Compressed gases are delivered to and used in agricultural operations every day across Canada. They may be used for heating, cutting, welding and even directly in food production by, for example, supplementing the carbon dioxide levels in greenhouses.
While some very large users will have semi-permanent bulk-storage or mini-bulk tanks installed that contain cryogenic (very cold) liquid gases, most operations will be using portable cylinders.
These cylinders may contain gases held as a liquid that that turns to a gas as it is used, either as a high-pressure compressed gas or as a gas dissolved into a liquid inside the cylinder. Surprisingly, most farmers and ranchers would have all three types of portable cylinders on the property, even if using only three of the most common gases.
Read Also
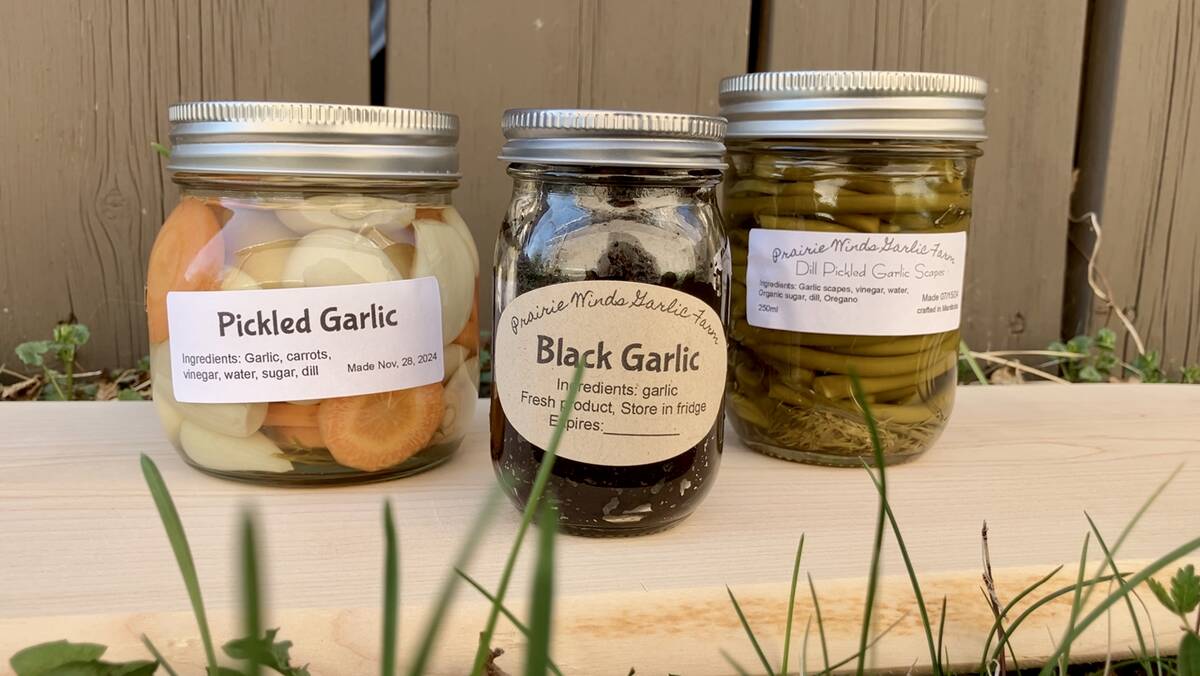
Growing garlic by the thousands in Manitoba
Grower holds a planting party day every fall as a crowd gathers to help put 28,000 plants, and sometimes more, into theground
Common gases
Most agricultural operations will be using propane for heating, acetylene for steel cutting and spot heating, and oxygen as a gas to increase the flame temperature for cutting, welding or brazing welding applications.
As well, various compressed gases or gas mixes such as argon and carbon dioxide or pure carbon dioxide or argon will be required if arc welding with gas-metal-arc (MIG) welding or gas-tungsten-arc (TIG).
Of these gases, propane and carbon dioxide are liquefied gases, argon and oxygen cylinders are highly compressed gases — typically from 2,200 to 4,500 pounds per sq. inch gauge pressure — and acetylene is dissolved into acetone in a specially constructed cylinder and produces gas at no more than 250 p.s.i.
One of the common misconceptions is that you can identify the gas in all cylinders by the exterior colour. While this may be true for certain gas supplier’s product lines, this is not true across the industry. When you receive a new cylinder, you should verify it is what you ordered by the affixed label.
In all cases, the higher pressure of the cylinder must be reduced to a working pressure and the flow must controlled. These functions are accomplished using a pressure reducing regulator.
