barns and about 10,000 hogs at barns under contract to Peace Pork are weighed using the automatic weight scale each year.
“We would never go back to the old system,” said Morrill.
In the redesigned finisher barns, the barn is divided lengthwise in thirds with a wide centre alleyway and long rows of feeding, or food courts, along the outsides. The three sections are divided by a series of one-way gates that only allow the pigs to move from the feeding area to the open area.
When the pigs are small, they can easily move under the gates and go anywhere in the barn, but as they get larger they can only get into the food court area by gates near the automatic weigh scale. The feeding area is about 25 percent of the barn. As the hogs get closer to market weight, all the gates are closed except for the one through the weigh scale.
While there are several different types of scales on the market, those in the Peace Pork barns use an electric eye to activate a head gate operated by air compression. If the hog is not the desired weight it is sent back to the food area. If the hog is the correct finished weight, the mechanism changes the head gate and the hog is sent to another part of the barn while it waits to be loaded onto the truck.
Because the pigs are together as a group while they are raised, there are no problems with fighting when they are funnelled to the shipping area, Morrill said.
“It’s as simple as coming in the next day to have pigs that are ready to go.”
By weighing hogs by hand, a good manager could choose a couple of hogs from each pen and guess the average weight. Under that system 92 percent of the hogs shipped were in the correct target weight range required by the packer. The automatic sorter ensures 96-98 percent are the target weight, said Morrill.
For every pig not at the target weight there is a $10 loss in value. If five percent in an 8,000-head finishing barn are not within the target weight, that’s equal to $4,000 for each group of hogs in the barn, or $12,000 a year. With 8,000 hogs in a finishing barn, the deductions can add up quickly.
When Morrill first looked at the idea, he estimated the automatic weigh scales would pay for themselves in three years in labour savings and fewer deductions at the packing plant.
He thought there would be a 25 percent reduction in staff by eliminating the job of weighing the hogs. There are usually about four people working in two 8,000 head feeder barns. But because of holidays, weekend shifts and sick days, it’s impossible to work with only three staff members. Instead Morrill said staff have more time to do other jobs that weren’t getting done before.
“Labour is one of the biggest issues in the hog industry,” he said. Unlike other agriculture industries, women make up a large number of the staff in hog barns.
“I hope this is making a better work environment.”