SANFORD, Man. — Delta owners vow they’ll never go back to their previous tractor, just as Quadtrac owners once swore off going back to round rubber.
Versatile started with the premise that simply bolting triangular track sets to its big four wheel drive machines wasn’t good enough to make the cut. It felt that the next step forward in rubber track tractors demanded new engineering if it truly expected to put its Delta one giant step ahead of the competition.
The bet seems to be paying off.
Versatile refuses to disclose sales figures, but it said that Delta production numbers are now higher than its four wheel drive numbers.
Versatile engineers worked with Camso (formerly Camoplast) to closely examine the weak points on other rubber track systems and attempt to eliminate them on the Delta. The confidence factor in the new design is high enough to earn the new rubber track a prorated warranty of four years, or 2,500 hours.
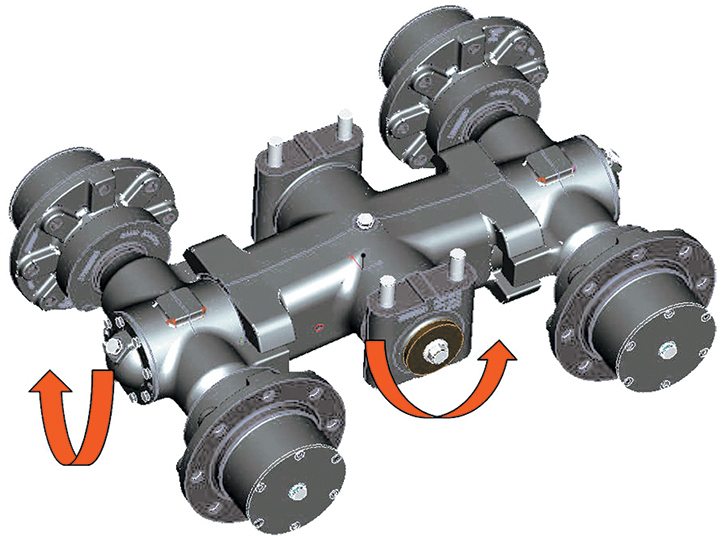
Camso had been concentrating its efforts on the next logical step in the evolution of rubber track design. It had new technology that it was ready to put into production and was looking for a company that wanted a high calibre rubber track system for the latest high horsepower tractors. Versatile was its choice.
“Our guys worked closely with Camso on every detail. The bogie wheels and idler gears are easily replaced. You simply unbolt them, install the new ones and bolt them up again. On other tractors, you have to pull the bearings apart. We don’t do that,” said Delta product manager Del Fast.
“Track alignment is simple on the Delta. On our competitors’ tracked tractors, you have to remove numerous bolts and shift the frame. On the Delta, we have two bolts with lock nuts. The very first time, it takes about an hour, but there’s so little stretch in the track that you generally never have to bother with it.”
Read Also
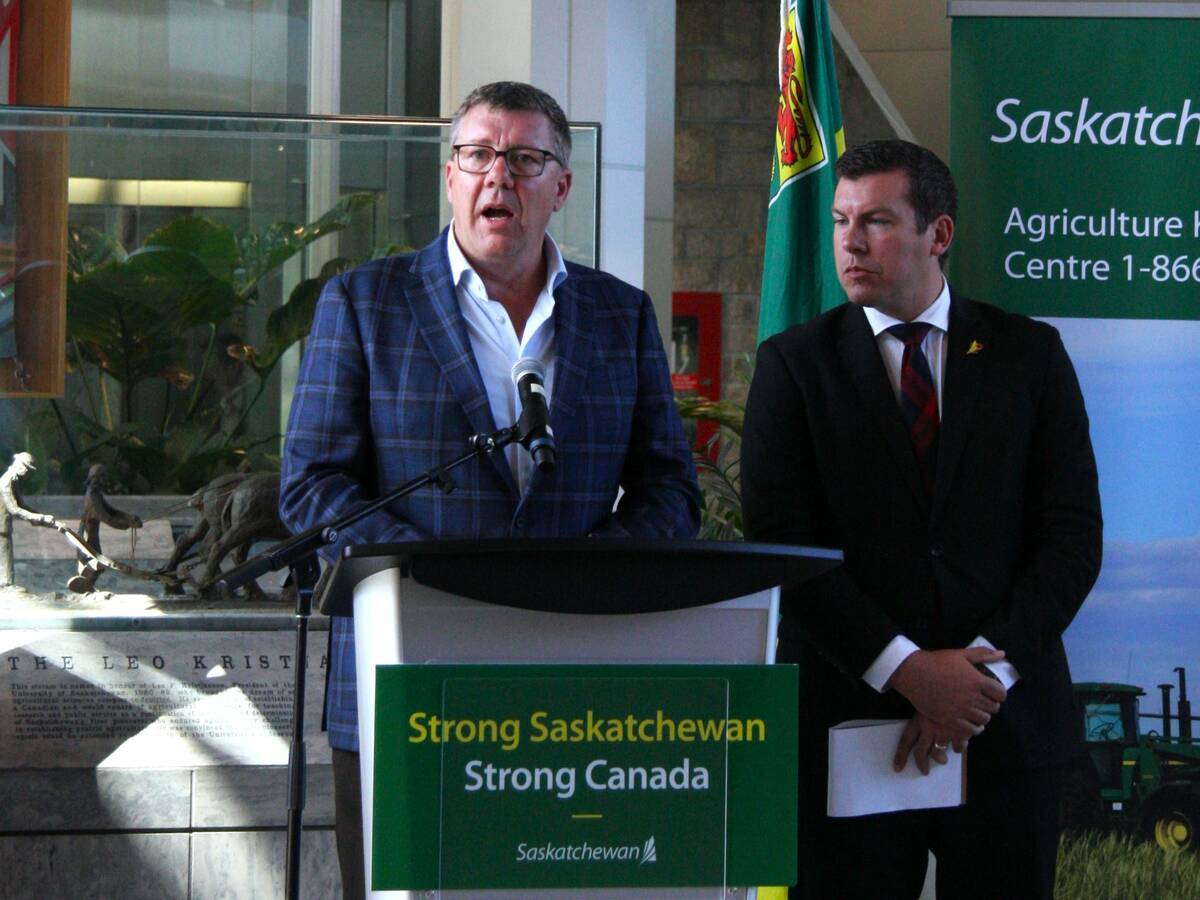
Key actions identified to address canola tariffs
Federal and Saskatchewan governments discuss next steps with industry on Chinese tariffs
The double axis bogie system is about as close to independent suspension as can be achieved on a rubber track tractor. From a conceptual point of view, it’s like the difference when 4×4 pick-up trucks switched from solid buckboard front axles to independent front suspension with CV joints.
The mounting system improves torque and weight transfer and helps reduce shock load.
The pivoting bogies force the tracks to closely follow the soil surface by permitting massive changes to the bogie geometry.