Each gas generally has a specific fitting type that cannot be accidentally interchanged with another type, and these are specified by the Compressed Gas Association. For example, an oxygen regulator cannot be inadvertently installed on an argon cylinder.
Cylinder protection
Compressed gas cylinders are vulnerable to impacts, over-heating and fires, corrosion, and electrical arcs. The cylinder design does offer some measure of protection.
The vulnerable valve and valve stem at the top of many cylinders are protected from impacts either by a removable or a permanent impact protection, such as a metal cap or collar. Some smaller cylinders do not have this protection, and special care must be taken to protect the valve from impacts.
On a cylinder with a removable valve protection cap, this device must be properly installed before moving the cylinder and when it is not in use. Do not remove this cap until the cylinder is secured and ready for use.
These caps are designed to be installed and removed by hand so do not use a pry-bar or hammer on them and do not lubricate the threads with oil or grease. If the cap is frozen, use warm water rather than boiling water or an open flame to thaw the threads.
Cylinders also have a protection system to prevent excessive pressure build-up if the cylinder is overheated, such as in a structure fire. For example, acetylene cylinders have fusible metal plugs that melt at around the temperature of boiling water.
Other cylinders, such as oxygen, carbon dioxide and argon, contain a burst disk that will rupture when the design pressure of the cylinder is exceeded. The purpose of these one-time use devices is to bleed off excessive gas pressure to prevent a catastrophic cylinder failure, but you cannot assume that the cylinder is empty if it has been in a fire. In this case, firefighting experts must take charge of the situation.
High pressure gas cylinders are forged from a seamless ductile steel alloy. Lower pressure cylinders, such as acetylene and propane, are a welded steel shell design. The cylinders are painted in a durable epoxy coating.
Despite this, the cylinders can be vulnerable to accelerated corrosion if stored directly on the soil, in damp areas or in a corrosive environment such as in contact with fertilizers or road salt. These cylinders are routinely inspected and serviced by gas suppliers, but a low-use cylinder may sit in a shed or a barn for several years before it is emptied, and these can corrode in this time.
Compressed gas cylinders are vulnerable to electrical arcing, either because they are in contact with an electrical power circuit or they are near an arc welding operation. These cylinders should never be in electrical contact with a steel workbench where arc welding is occurring. An arc strike will weaken the cylinder wall and could cause the cylinder to explode.
Compressed gas cylinders should be shipped, stored and used in well-ventilated locations and away from easily ignited flammable materials such as straw or sawdust. They must not be stored in enclosed cabinets in buildings or on vehicles.
Cylinders should be securely supported when transported, stored or in use to prevent them from falling over or being otherwise damaged.
They should not be stored in temperature extremes. Do not store any compressed gas cylinder in a location that can exceed 52 C, and they should not be used at a temperature exceeding 50 C.
Very low temperatures can also be a problem for cylinders because the gauge pressure will drop. For example, at 0 C, an acetylene cylinder pressure will appear to be only about half full, while at -15 C it will have a pressure of only about a quarter of the original pressure when it was filled at room temperature.
Oxygen and fuel-gas cylinders must be stored at least six metres apart unless separated by a fire-resistant barrier as required by local fire code regulations, but a single set of oxygen and acetylene cylinders mounted on a cylinder cart or secured against a wall are considered to be in-use and not in storage.
The most common safety incidents with moving cylinders involves pinching fingers, dropping them on feet or straining muscles because of their weight and shape. Proper personal protective equipment such as gloves and safety boots should be worn when handling cylinders.
A properly designed gas cylinder cart is the best way to move cylinders, and they should never be rolled, dragged, banged together or lifted by the safety cap. On the farm with rough ground, a cart with a larger set of wheels and pneumatic tires is easier to move.
Shipping, storage and handling
Compressed gas cylinders should be shipped, stored and used in the upright position. This is especially important with acetylene cylinders so that the gas stays dissolved in the acetone solution. If the cylinder ends up on its side, it must be placed upright and not used for at least an hour.
Transport Canada regulations must be considered if cylinders are transported by vehicle. They must never be transported or stored in an enclosed van or automobile.
A future column will focus on the specific safety issues with the use of oxygen and acetylene.
Compressed gas cylinders can be dangerous and must be treated with respect. They must be returned to the distributor If they are leaking, have a stuck valve or are malfunctioning in any way.
More information about compressed gases safety can be obtained from your gas supplier or the Canadian Standards Association standard CSAW117.2-19 (Safety in welding, cutting, and allied processes).
Jim Galloway teaches welding technology at Conestoga College in Cambridge, Ont. He also volunteers on several CSA technical committees, including CSA W117.2 — Welding Safety.