Fargo, N.D. – Can a modern tractor run on a blend of 99 percent hydrogen and one percent diesel? Bob Pieri hopes to find out this year.
“The idea is to push the ratio of hydrogen as high as possible,” said Pieri, a mechanical engineering professor at North Dakota State University.
“Theoretically, we can get the diesel down to one percent or a half percent of the total fuel blend. Practicality may be different. In reality, we may only get the diesel down to five or 10 percent of the blend.”
Read Also
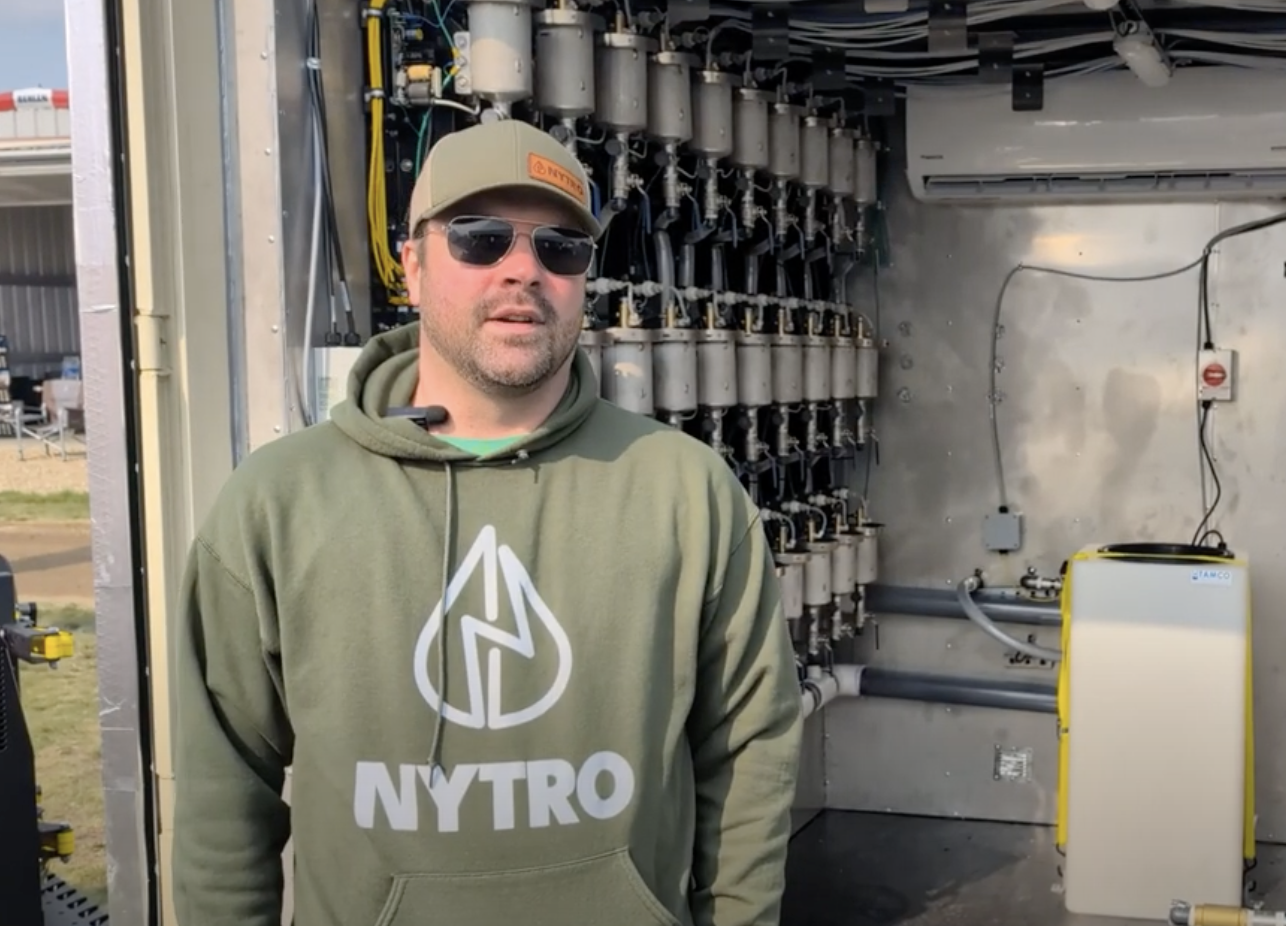
VIDEO: Green Lightning and Nytro Ag win sustainability innovation award
Nytro Ag Corp and Green Lightning recieved an innovation award at Ag in Motion 2025 for the Green Lightning Nitrogen Machine, which converts atmospheric nitrogen into a plant-usable form.
Pieri said hydrogen burns cleaner than petroleum diesel and biofuel alternatives, and it is cheaper to produce from wind and water. He said biofuel also requires diverting land use to fuel crops from food, and they still emit pollution.
The need is to reduce burning of both petroleum and biofuel.
Pieri said the university was approached by Agco to see how much hydrogen could be burned in a six-cylinder Perkins powered Challenger.
He said NDSU had already converted three gasoline engines to run on hydrogen, but getting a modern diesel engine to run on a high ratio of hydrogen would be more significant.
