If you think fuel prices are going down in the future, raise your hands.
Not many readers are likely to dent the headliners in their pickups with their hands flying up in answer to my question.
Every acre will cost farmers more in fuel this year unless they just bought a new machine that is more efficient and relies on computers.
But even if the equipment doesn’t have the latest in engineering, farmers can realize some of those savings.
A portion of what computers do to save on fuel, farmers can do themselves. For starters, farmers can run their engines at the factory-rated load speed.
Read Also
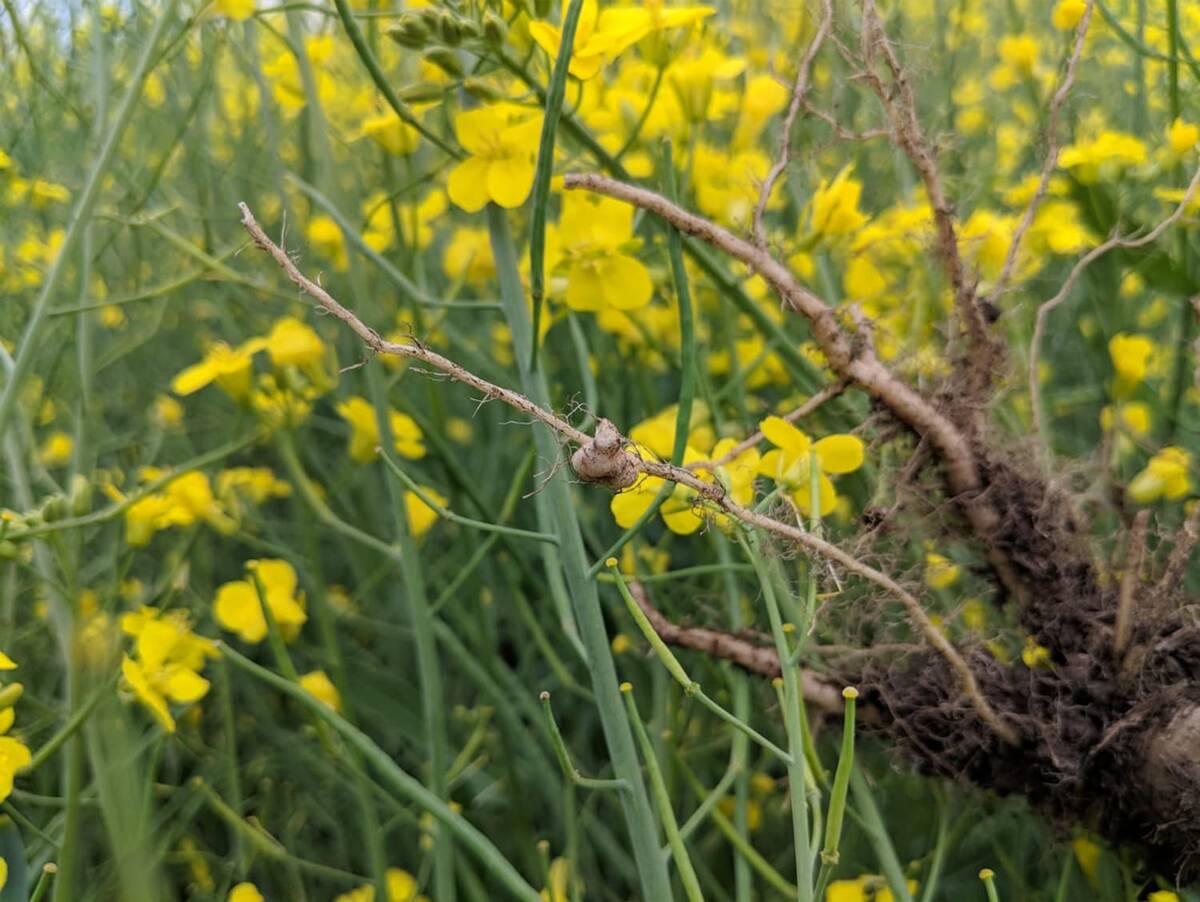
Going beyond “Resistant” on crop seed labels
Variety resistance is getting more specific on crop disease pathogens, but that information must be conveyed in a way that actually helps producers make rotation decisions.
This is done by setting the high idle, then putting load to it, choosing a gear that causes the engine speed to drop slightly, but holds at the rated-load engine r.p.m. This is the speed that has the best fuel use to horsepower ratio. Try to operate at that engine speed as much of the time as possible.
For example, on an older Massey combine, set the high idle to get a 740 rear beater speed. Then, when you are combining, load the machine until the speed drops to 710 r.p.m. Not only is this best for fuel economy but it is also the best for combine performance.
The same principle applies to other machines. To take the most advantage you can of the well loaded, but not over or under loaded machine, run it steadily. Don’t vary the load.
DON’T OVER WEIGHT TRACTOR
There are people who think that every big tractor must have a full load of fluid in the tires. That might not be so. The first thing to consider is whether you are exceeding the maximum weight of the tractor as given in your operators manual.
Before you put ballast in the tires, check to see how much slippage you have. It should be 10 percent. That is the place where you get best fuel to horsepower ratio.
If it is more than 10 percent, cure the bouncing problem by distributing the load properly. Remember, a bouncing tractor is not a pulling tractor. Then if you still have a problem, you have to put in some weight.
The key to ballast is to make sure you have the problem before you solve it and then only add enough to get the traction you need.
SET COMBINE PROPERLY
There are people who set their combine approximately, and then when they get out in the field they see they have a dirty sample. The first thing they do is close the bottom sieve just a notch. They are happy that they solved the problem and the sample is cleaner with maybe a few more cracks. But did they solve the issue? Where did that unthreshed material go? It went back to the cylinder to be handled again.
On some combines, you can hear the growling and the engine work a little harder when that returned material hits the cylinder or rotor.
The best way to solve the issue is to open that sieve right up so everything goes into the hopper. Then set your cylinder or rotor and concave to do the best possible job of threshing that crop.
The sample should be as clean as possible before closing that bottom sieve and sending material back to the primary threshing area. You would be shocked how much faster you can go and how much fuel you will save per bushel threshed.
MAINTENANCE MAKES A DIFFERENCE
Things that can cause extra fuel to be used include a partially plugged air filter, a bad injector or a cold running engine. This list could be long, but in short you save fuel every day by keeping up with the recommended maintenance.
Henry Guenter is a former service manager for Massey Ferguson. Contact: