Fibreglass was the standby material for construction insulation for decades.
It looks like cotton candy and is actually made in a similar way, although from hot sand rather than sugar.
Fibreglass was used in insulation applications of all sorts: wall cavities and ceilings in residential construction and roofs in commercial installations. It found its way into both hot and cold insulation, from water heaters to pipes.
Fibreglass insulation is still around, but today it has competition.
For batt insulation there is rockwool, made from slag, which is similar to fibreglass but has a somewhat higher R-value. The dull green Roxul brand is the most common.
Read Also
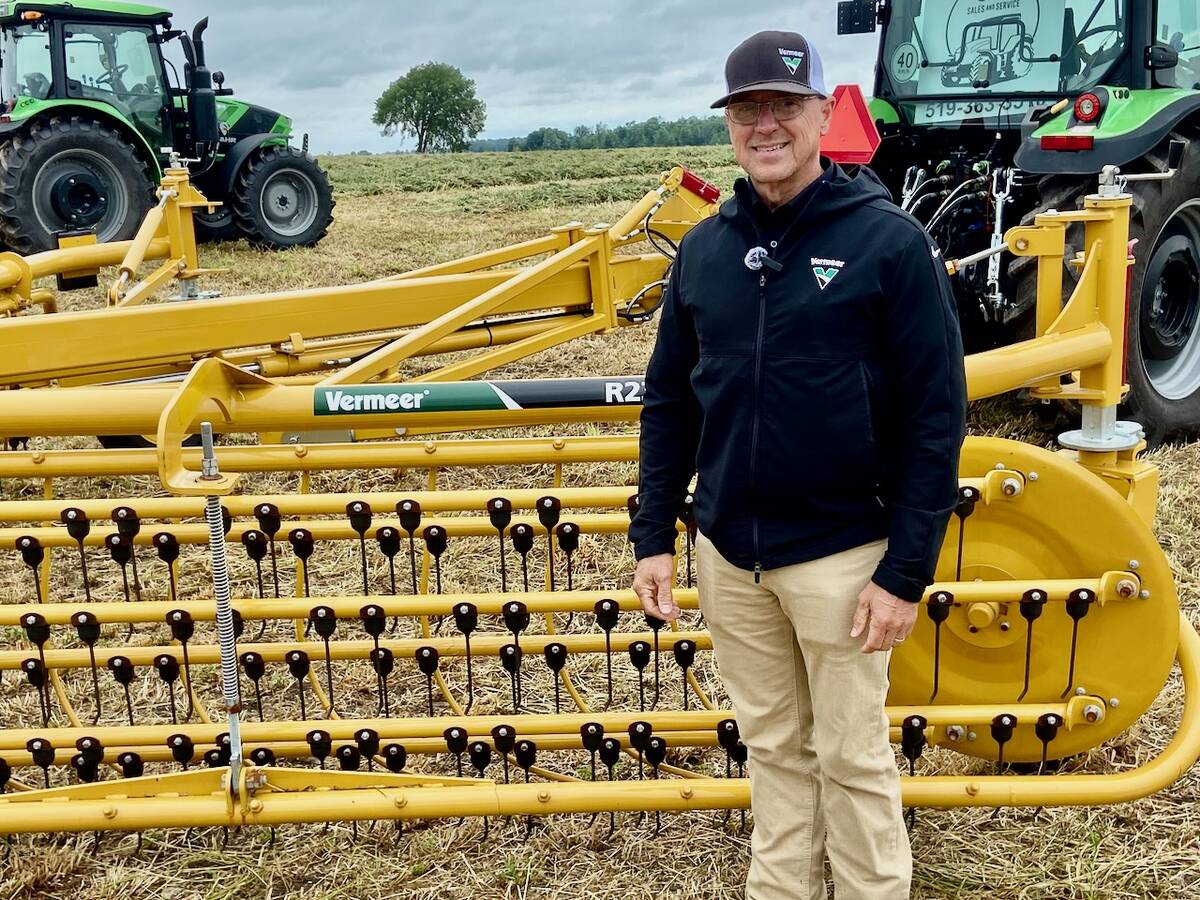
Basket rakes pitched for top-quality windrows
Boxy, clean windrows help make better hay bales for livestock farms and forage growers, and a basket rake excels in those areas, says Bart Elder of Vermeer.
