Farmers are asked to contribute $200 per acre to supply the processing facility with feedstock to produce dextrose
FOREST, Ont. — Ontario farmers have been told they can expect payback in little more than three years from a $200-per-acre investment in a new co-operative.
Proponents of the Cellulosic Sugar Producers Co-operative (CSPC) talked about the opportunity at a Nov. 8 field day here, which also featured equipment demonstrations for corn stover harvesting.
“We need about 55,000 acres, which will give us 750,000 metric tonnes of feedstock,” said Jim Campbell, general manager of AGRIS Co-operative.
“This will be the first commercial plant of its kind, which produces high-purity dextrose specifically for bio-based chemical production.”
Read Also
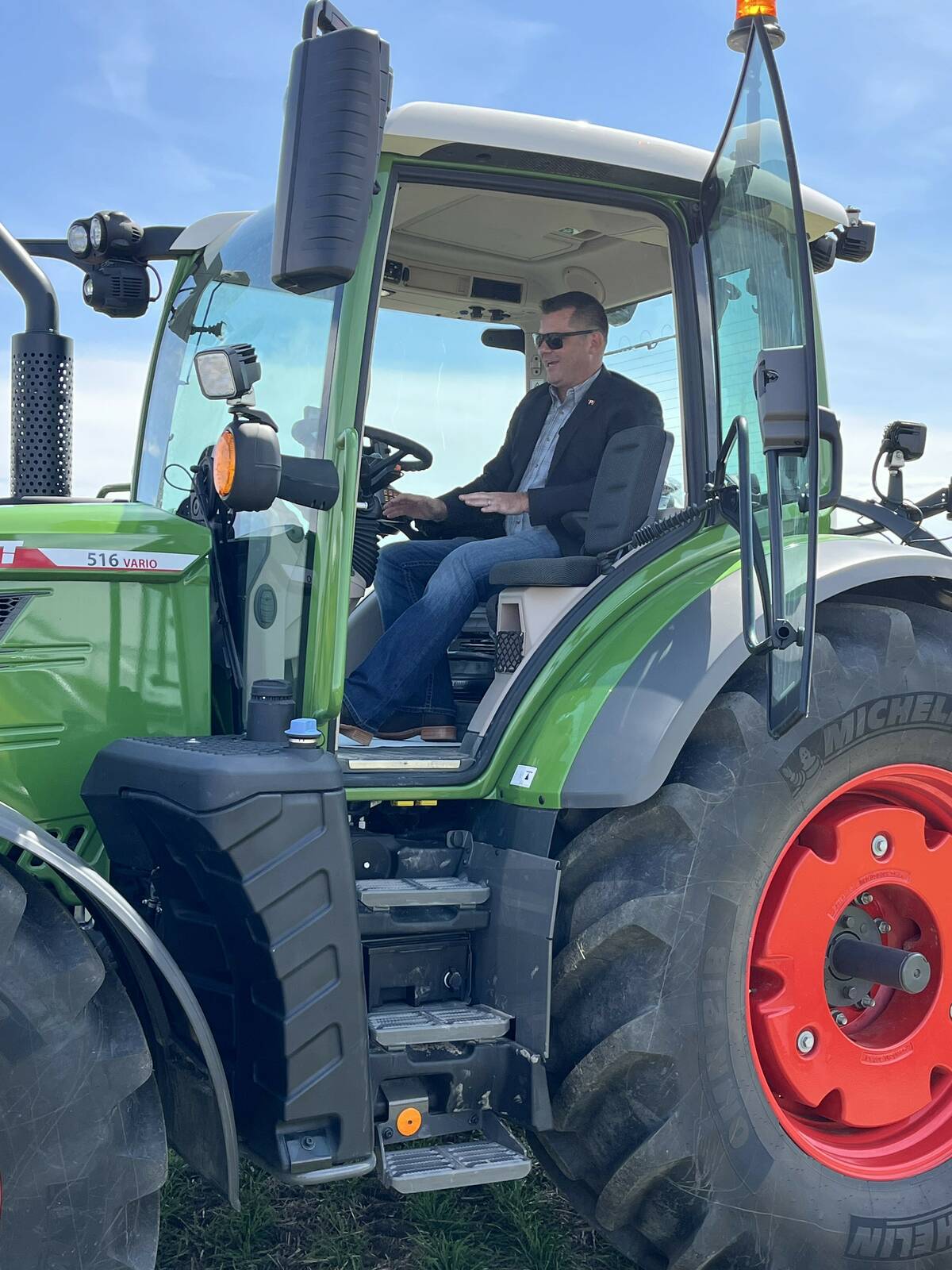
Farming Smarter receives financial boost from Alberta government for potato research
Farming Smarter near Lethbridge got a boost to its research equipment, thanks to the Alberta government’s increase in funding for research associations.
While AGRIS is not directly involved, Campbell has been helping get the new co-operative off the ground.
Plans call for farmer members to have about a 30 percent stake, about $11 million, in a processing plant to be located in Sarnia, Ont. It is expected production will begin in 2018.
The capital cost of the plant, which will be operated by Comet Biorefining, is expected to be about $70 million, Campbell said.
Comet will be contributing and money is to be raised through a $10 million loan from the federal government and $20 million from the banking community.
Andrew Richard, Comet founder, said his company has developed a low-cost approach for the conversion process. Proven at a demonstration plant in Italy, the system replaces the traditional pre-treatment of biomass and reduces enzyme loading, he said.
Among Comet’s investors is BioAmber, which already operates a plant in Sarnia.
While Richard didn’t provide details, he said Comet’s process doesn’t require a large processing facility. That allows feedstock to be secured within a relatively small geographical area, specifically, within 100 kilometres of the plant’s location.
CSPC is to be 100 percent farmer-owned. Its role is to secure a steady supply of biomass, corn stover and wheat straw. Co-op members are to receive $42 per acre on average for the biomass they deliver and dividends from their investment in the processing plant of $20 per acre.
There is to be no financial risk to producers until the plant is commissioned, Campbell said. The co-operative is expected to invest in biomass harvest equipment, such as tractors, balers, bale accumulators and flail choppers.
Jay Cunningham, who retired earlier this year from the banking industry, has been hired as general manager of CSPC.
“It’s a very well-planned venture,” he said.
Dave Park, chair the CSPC board of directors, said removing crop residue benefits farmers.
“Some of the newer corn varieties don’t break down like they used to,” he said.
“On our farm, we’ve had to go back to primary tillage. Others have gone to strip tillage.
Park said residue removal adds another revenue stream, a welcome addition to farming operations, especially when commodity prices are poor.
Research, carried about by a Sarnia-based research group, Bioindustrial Innovation Canada, has shown that some crop residue can be removed without a negative impact on the soil. Crop residue is already being harvested in the United States for the production of cellulosic ethanol.
With corn stover, the removal rate is to be from one to 1.5 tonnes per acre. According to Campbell, it’s impractical to remove more.
Charlie Lalonde, who’s been working with co-operative members on behalf of the Ontario Federation of Agriculture, said there are restrictions for stover removal. For example, if the grain corn yield is less than 150 bushels per acre, no stover should be removed.
An area dealer, Advantage Farm Equipment, demonstrated the type of harvesting equipment used for residue removal in the United States.
A Hinniker flail chopper equipped with an auger chopped and placed the stover in windrows. A beefed-up Massey Ferguson unit packed large square bales weighing around 1,500 pounds each. A ProAG bale accumulator picked up the bales.