Henry Guenter was a service manager for Massey Ferguson for many years. He is now retired and living in Saskatoon, but decided to compile some of his observations on how to improve the operation of certain types of MF equipment.
While the Western Producer didn’t have the space to put all his observations in print, it decided to make the information available here on the WP website.
The following information has been provided by Mr. Guenter and the Western Producer to help farmers still operating this machinery.
Read Also
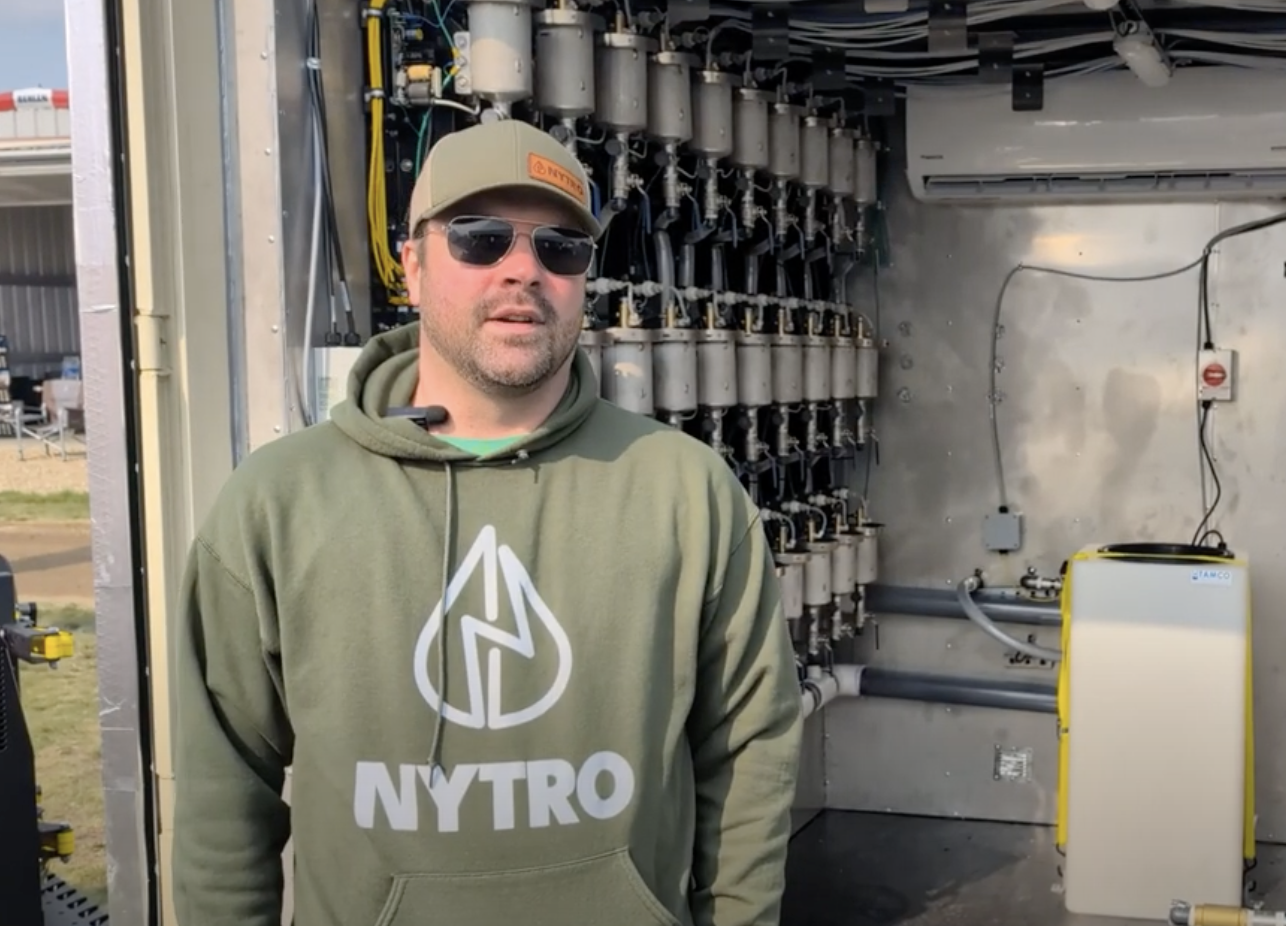
VIDEO: Green Lightning and Nytro Ag win sustainability innovation award
Nytro Ag Corp and Green Lightning recieved an innovation award at Ag in Motion 2025 for the Green Lightning Nitrogen Machine, which converts atmospheric nitrogen into a plant-usable form.