The frame holding the bogie wheels is mounted in bushings so the pitch oscillates 12 degrees fore/aft and the roll oscillates 12 degrees side to side. In effect, each rotating rubber pad is free to crawl over the soil surface using the best contact angle within those 12 degree geometric parameters, regardless of what the other three pads are doing.
Fast said the bushings run in an oil bath, so they should be good for the life of the tractor.
“Drive lugs on our track are 8.5 inches wide, considerably wider than anything our competitors have,” he said.
“We use an 81 degree wrap drive sprocket, so seven drive lugs are engaged at all times. There’s a lot less chance of it ever slipping, and the track is going to last way longer.”
Two side-mounted fuel tanks hold a total of 475 U.S. gallons and have a cross-over tube so that they can be filled from either side. They are located mid-point on the tractor so that 50-50 weight distribution front/rear is maintained whether the tanks are full or empty.
“At our test track here, we can really beat up on a tractor,” Fast said.
“In a couple weeks, we put on as much wear and tear and abuse as any tractor will see in a lifetime. We’ve seen our Camso tracks last slightly longer than tires in bad conditions. However, if a farmer is roading a lot or working on side slopes, track life will be slightly shorter than tires.”
It’s the bean counters who often have the final say in the quality of any manufactured product, but Fast said cutting corners on component costs was definitely not part of the Delta design process.
“We build the Delta to go long periods without maintenance or problems, so we do things like using only long-life bearings with metal-faced seals,” he said.
“Our bearing supplier tells us we can go 2,000 hours before you need to change the oil.”
The outboard planetaries that allowed broken axles to be re-placed in the field were once a significant promotional feature for Versatile. The practice was fraught with the risk of exposing the hypoid to destructive contaminants, but it was more efficient than dragging the tractor back to the yard or to town. Besides, the hypoid could always be changed next time the tractor was in the yard.
“That’s not a factor anymore. Broken axles are history,” Fast said.
“Metallurgy has come a long way. We just don’t see broken axles today.”
Fast said there’s been a major shift in the thinking of farmers buying rubber track tractors. Farmers bought tracks 20 years ago so they could keep working in mud. Today, compaction and aerial images that show compacted tracks are the biggest motivators.
“The drone images are showing guys the compacted tire lines in fields worked with tires,” he said.
“On a field worked with tracks, you can hardly see where the tracked tractor went.”
For more information, contact Fast at 204-619-4083.
ron.lyseng@producer.com