If it can be automated, it will be automated.
Farmers and other entrepreneurs continue to opt for more technology and larger-scale operations rather than deal with employees.
Recently, I hired a company to install eavestroughs on a pole shed used for machinery storage. I was surprised when a one-person operation arrived at the farm. Rather than many hands and ladders, he used remote control lifters from anchor points installed on the roof.
In a few hours, he single-handedly had the eavestroughs and downspouts installed and he was loading up to move to the next job.
Read Also
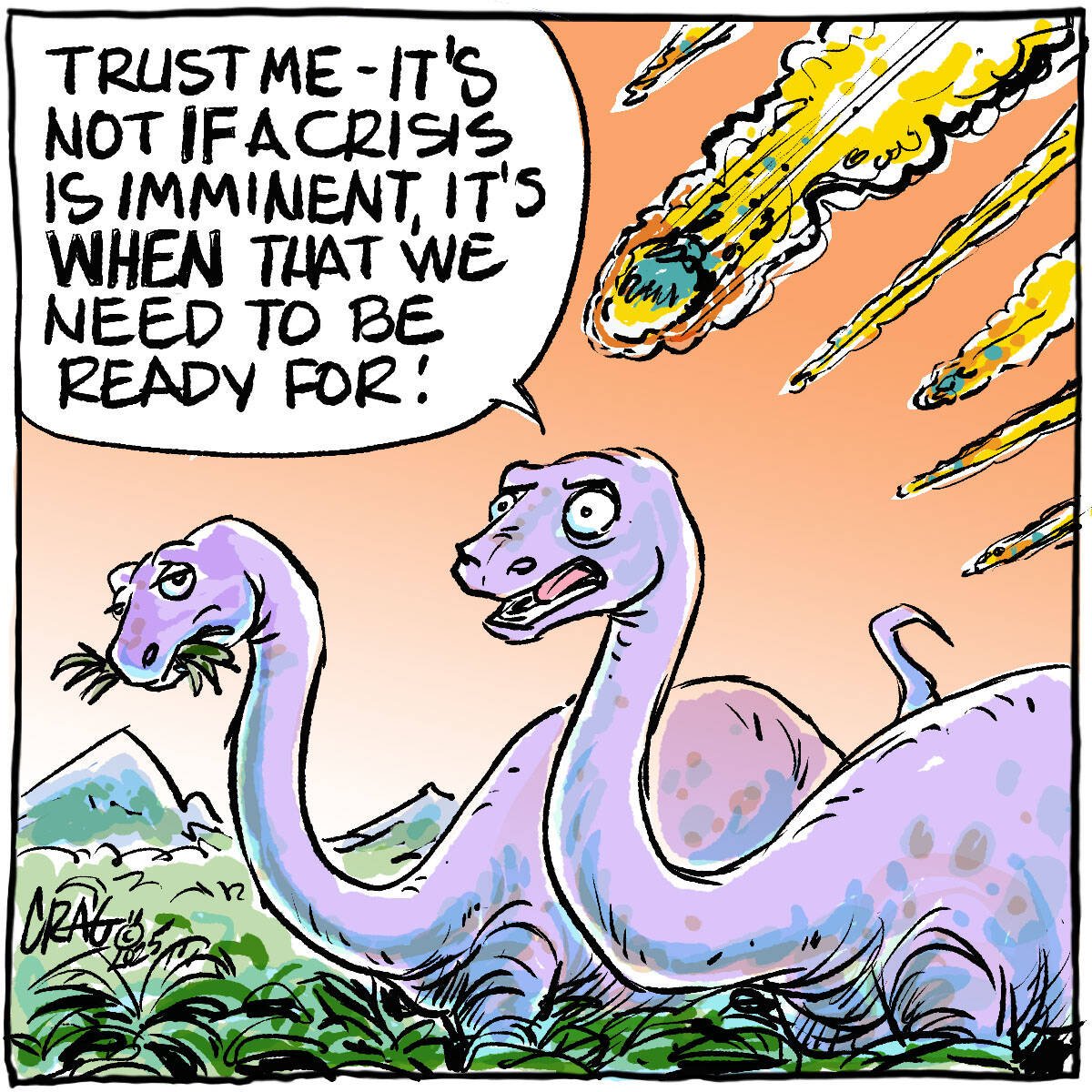
Proactive approach best bet with looming catastrophes
The Pan-Canadian Action Plan on African swine fever has been developed to avoid the worst case scenario — a total loss ofmarket access.
He has a telehandler and scissor lift in his big trailer pulled behind a tractor semi, which is complete with a sleeper for wherever nightfall finds him.
He used to be less automated and rely on a work crew of about four people, but he got tired of dealing with employee problems. For him, that was stressful. He couldn’t find enough people he considered reliable.
Now he doesn’t have to deal with employees who don’t show up on time or who have alcohol or drug problems. He doesn’t have to worry about where the crew is going to eat or where they’re going to sleep as he meanders from job to job across Alberta and Saskatchewan. And he doesn’t have to worry about employees following safety rules.
It must be noted that many entrepreneurs and especially farmers don’t make good employers. They’re driven to get the job done and they expect workers who are just as committed. That level of commitment can be hard to find if the only motivation is an hourly wage.
In grain farming, there’s a relentless drive to bigger, higher capacity equipment. With more people, the work could be accomplished with a much lower capital investment, but few farms operate that way.
The farms with a sizable crew are typically running some of the largest equipment available. You don’t see many that opt for smaller equipment and a bigger complement of workers. Family labour is usually the first line of defence. Then comes full-time employees followed by seasonable workers.
Some farms seem to do a great job with employee satisfaction and retention, but in many cases, a high turnover rate from one year to the next makes training and supervision a challenge.
On farms with sizable pulse crop acreage, the starting point for an employee running equipment is often the land roller. It’s a forgiving venue for learning how GPS guidance works and there aren’t as many things to go wrong.
A seeding outfit can also be relatively simple to drive when everything is working correctly, but an experienced employee will recognize problems that novices would miss. As for the high clearance sprayer, that isn’t a job for an entry level employee.
Grain farms do have a big advantage. It isn’t manual labour like that required at many fruit and vegetable operations and there’s a large pool of people with some background in grain farming.
But maintaining a competent and committed workforce is still a big challenge and that challenge is magnified as a farm grows beyond what family members can accomplish.
This is probably a factor that has slowed the expansion of mega farms. Farming big can provide advantages when buying inputs and when marketing a large volume of product, but finding and retaining motivated and competent employees can be an Achilles heel.