The latest low-cost metal inert gas (MIG) wire feed welders are a popular purchase these days. They make beautiful welds and instantly turn anyone into an expert, so the story goes.
But the story is false.
The problem isn’t the machine. Manufacturers make fantastic little welders for less than $1,000. Even the 110-volt units have an amazingly good, stable arc. They are hot little machines with good penetration if used right.
The problem is that so many people think a pretty weld is a good weld.
Read Also
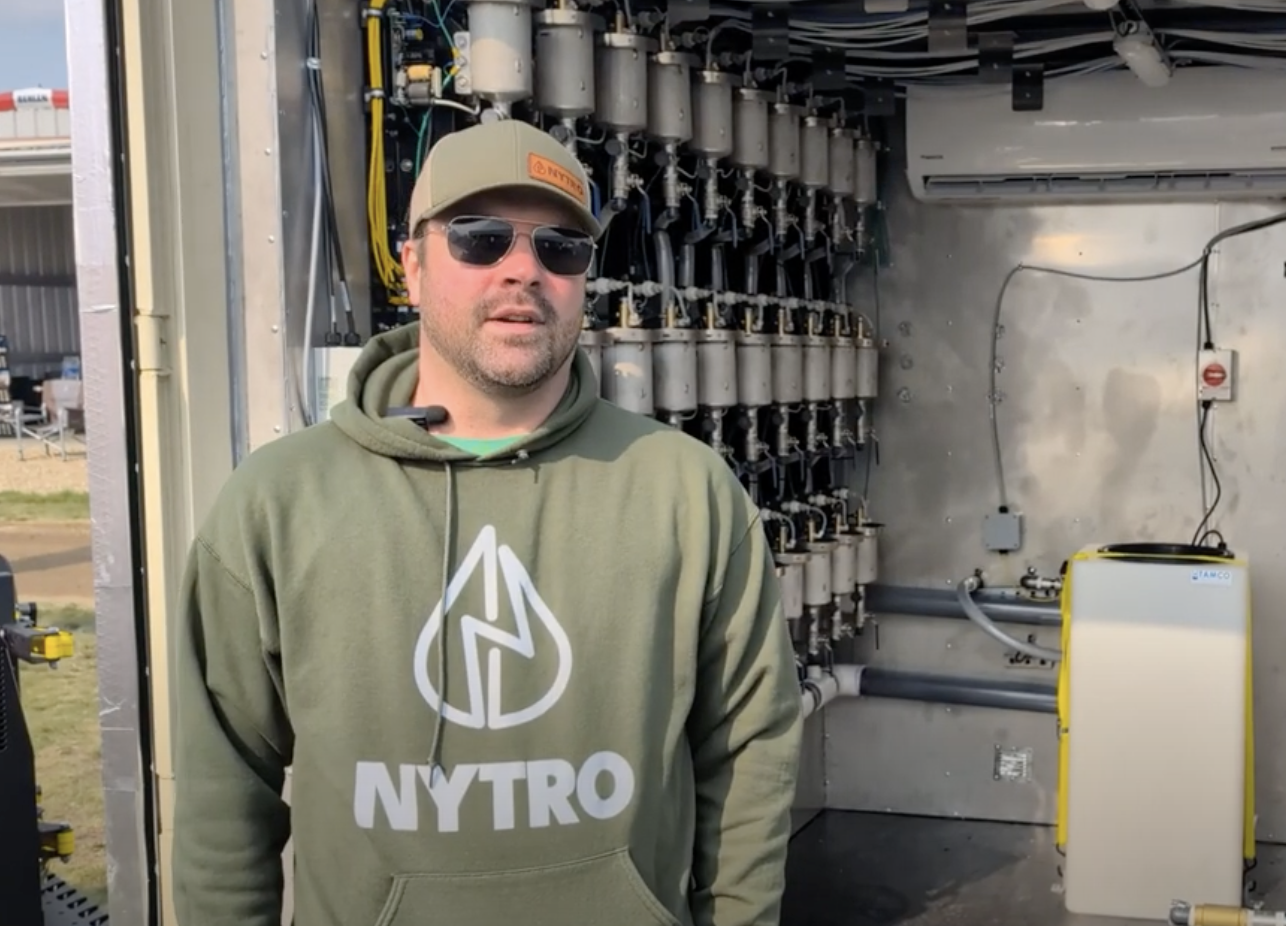
VIDEO: Green Lightning and Nytro Ag win sustainability innovation award
Nytro Ag Corp and Green Lightning recieved an innovation award at Ag in Motion 2025 for the Green Lightning Nitrogen Machine, which converts atmospheric nitrogen into a plant-usable form.