Your operator’s manual is a book worth studying. It has a lot of good advice but it obviously cannot cover every conceivable situation.
It has been my privilege to hear a lot of farmers explain what they do in exceptional circumstances. I have learned a lot at clinics, on the farmer’s field, and talking to farmers at the dealership.
I am not the expert. The people who run these machines know what they need to run them in the crop they are in at the moment. But I have gathered a lot of information and I would like to share it with you.
MF 410 510 550 750 760 850 860 865 751 851 852 combines
HANDLING THE CROP
1. Speed of the machine
This is always the first thing to check on any problem you might have with the combine. This is true of any make.
On the MF the speed is read off the rear beater from which all other parts of the combine are driven. It should read 710 or 740 RPM depending on the serial number. That is without any load on the combine. This speed is set on the fuel injection pump. Before you do any work adjusting the speed make sure the cable is pulling the pump lever tight against the stop.
What should the speed of the rear beater be when I am combining?
There is a speed at which the engine develops full horsepower and it is also the speed at which the combine is the most efficient.
On the combine with the rear beater speed of 740 you will have the best results at about 710. This means you should be able to push the forward speed ahead increasing load until the speed drops close to 710 but the closer you get to 710 the more the engine seems to want to “hang on.”
You should be able to increase the load on the engine a lot at this point without losing an appreciable amount of speed. If you push the combine till the speed drops to 680 or 690, you will not only notice an increase in losses but also you are getting close to plugging it.
The shoe and the walkers are designed to run at 710. Slower or faster will create losses. This is a major issue on the pull-type combine because owners seem to think they have to push the throttle ahead to keep the speed at 1000 RPM PTO speed no matter what the load.
The combine is actually running too fast and you will have losses. Also you will have damage to the shoe, pitman arm and bearings because the combine will tend to run way too fast when the load comes off at the corners.
2. The 700 and 800 series combines had the paddle system in the feeder house. The only adjustment was that they had to be timed to 90 degrees to each other.
Why do I have so much wear and bending of the paddles?
Basically you are sending too much material in lumps up the feeder house.
For some years MF had an extra set of holes in the hubs because they were used in both directions. You could raise the paddles off the floor by moving the paddles to the other holes.
How do I prevent wrapping, especially in flax?
There are anti wrap shields available but they are not always successful. Try the following:
a. Lining up the paddles in a straight line. This will knock the material off each other as they pass. Of course if you raised the paddles as per above they will be too far away from each other.
b. Grind down every sharp corner anywhere in the feeder house.
c. Put four paddles on every shaft. This is by far the most effective.
3. The front beater has two purposes – to knock the stones into the stone/trap just below it and to provide a smooth flow of material to the cylinder.
I am not too sure the beater is what knocks the stones into the stone trap. I think the cylinder does that. Of course if the trap is full of dirt it can’t do its job.
If there is a problem in this area you could hear the cylinder slugging resulting in cracked grain, dirty sample, overloading of the return system etc. The problem could just be a worn beater or too short a crop. There is a covering for the trap, which covers the front so the stones and the crop have to go over the trap.
4. This combine has a high inertia cylinder. The hubs are made of heavy cast iron. Up until about 1978 the hubs had a zero degree rub bar surface. Then they went to a nine degree surface to make the cylinder more aggressive, especially in tough conditions such as weathered swaths.
In dry conditions it had a tendency to over thresh. It was really not a problem until they made the concave longer to give us more threshing area.
That was added to the front so that material was fed in at a sharper angle and you experienced a lot of overthreshing.
If you have that problem you can add wedges under the rub bars but they could come loose and cause a lot of damage. Better to replace the hubs.
5. All unthreshed material goes to separate cylinder to be threshed again. This is called the return system. Many combines have something to handle unthreshed material. Usually it is fed back to the main cylinder. Obviously the less you have in this system the better.
On the MF combine, the rethreshed material gets blown onto the pan under the walkers. There is enough force to blow it right across to the left side and if there is a lot of it you will encounter a lot of loss on the left side of the shoe – a strip about six inches wide.
Later combines had two paddles mounted to the bottom of two walkers directly in the path of this flow of material in such a way that when one was up the other was down. They can be installed in earlier units.
CONCAVES
For our country there were two different concaves, a narrow spaced and a wide spaced. This referred to distance between the rods.
The narrow spaced was introduced to take care of the hard to thresh Neepawa wheat. It held the material up against the cylinder longer but that was also its weakness. It seriously cut capacity in large kernel grain such as barley or durum.
Some owners tried to increase capacity by removing every other wire or rod. They found out that by removing them in just one bar, they gained about half a mile an hour.