For attic insulation there is cellulose, which is essentially ground up newspaper. It is perhaps the most environmentally sound insulation material.
Two tests have helped better under-stand the importance of insulation and sealing buildings against air movement: air pressure testing, which pressurizes a building and looks for air leaks; and thermography, which takes photographs to show infrared radiation.
Batt and loose insulation, including fibreglass, both have a drawback. They reduce air movement but do not eliminate it or the water vapour in the air.
The industry has responded to this problem by installing polyethylene sheeting as an air-vapour resistant barrier between insulation and the interior of the structure.
The development of petroleum based insulations have dramatically changed the options.
Foam sheet insulation has low air and moisture permeability, particularly the more dense versions such as an extruded styrofoam, which is usually pink or blue, and polyisocyanurate, a dense white foam with two foil faces.
They can be used for retrofitting and in new installations.
Sheet foam insulations can be used for above grade and below grade applications, which helps insulate foundations and basement walls on the outside.
The industry has discovered that sheet foam can go on the inside of the stud wall or on the outside.
In both cases, it should be installed tightly with taping only at the joints. It has also been determined that moisture movement into the wall can largely be stopped by stopping the moving air.
Foam sheet insulation also mitigates the impact of thermal bridging in studs.
Wood studs are not a good insulator, about R1 per inch, and it is evident in thermal imaging. It means that studs located next to windows are the weak part of the wall in heat loss prevention.
A 2 x 6 wall with R19 batts is really R16 when averaged over the entire wall.
Installing a continuous two-inch layer of styrofoam over a stud wall adds the full value of that insulation to the wall. In other words, R5 per inch provides R10.
Add that to the R16 and it creates an effective insulation total of R26, which is more than a 60 percent gain in insulative value.
Spray foam is the new kid on block. For those old enough, there are bad memories of the urea formaldehyde fiasco of the 1970s, in which the material was sprayed into wall cavities of older houses.
Poor installation could result in health issues with offgassing, and the resulting bad publicity meant that spray foam vanished for a while.
However, we have seen a resurgence of spray foam insulation in the last 10 years, and it is much improved.
There are two types:
Open cell, or half-pound foam, is soft to the touch and has a value of more than R3.5.
Closed cell, or two-pound foam, is typically R5 or more per inch.
Some potential insulative value is lost when used between studs be-cause installers cannot entirely fill the cavity.
The application can never be exact and smooth, as with batt or sheet material, so the installation is stopped short of filling the stud wall cavity to ensure that the finished material does not extend beyond the face of the studs.
This type of insulation can be effective in certain circumstances. It seals much better than batt insulation and does not absorb moisture, which makes it useful in basement wall applications.
It is particularly good for hard-to-insulate structures such as steel quonsets. It is also approved for use in unvented spaces such as cathedral roofs.
There is little waste with spray foam and installation is fast, but it is also pricey: easily two to three times the cost of batt-poly installations.
It is likely to remain one of many options with attributes for special situations.
For those who like to put things to the environmental test, all products, including foam insulation, have their downsides.
Ozone-depleting chemicals in foam insulation have been reduced or eliminated, but there are still concerns about flame retardants that stay in the environment. The greatest concern is about off-gassing in living space.
Flame retardants vary from 0.5 percent by weight in expanded polystyrene sheet foam to 12.5 percent in open cell spray foam. These retardants are not part of batt insulations or cellulose.
Flame retardant is not required where there is a thermal barrier such as half inch drywall, but the codes call for it.
Some argue that the long-term energy saving resulting from an exceptional insulation job compensates for any other shortcomings. Others argue that we must go the extra mile to avoid environmental compromise.
As always, we will be better able to judge the wisdom of these arguments somewhere down the road. In the meantime, even with something seemingly as innocuous as insulation, there are benefits and detriments to consider — all the way from fibreglass to foam.
Will Oddie is a renewable energy, sustainable building consultant with a lifetime interest in energy conservation. To contact Oddie, send e-mail to energyfield@producer.com.