Research shows a small amount of the marine algae added to feed can reduce methane emissions by 99 percent
Global demand for seaweed is increasing as it becomes more recognized as a good source of vitamins and minerals for humans and livestock.
It is also a good source of amino acids, anti-oxidants and essential fatty acids. As well, it acts as a good soil fertilizer and has been used by the cosmetics industry.
Feeding seaweed to cattle has been proven to increase overall health and growth rates but more recently research has indicated a small amount of the marine algae added to cattle feed can reduce methane emissions from cattle gut microbes by as much as 99 percent.
Read Also
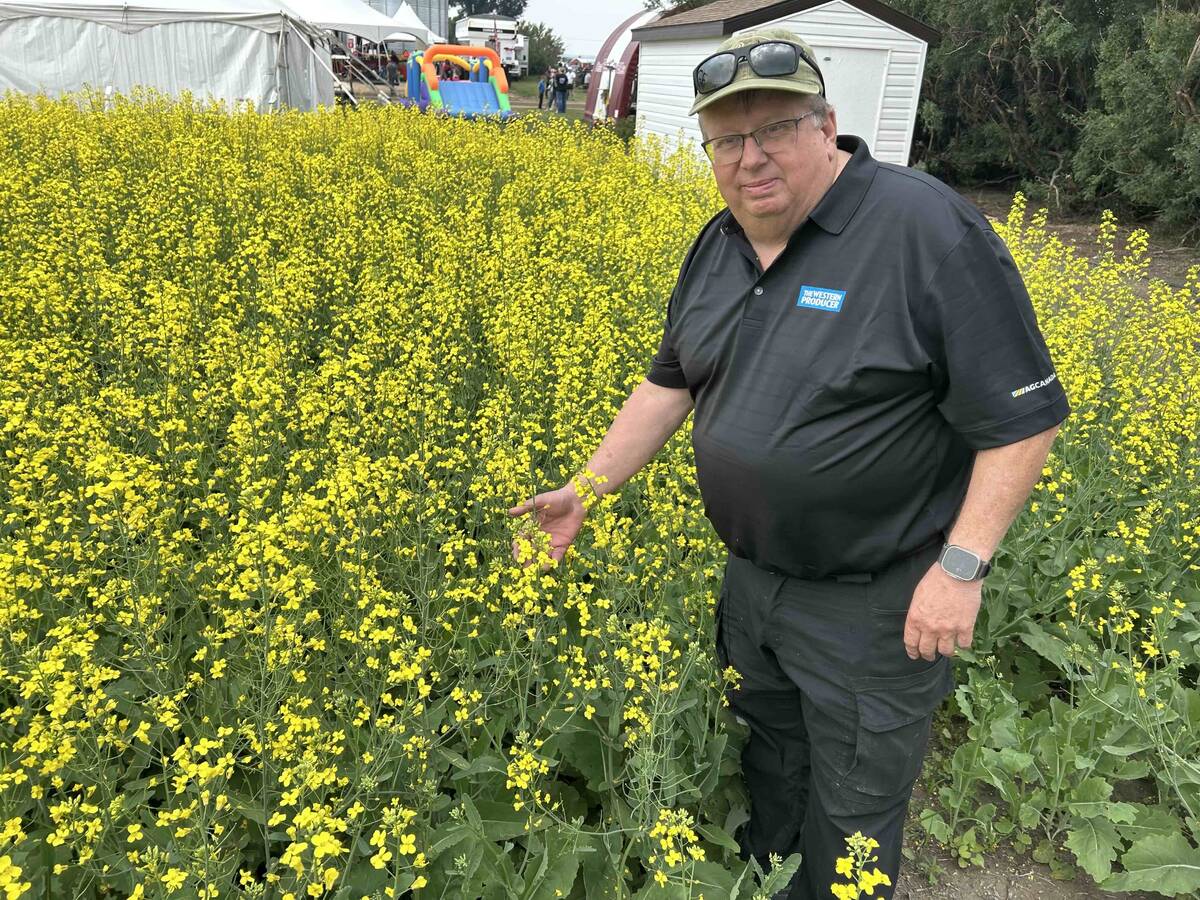
Crop conditions a pleasant surprise
Market analysts found some stressed crops and some good ones on pre-Ag In Motion 2025 crop tours,
Sales of seaweed worldwide reached more than US$4 billion in 2016 and are predicted to rise to around $10 billion by 2024. Asian countries are pushing sales higher as is strong demand from the United States and Europe.
This increased demand has become so strong that one company in the United Kingdom harvesting and processing the algae in the outer Hebrides, off the northwest coast of Scotland, is expanding its production facilities to meet demand.
Hebridean Seaweed Company Limited is the largest industrial seaweed processor in Great Britain and is based on the Isle of Lewis.
With crystal clear waters to harvest from, the company was set up at Arnish Point near Stornoway by Martin Macleod and Malcolm Macrae, both of whom are from the nearby village of Leurbost.
Currently, the production plant is undergoing an $11.8 million expansion project to cater for increased demand for seaweed products. Hebridean Seaweed already produces about 5,400 tonnes of seaweed per year but demand is growing.
Macleod, who is the company’s managing director, said about 95 percent of the company’s production is headed for agricultural and horticultural markets. Another five percent goes for food production and the cosmetic industry.
“In the agricultural sector, we mostly supply business to business including Glenside Organics in Scotland and Trouw Nutrition and also to some fish feed manufacturers” he said.
“We harvest the seaweed from the sea, which is ultimately owned by the Queen. We have agreements in place with the Crown Estate and local private estates to exclusively harvest ascophyllum nodosum throughout the Western Isles.
“Harvesting takes place all year round and the cutting is carried out mechanically using a fleet of seaweed harvesting boats that I designed and had built exclusively for us.
“We work very closely with Scottish Natural Heritage and SEPA to ensure the seaweed harvesting is sustainable and environmentally friendly.”
Although manual cutting of the seaweed was once the favoured method of harvesting, mechanical harvesting is now preferred. The boats works close to the shore and cut the seaweed as the stalks float above the seabed.
It is then filled into sacks and towed by a small boat to a sheltered area for loading onto a lorry. This method of harvesting is environmentally friendly and sustainable because only the tops of the stalks are cut, which allows the seaweed to regenerate in a relatively short time.
“We have a licence to harvest 12 hours per day but we keep it at around six to eight hours to ensure sustainability in regrowth,” said Macleod. “Up to 40 tonnes of fresh seaweed is harvested per day, which equates to around 10 tonnes of processed seaweed as the ratio of fresh seaweed to processed product is around four to one,” he said.
When the seaweed arrives at the processing plant, it first must be dried and then milled into the product requested by each customer.
Macleod is currently looking at different ways of drying seaweed including air drying to see which method is best.
As part of the new production facility under construction Macleod is installing new technology to ensure increased efficiency of energy and production methods.
“It extends to 3,250 sq. metres of covered facility and a further 17,000 sq. metres of yard space, which is probably Europe’s biggest seaweed factory.
“We hope to have the unit completed within 10 months from starting as we have customer orders to honour and we will.”