If you do decide to remove every other rod make sure you close the holes left in the concave. The straw will weave into these holes and make a perfect basket.
Spot welding warps the concave. Bolts will cut capacity. Silicone is too soft. An epoxy like liquid steel is probably the best.
Now you have a concave that is much like the wide spaced concave. Now you could have another problem.
As you are doing all this experimenting you will all of a sudden notice losses over the left side of the shoe. You have overloaded the return as I explained before. Too much material is getting through the concave before it is threshed.
The answer was to put in concave blanks. You might need to blank as many as eight bars before you cured the problem, although at this point you haven’t got a lot of capacity left.
The blanks that fit underneath the concave were a lot better. They left the bars exposed so they were threshing. You didn’t need as many blanks. They were also easier to put in. You could pull the front of the grain pan out like a drawer.
The concave diameter is bigger than the cylinder. This means when you set the back of the concave tight against the cylinder you cannot bring the front tighter than 5/16 of an inch because the middle will touch.
WALKERS
For grain loss in this area you should check the grate behind the concave. It should be within an inch of the rear beater.
When you plug the combine it is possible to bend this grate down. Then you won’t have the aggressive action you need. You can see this grate through the inspection hole on the right side of the machine.
There is a row of belt-like curtains behind the beater. They should have the natural curl to the back. If they are installed with the curl forward, the rear beater will eat them up.
SHOE
The shoe separates the grain from everything else. Its job is made easier by the job the rest of the combine is doing.
One of the biggest mistakes people make is to try to set this area when they should be setting the source of the problem. For example, we play with the wind to try to solve the chaff problem when we should be solving an overthreshing problem.
We usually diagnose problems by checking for losses on the ground and the sample in the tank. We aim for no losses, no damaged kernels, and no whitecaps. There isn’t a combine built that will deliver this.
People like PAMI will accept a total loss of three percent including the weather. You probably lose about two percent by weather, header, what’s cracked, ground up and blown out as flour. That means you shouldn’t see more than one percent out the back of the combine.
In a 100 bushel crop if you read 22 kernels per square foot over the full width of cut you would have one percent loss. However you are narrowing this to five feet or 1/6 the total if your swather or header is 30 feet.
So you multiply the 22 by 6 and you get 132 kernels per square foot to make a one percent loss.
I am not saying you should be satisfied with that but it puts it in proper prospective. I am used to seeing less than 10 kernels.
Lets start with a very basic shoe setting. The front part of the of top sieve of the triple sieve shoe should be about 3/4 open to provide clear path for the air to come through. This will catch the material as it is coming off the grain pan.
You will know that you have the correct amount of air when you see a nice rooster tail of chaff falling between the shoe and the straw chopper.
If you have a dirty sample in the grain tank, especially unthreshed material, the temptation is to close the front part of the top sieve. This will clean it up but now you have overloaded the return system and you will probably see a streak of grain about six inches wide coming over the left side of the shoe.
Much better than closing the sieve would be to find out why you are not threshing everything. Maybe you need to put in some filler plates or set the concave tighter or speed up the cylinder.
There is an option available to put a round-hole sieve in front of the bottom sieve that you could order with the combine. There were many sizes available but they were just flat sheets of metal with holes in it.
The flat surface had a tendency to deflect the air and it also seemed to push a lot of grain into the fan housing. Better was an adjustable sieve commonly called the Peterson sieve.
One of the problems was the airflow pattern on the shoe. In some crops you could never seem to get the air just right. You seem to get a lot of chaff in the bin and if you increased the air to blow it out you started to lose grain.
The problem was that you had an uneven airflow coming from the fan. On that type of fan the air comes in from the ends and is in a crossing pattern when it gets to the shoe so you will have dead spots.
With the combine running, spray different colored paints into each intake and then check the bottom of the shoe and it will tell you the story. Some parts will be all colors and some parts will have no paint.
The answer is the fan dividers that were installed as standard in 1983. They will retrofit all combines.
The hillside kit might have been very good for steep hills but they caused two problems. On the shoe there was always a dead spot in the lee of each divider. In swathed grain with the herringbone pattern on the swath, the grain is mainly in the center. These dividers seemed to hold it there all the way to the end, overloading the middle of the shoe.
MECHANICAL PROBLEMS
VIBRATION
One of the main reasons why a combine started vibrating was the sagging of the frame under the operator’s platform.
This is very common. This in turn pulled down the engine output shaft. It caused the output shaft to run at an angle to the drive disc.
You could hear it squawking away when you idled it slowly. Very often the disc would be cracked and the tip broken off the shaft. This can be corrected by putting in a new style bearing and shaft and housing.