In a common scenario, the new owner fires up his new MIG, lays down a bead, steps back and says, “damn, I’m good.”
Now, take that beautiful experiment, put it in a vice, give it a little whack with your ball peen hammer and it falls apart. Beauty really is only skin deep.
In my example, this welder, when using this machine, should not be welding anything more critical than lawn ornaments. Keep him away from your implements.
MIG is easy to use but hard to master. The nice appearance only serves to compound the problem by giving people false confidence.
If the machine isn’t set right, you get a beauty of a bead, but it’s mainly just penetrating one side of the weld. The other side isn’t stuck at all, as the hammer test will confirm.
To check weld quality while you’re welding, finish a bead and then flip up your helmet right away. If the bead is orange and the base material is not orange, there is no penetration. That tells you it’s time to reread the manual or better yet, enroll in a one-day class that teaches about voltage settings and wire feed speed.
One factor alone – wire feed speed – can make all the difference. If wire speed is too slow, you can hear a swish swish sound. If speed is too fast, you can feel a stabbing at the tip as wire hits the base material.
MIG has more variables than stick welding. Wire is mechanically driven through the liner tube. Pushing a thin little wire through the whip is a lot like pushing a string. Slippage can occur if the drive rollers are dirty or worn. They won’t push the wire to the contact tip properly.
The most common MIG mistake is too much tension on the drive rollers, which causes premature wear and wire feeding problems. When it jams up, you’ve got an instant bird’s nest of wire in the machine.
When adjusting rollers, you need just enough pressure so the wire can barely push a six-inch length of 2 x 4 across a clean surface, and nothing more.
Always treat the whip with care. Wire and gas flow down the same tube. All it takes to jam is a hammer or piece of steel falling from the bench. At the Winnipeg Technical College where I teach, we mount our wire feeders up high on a shelf so the whip always has a nice gentle curve down to the welding area.
The duty cycle on the entry level 110 volt MIG is only 30 to 40 percent, so in every 10 minute period, you’ll need to rest the welder for six or seven minutes to let it cool down.
I never use a MIG on any project where structural integrity is important, such as a hitch or loader arms. That’s always a job for the stick. The only exception is when there’s a cored wire available, such as flex core or metal core.
A few years ago, Boeing used MIG to weld aluminum seats. When analyzing plane crashes, they found the seats were breaking to pieces on impact. They now use TIG (tungsten inert gas) for all such components that demand structural integrity.
There are many different gas mixes, all comprising some ratio of oxygen, carbon dioxide and argon. Some mixes are designed for deep penetration while others are for thin or delicate metals. Your gas dealer should be able to assist you on this.
The wire feed is metal and the gas flowing down the tube is an inert gas, hence the MIG moniker, but technically it’s called gas metal arc welding.
There are three modes of heat transfer in MIG:
- Short circuit is a fast buzzing sound mainly for metal less than 1/8 inch, usually about 10 to 19 volts.
- Globular transfer is for metal up to 1/4 inch. If you watch the wire closely, it transforms itself from a solid wire into globs or droplets before becoming a liquid in the puddle. Globular transfer requires more voltage, typically in the area of 20 to 23 volts, and higher wire feed speed.
- Spray transfer is reserved for material such as plate steel 3/8 inch or thicker. It requires higher voltages of more than 24.
In future columns, I will look at flux core and metal core wires. These are good choices for materials that are not as clean as they should be, with rust, oil or paint. I will also examine the push/pull MIG that actually pulls wire through the MIG torch.
Jason Feal is a nationally certified welder. He has experience in construction welding including bridges and towers. He began teaching welding at Winnipeg Technical College in 2005.