“The self ignition temperature of hydrogen is higher than either bio or petroleum based diesel fuels. So it’s not an ideal candidate for running a diesel engine. You need something other than a spark plug to light it up.
“Self ignition for hydrogen is up around 500 C. Self-ignition for diesel is only 280 C. To achieve self-ignition with hydrogen, you’d need to double the pressure. You’d need a compression ratio of 50:1 or 60:1. And if you did something like that, the explosion in the combustion chamber would be so massive, it just would not be workable.”
Some engineers have already added combustible gases such as propane or natural gas as a boost element on top of diesel fuel to gain more power.
“We’re not doing that. We don’t want to use hydrogen simply as a boost element on top of diesel. We’re using hydrogen to replace diesel.
“Researchers in India now are playing with a very complex series of timed injectors at the inlet ports. They have injectors for diesel and injectors for hydrogen. It’s complicated.”
Pieri said engineers in Tasmania found that a couple drops of diesel injected into the chamber when the piston is at the top, dead centre, is enough to ignite hydrogen.
“The Tasmanians found that as soon as the initial blast from the self-igniting diesel touched the hydrogen – bang – it ignites like crazy and combines instantly with oxygen.
“It’s a very immediate and powerful blast of power because hydrogen has such a rapid flame speed.”
It’s the same rapid flame speed that destroyed the Hindenburg, a 1937 hydrogen-powered airship.
“The flames we see in the film and old photos of the Hindenburg are not burning hydrogen. The hydrogen was all burned off by the time anyone saw flames. It flashed away instantly.”
The flames in the photos, said Pieri, are burning paint.
The difficulty of working with hydrogen is its unstable nature when in a gaseous state and because it boils at -253 C, it exists as a gas at temperatures above that.
“To contain the hydrogen, our tanks are rated at 5,000 psi.”
Pieri said the NDSU team is taking the Tasmanian rather than the Indian approach. He emphasized they are not adding hydrogen injectors for each cylinder.
Instead, NDSU infuses hydrogen into the airflow just before the intake manifold. The hydrogen blends into the turbocharged airflow and passes through the intake valves on the down stroke.
The gas is compressed on the up stroke. The injector squirts in a few drops of diesel at the right moment. When the diesel self-ignites, it causes the hydrogen to ignite.
“A couple of ignited drops of diesel are all it needs to fire the hydrogen. Just a couple of mistlets.”
Pieri said the university has so far pushed a four-cylinder diesel up to 45 percent hydrogen with no drop in horsepower or rpm. He added the exhaust from both their hydrogen conversion engines is clean and green.
“We began seeing significant emission reductions at only 10 percent hydrogen.”
Now they need to look further into the timing of the diesel injection event, said Pieri.
“Because of the speed of the flame front with hydrogen, the pressure points we plot (on the power stroke) are earlier than diesel. That’s why timing of the injection is vital if we want to get up to optimal levels of hydrogen and maximum power.”
However, adjusting the injection timing is not simple.
“On a modern diesel, all the controls are electronically locked into a proprietary computer module. We can’t play with the injection system like we used to in the old days.”
The university is working with an older model engine that has a manually controlled injection system. But for the Challenger, NDSU has researchers working exclusively on the control module.
The NDSU conversion uses all the original fuel delivery parts, but they function in a different way.
“In a regular diesel, rpm and power are controlled by the amount of liquid diesel fuel going through the injectors,” said Pieri. “But on converted engines, we control the fuel supply at the air inlet. Hydrogen to create power and rpm comes through the intake manifold. The throttle now controls the hydrogen flow rate instead of the diesel injection pump.”
He said pressure at the intake manifold from the turbocharger is about 30 psi.
“We need to run enough hydrogen pressure so we don’t get air infusion back into the hydrogen supply. So we regulate the hydrogen down to about 90 psi.”
The turbo pumps air according to engine rpm, as it did before NDSU converted the tractor. At higher rpm, it pushes more air into the engine.
Eventually the operator will be able to select different hydrogen/diesel blends from inside the cab.
Pieri said safety is an obvious concern when working with pressurized gaseous fuel and hydrogen is no different.
“It goes off pretty quickly. It doesn’t take very much of a spark. You must be very respectful of hydrogen.”
Another issue is the lubricity. Pieri said the lower lubricity of hydrogen may compel his team to maintain a higher diesel percentage to lubricate the cylinder walls.
Hydrogen embrittlement is another concern.
“Because hydrogen molecules are so much smaller than the molecules in steel, the hydrogen is able to pass between the grain of the steel and crack it open.
“This might be particularly troublesome on the intake valve stems with all that hydrogen passing over them. A normally ductile steel can become very brittle when exposed to hydrogen. We’ll need a lot of test time on the engines to find out more about this factor.”
He said that even if the problem is severe, the exposed parts can be hardened by a surface treatment with boron, brillium or some other trace element.
To get the necessary number of working hours on hydrogen conversions, Pieri is negotiating with other tractor manufacturers to put more tractors into his program.
As well, backfiring has been a problem with hydrogen conversions on gasoline engines. Pieri thinks the spark plugs heat to several thousand degrees each time they fire, but don’t have time to cool down. He thinks it likely will not be a problem with diesel engines.
For more information visit www.ndsu.nodak.edu.me.