Since the frame has settled you need to reset the alignment. Attach the whole assembly to the engine. Add enough shims to just take up the clearance between tube support and frame. Then add 50 thou for the 850 and 60 thou for the 860.
When doing this job you might find out there is a side load on the engine output shaft when you try to put the bearing on. Cut a hole in the flywheel housing so you can loosen all the bolts on drive disc and then tighten them again.
You can check your job by drilling a hole in the output tube and putting a dial indicator on the shaft. The less runout you have the less the vibration will be.
The outer bearing was changed many times. Originally there was a seven ball bearing in the 510 and the 750 and a ten ball bearing in the higher horsepower units. People were always getting them mixed up.
Next was a single tapered roller bearing held in with a washer. It never was very good.
Next was a double tapered roller bearing, which required changing the tube too, but it was very good.
Another thing that happened when the frame started sagging was that the center traction drive pulley ran at an angle causing belt failure and vibration. This can easily be checked.
Change speed on the variable speed until both top and bottom belts are equal distance into the center variator pulleys. Just looking at them from the front will tell you if the belts are square to the pulleys. Line them up by adding shims to the top and back of the variator frame.
Another thing that caused vibration was a balance problem.
Most often it was the bottom pulley. This vibration increased as you moved the speed lever towards top speed.
It must be balanced at 3000 RPM. Many shops will try to tell you that 1000 is good enough. You will likely find out that the input shaft has an endplay of 30 to 40 thou. It should be 9 to 1 thou.
I don’t know whether the extra endplay caused this problem or whether the pulley being out of balance cause the bearing to wear. In any case check the bearing. Then put shims behind the outer race to set this bearing as close as you can get to 1 thou. If you can’t find any shims I think the ones from the 510 release bearing will work.
It could also be a balance problem with the top pulley. This showed up as a vibration that was totally related to engine speed. It can be severe enough to shake the cab bolts loose.
The causes were varied:
* Poor assembly – This is a balanced unit and should be marked when you take it apart for any reason so you can assemble it the same way you took it apart;
* Dirt in the pulley;
* For a couple of years the pulley was made so shallow that the belt would ride in the bottom of the pulley.
The vibration coming from the middle pulley was not so much a balance problem but more of an assembly problem and a wear problem.
It can be detected by running the variator through all speeds. If the smoothest spot is in the middle of the belt travel then you should look at the middle pulley.
Since this problem is so closely related to belt failure I will deal with them together.
There were many causes of belt failure and vibration. The most common was excessive wear on the hub. This made the center shive run at a different angle than the other two shives and therefore not the same angle as the belt.
The belt would fail fast on the sides. Worse than that was uneven wear on the hub making the center shive wobble. That made the belt walk in and out and it would just tear to shreds in no time.
The big spring in the pulleys might be installed in the wrong side. This would fail the upper belt real quickly.
Sometimes the upper traction belt was just too tight. People were continuously mixing springs to get more traction and if you ended up with a spring from a 760 hydro on a 750 standard it would last about a day.
Sometimes the operator was just too rough. The later combines had an orifice in the speed change cylinder so the operator could not accelerate so quickly.
GRAINPAN/SHOE ASSEMBLY
Sometimes you will hear a pounding or vibration/shudder much more noticeable when the combine is running empty.
Turn the combine over until the shoe is all the way back and of course the grain pan will be all the way forward. You will probably see one corner of the shoe will touch the frame and the opposite corner of the pan will touch the frame.
At this point it might not quite touch but you can see the wear marks on the frame. This can cause enough vibration to crack the walker body and shoe/pan, break the pitman arm, ruin the bearings, etc.
To square the pan/shoe to the combine you switch shims from side to side under the rocker shaft bearing supports. Never add or remove from the total.
If the shoe and the pan are both touching on the same side the rocker shaft is not welded properly.
510 COMBINE
It had one serious problem, which was very consistent and baffling. The grain pan would load up with material until it piled up against the pan under the walkers and plug up the whole combine. This would go on all afternoon and cure itself right about sundown.
There are all kinds of bulletins written and suggestions made to move pan back and everything else to give the material more room to get through. What seems to work the best is to close the hole behind the concave.
There is a plate fastened to the grate, which can be flipped over to cover this hole or gap. What is happening is that when it is very dry the rear beater pushes everything off the concave through this opening onto the grain pan. But with the slightest moisture the straw goes over the opening onto the walkers.
HYDRAULICS
One of the problems was oil heating. The most common reason was that the unloader valve was sticking.
It usually happened in the home position right after you unloaded a load of grain. You just pushed the lever to bring the auger home and forgot about it, expecting it to kick out.
