Anyone who has ever sat next to a crackling fire knows there is plenty of energy stored in wood. It’s getting it into your gas tank that’s the problem.
Arthur Zegil and Jude Sanson, president and vice-president of Winnipeg-based W2E Technologies believe they may have found the solution to that problem.
For nearly three years they have been working on a way to perfect the gasification process, converting thumb-sized wood chips into flammable hydrogen, methane and carbon monoxide which, along with a tiny amount of diesel, run a huge Mirrlees stationary diesel engine capable of generating two megawatts of electricity.
Read Also
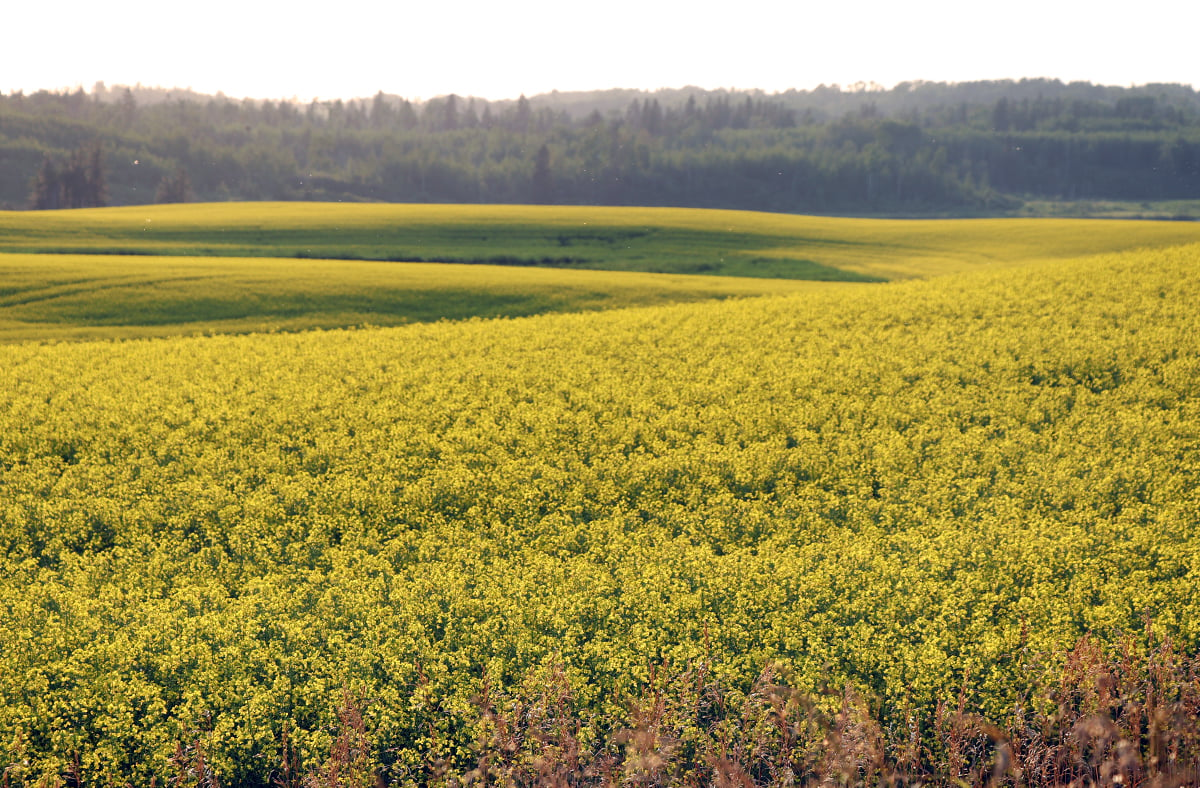
Agriculture ministers agree to AgriStability changes
federal government proposed several months ago to increase the compensation rate from 80 to 90 per cent and double the maximum payment from $3 million to $6 million
The privately financed project at FinMac Lumber, a sawmill near Winnipeg, is currently using chipped first-cut slabs, a burdensome waste material, which is harder to get rid of due to decreased demand from paper mills. Depending on the size of a log, as much as 20 percent of it is discarded slabs.
“Other materials, such as hemp or flax straw fibre, work well, too,” said Zegil. “You just gather it up, press it into cubes, and voila, electricity.”
More work will need to be done before wheat straw can be used, since it contains a lot of silicate residues, which cause premature engine wear and are difficult to filter out, he said.
To get the generator’s giant pistons thundering, the wood has to be turned into something that will flow through the intakes. First, a two tonne hopper is filled with dried wood chips that are carried by auger to the gasifier, a 2.5-metre long tank filled with “top secret” processes for which patents are pending, the inventors said.
The gas is then passed through funnel shaped cyclones that filter off the engine-destroying tar and soot particles that have bedeviled gasifier designers for more than a century.
“The thing that makes our gasifier different from others in Manitoba is that we are making gas that is almost tar-free. We operate at a high enough temperature that we actually crack the tar,” said Sanson.
“If you try to run an engine using other gasifier designs, it’s going to gum up. It’s the tar that’s in wood gas that is a big issue with engines.”
After that, a giant condenser unit, which looks like a steel radiator, cools the gas to make it dense and therefore produce more horsepower.
The gas mixture, which is roughly 15-20 percent hydrogen, three percent methane, 25 percent carbon monoxide and the balance nitrogen, then runs through a gas pipe to the engine inside the building.
The gas produced is about 160 British thermal units, compared to 1,000 for natural gas.
“But you don’t have to drill for it. There are lots of associated costs for natural gas that we don’t incur,” said Sanson. “The biggest cost of getting rid of waste wood is transport, so we are looking at ways to make use of materials where they are created.”
The Mirrlees diesel, which runs at a constant 600 rpm, typically consumes 13 gallons of diesel per hour while generating 175 kilowatts of electricity. Put a heavier load on it, like the two-megawatt generation unit sitting just a few feet away in the shop, and fuel consumption soars.
“Extrapolate to two megawatts, and you’ve got a huge amount of diesel going through that engine,” said Zegil. “But we run it on four percent diesel and 96 percent wood gas.”
Hooked up to the gasifier, and using two tonnes of wood chips per hour, its diesel consumption over a 24 hour period is just two gallons.
“This style of engine, which is the smallest of the big diesels, has been around for about 60 years. It hasn’t changed a whole lot since then,” said Sanson. Maintenance, such as oil changes, can be done on the fly. “It is made to run 24 hours a day, seven days a week, for years on end.”
If biodiesel was used instead of regular diesel, the system could churn out power using only renewable fuels, said Sanson, and could potentially allow the owner to cash in on Kyoto credits.
“Gasification is not a new idea. The issue is commercializing it at a large enough scale to make it economically viable,” said Sanson.
Still, more work could be done to increase the efficiency of the unit, such as using waste heat from the gasifier and engine exhaust, which hits 318 C, to dry the wood chips or for heating buildings and kilns.
The Mirrlees is able to convert about 31 percent of its fuel consumption into mechanical energy, with the rest lost as heat. This rate is typical for an internal combustion engine, said Zegil.
It’s a little-known fact, he added, but during the Second World War up to half of the passenger cars in Germany and Sweden ran on wood chip gasifiers. After the war, the crude systems, which drastically shortened engine life, were discarded en masse once cheap gasoline reappeared.
Making the system economically viable depends largely on the cost of electricity, which varies according to location. Other factors include a potential customer’s energy consumption and costs, and whether they can be connected to the grid.
“If you go to some places in the United States, you can earn up to 25 cents a kilowatt hour,” said Sanson. “But the fact is, there is an incredible amount of waste materials out there and energy costs are increasing.”