Is it possible to develop brake technology capable of hauling 235,000 pounds of iron on the highway at 55 m.p.h.?
Brian Olson of Power Pin hitching systems doesn’t know exactly how we’ll do it, but he does say it’s necessary, and he does have an idea of the kinds of questions we should be asking.
“For one thing, we have to look at the difference between hydraulic brakes and air brakes. When an air system comes disconnected, it throws the brakes on instantaneously and automatically. European tractors use air brakes when towing carts, so that technology has been proven for decades.
Read Also
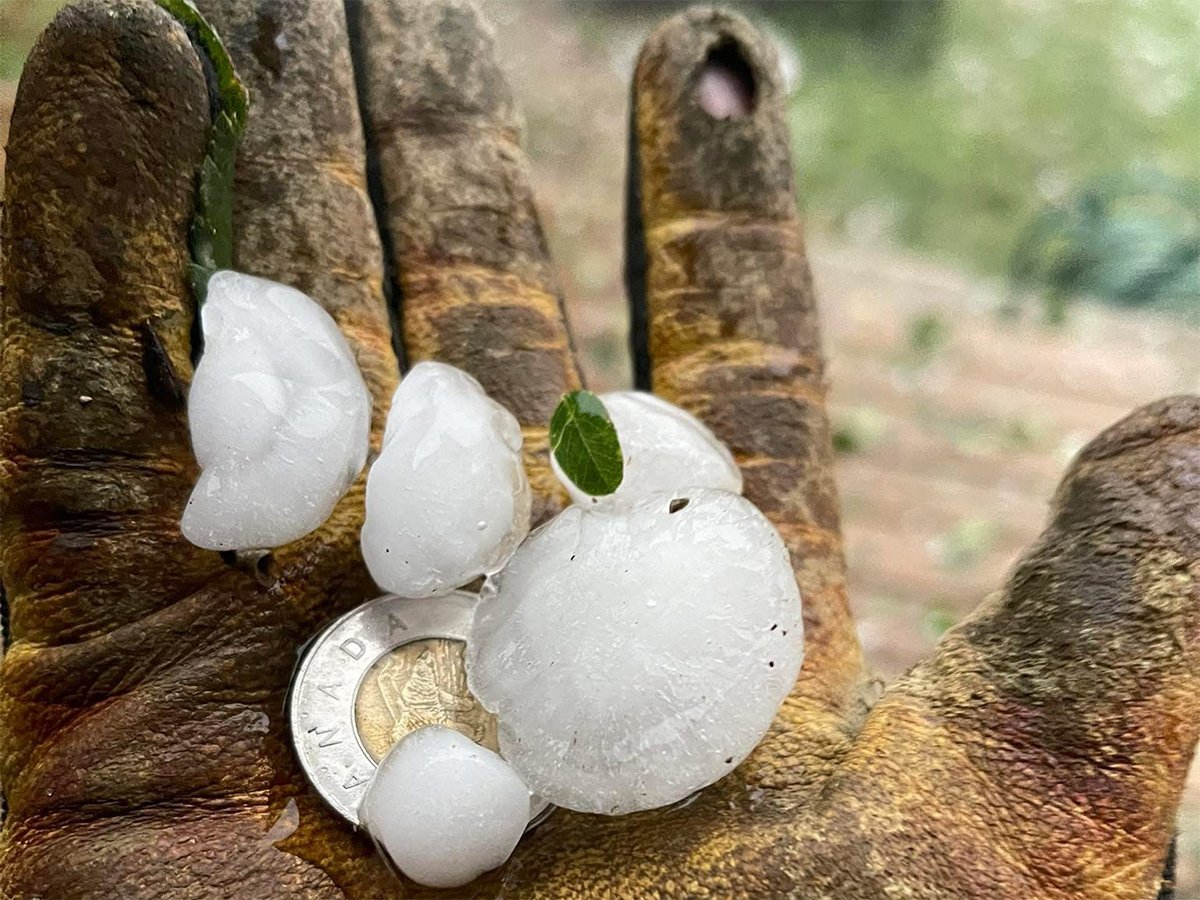
Half million acres of Alberta crops affected by massive hail storm
Late August hail storm catches farmers in prime harvest mode, damaging half million acres of crops in Alberta.
However, Europeans don’t pull the big loads we do this side of the Atlantic.
“North American manufacturers want hydraulic brakes because they’ve already invested heavily in these big capacity hydraulic systems, but hydraulics take time to obtain full braking force. They don’t engage quickly enough. You need instant response. Plus, you need the trailer brakes to throw on milliseconds before the tractor brakes so you don’t jackknife.
“If there’s a disconnect with hydraulic brakes, you lose all braking force. If there’s a disconnect with air brakes, the trailer brakes clamp on immediately. Hydraulic brakes simply don’t cut it for trailers. That’s why we’ve had air brakes on highway rigs forever. That’s what we need on farm trailers.”
All four major North American tractor manufacturers offer air brakes for towed implements. As well, there are numerous aftermarket kits. The real issue is that very few towed implements have brakes.
Olson said whether the industry adopts air actuated brakes or hydraulically actuated brakes, the big question remains: how do you create enough friction to stop 235,000 lb. of mass, especially if you’ve allowed it to run down the road at 55 m.p.h.?
“Look at the air brakes on an 18-wheeler. There’s 10 individual braking systems on a rig that has a maximum GVW of just 80,000 pounds. But a big four-wheel grain cart only has four tires. There’s only space for four friction points. Is that enough contact area? This is a big challenge for the engineers and the people who write the rules.”
The next step is deciding between drums and discs, which involves availability of space and what technologies are needed to reduce speed safely and deal with heat generation. Technologies exist in Formula One racing and in electrical generation braking, but bringing them to agricultural applications may still be in the distant future.
European ag manufacturers are gradually switching to electric motors to replace hydraulic and mechanical components. Their three main reasons are better efficiency with electrical, more precise control and the fact that it’s easier to route electrical cables than hydraulic lines or drive shafts and belts. Power generated from braking could be used in equipment operation.
Olson said it’s up to the engineers to figure out how to accomplish it. His main emphasis is that the industry must take major steps soon in getting high performance braking systems on carts and trailers.
“Sooner or later somebody has to step up and say enough is enough. Our industry must take the bull by the horns and regulate ourselves and makes these changes or we’re headed over a cliff. So far, we have not taken those steps..… That school bus full of kids, that’s exactly what the issue is all about, isn’t it. God help us the day that happens. This is something we can prevent. We have the choice right now.”