This might be because the spool is binding in the body. The frame it is bolted to could warp it. Try just loosening the bolts. Or possibly because the linkage is binding.
Another reason why the oil could be heating is that you are trying to run the hydro lever in the lower half of the quadrant. You have picked too high a gear.
If you took a pressure reading you will find out that the lower the gear the lower the oil pressure. Running too small a motor on the pickup.
Hard steering
The combine had hard steering when it had one cylinder in the back. Later combines had two cylinders.
People complained it was harder but it actually was slower and people were trying to steer faster than the system could deliver. If you drill out the orifice in the center of the spool you get faster steering but remember you are robbing this from the header lift.
GENERAL SERVICE QUESTIONS YOU MIGHT HAVE
ABOUT THE AIR CLEANER
1. When should I service my air cleaner?
Basically when the indicator tells you to service the air cleaner. Donaldson, who makes the air system for a lot of companies, tells us that if the air filter can be blamed for an engine failure, 75% or more times the fault was that the operator serviced it too often. Their point was that every time the operator touches the air cleaner there is a risk of damage. Remember a plugged filter will not ruin an engine but a damaged one will.
2. In what ways can I damage my filter?
Slapping the sides with the palm of your hand. The slightest bend in the metal shield around the paper element will allow it to touch the element and since the paper is moving all the time there will soon be a hole in the paper.
By hitting the corner of the end cap against the tire. This will crack the glue that holds the paper to the end cap.
By washing too often or with the wrong solution.
3. How long will my filter last?
The book recommends that you change it after a set number of hours or after a certain number of washings or a time period. When the engine is running the paper will bend back and forth and there are only so many bends in the paper. This is regardless of it ever got dirty.
Because the paper is treated with a chemical and this chemical will dissipate into the atmosphere the filter should be replaced in the given time in your book
4. How can I tell when my filter is damaged?
If you pull the filter out of the tractor and before you disturb anything put a clean sheet of paper into the filter and just touch the out side. There should be no dirt on the paper.
The safety element should have no dust on it.
If you use a light to check for damage you are looking for little pinpricks of light the same as you see on TV when the camera is directly on the lights.
OIL IN THE ENGINE
When should I change oil?
Basically when you need to. Much has been made of the hours given in the book but that is just a maximum.
You might need to change sooner because you start using oil. This would be especially true of multigrade oil.
It seems that when a multigrade oil breaks down its additives break down first. So a 10/30 would become a 10 and a 10 burns more oil than a 30. The harder you use an engine the sooner it will break down.
If you are using the engine for short periods of time in cold weather, differences in temperature cause moisture to collect in the crankcase. The detergent in the oil gives it the capacity to hold some moisture in suspension but eventually it becomes saturated and the moisture will combine with sulfur in the oil to make sulfuric acid, which eats metal.
Why is my engine using oil?
First of all, is it actually using oil? Manufacturers will tell us that they expect about 0.5 percent of fuel consumption and they will not consider even one percent to be excessive.
It might be using oil because you got dirt in the engine. You might have overfilled it.
If your engine uses oil down to a certain level then stops using oil, your full mark on the dipstick is probably too high. Fill the crankcase with the right amount of oil and then check on the dipstick where that is. That becomes your full mark.
Tip – Always put clean oil in an engine that is going to be parked for a long period of time.
SPEEDS
At what speed should I run my tractor?
A general rule of thumb is to run the engine at rated speed. To run it at half throttle when you are under light load will probably carbon up your injectors and your muffler. Both will show up as low HP.
When you are working the engine it is best to pick a gear that will lug the engine down to rated load speed. That is where the engine is most efficient.
Closely related to this is the question whether or not you should put fluid in your tires. If the tractor can’t slip a little bit you will use more fuel and it will feel like you have a dead engine. You should work towards having 10 percent slippage. For a quick read that would be if the imprint of the lug on the tire moved back its own width.
Why does my tractor bounce around so much in the field?
Basically it is because one axle is trying to go faster than the other one. It only happens with radial tires where you have very good traction. The reasons why it is trying to go faster could be one of many.
It could be because it is turning faster as in the front wheel assist. Try the following:
1. Make sure the ratio of wheels is right. Sometimes people will order special size wheels for a particular job and they end up with a very big difference.
2. Change tire air pressure so you have maximum in front and minimum in the back. That will give the back more traction.
3. Put weights on the back.
4. Sometimes you can accomplish 2 and 3 just by attaching the implement to a higher point.
5. Sometimes you just have to try and try again until some combination works and you have no idea why.
On the four wheel drive tractor the axles both turn the same speed.